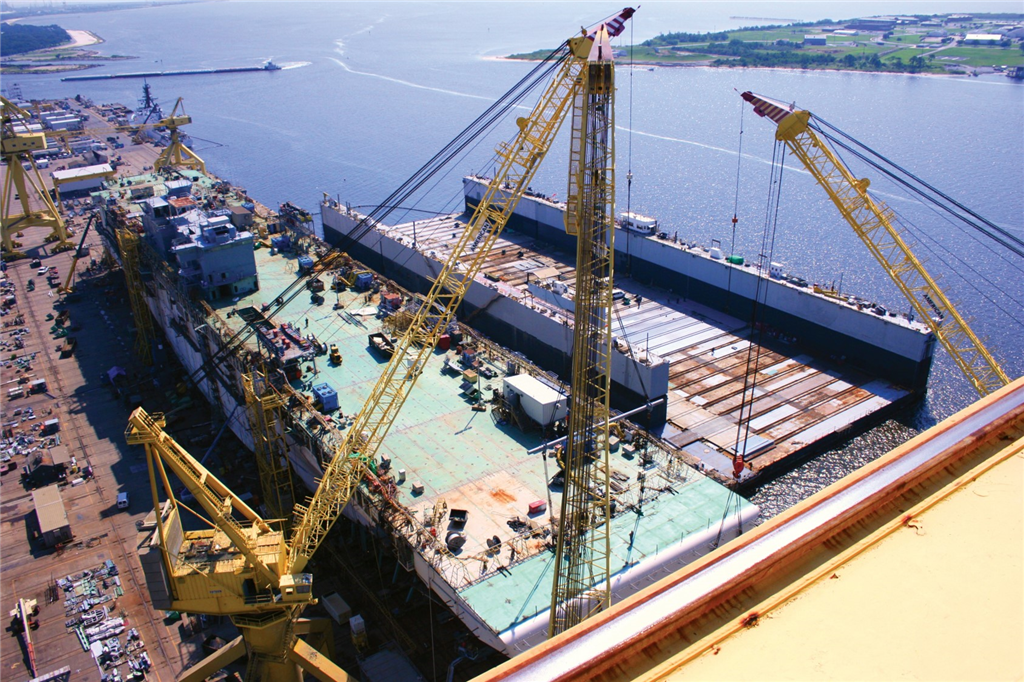
Spending an Hour per Day on Non-Value-Added Activities
For many shipbuilding operations, fabrication typically begins in a workshop before moving outside to the shipyard for completion. In both of these environments, a welder could be several hundred feet away from the welding machine. For example, the point of the welding could be in a confined area of the vessel and the power source could be on a mezzanine.
Currently, a welder usually spends 15 minutes per trip walking back to the power source to make changes to welding processes or parameters. Even with a conservative estimate of 4 walks per shift, a welder could be wasting 250 hours on the jobsite every year. For larger shipyards that employ more than 100 welders on the jobsite, the loss in productivity due to unnecessary walking can be significant.
What if all unnecessary walking can be eliminated? Can the productivity gains result in significant improvements to the shipyard’s bottom line?
Complete Control at the Point of Welding
In shipbuilding and ship repair applications, it is common for welders to switch between different welding processes such as flux-cored arc welding (FCAW), stick, TIG and even carbon arc gouging. With advanced remote-control solutions such as Miller’s ArcReach technology, a welder can control all these processes at the point of welding without having to walk back and forth to the power source. This technology does not require separate control cables, thereby eliminating the time and money that is usually spent on maintaining or repairing expensive control cables.
The XMT 400 and ArcReach Suitcase 12 system also offers enhanced ArcReach capabilities such as Cable Length Compensation, or CLC™. CLC ensures that the voltage the welder sets at the wire feeder is the voltage they get, even hundreds of feet away from the power source. This allows greater accuracy and easier control of weld quality.
With point-of-use control technology, welders can also see the exact amperage and voltage, and easily adjust welding parameters as needed to ensure they are staying within specified welding procedures. Welders no longer need to “get by” with less-than-optimal welding parameters.
Improving Jobsite Safety
Slips, trips and falls are among the most common causes of jobsite injuries and death. Given that most shipyards have a sizable operation, there can be numerous obstacles between the point of welding and the location of the power source. Eliminating unnecessary walking in the expansive jobsite can contribute to improving the safety of the welders, since they will be exposed to fewer slip, trip and fall hazards. This can contribute to the shipyard’s goal of achieving zero lost-time incidents.
Improvements in safety can also reduce the cost associated with worker downtime, insurance and compensation payments, thereby improving the shipyard’s bottom line.
A Solution that Provides a Competitive Edge
As competition for contracts intensifies in the shipbuilding and ship repair industry, shipyards have to deliver vessels under tighter schedules, lower costs and increasingly stringent quality requirements. One solution is to invest in advanced remote-control welding technology that can help shipyards complete vessels faster without compromising on safety or quality. The investment will be paid off quickly thanks to significant productivity gains and time savings.