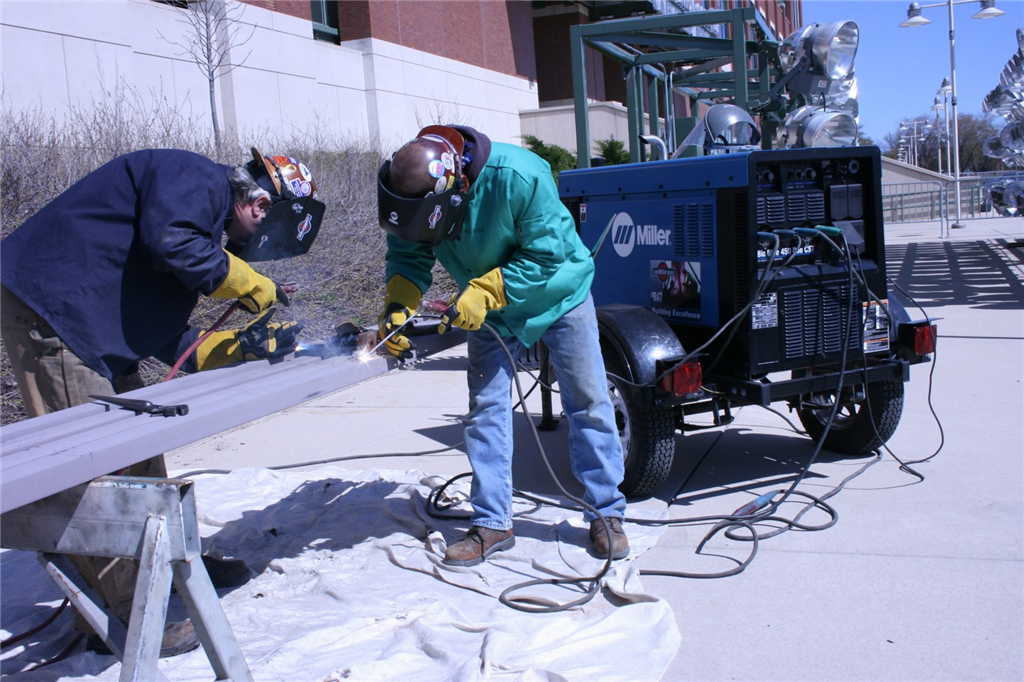
In the construction industry, contractors are finding it a challenge to complete jobs on schedule and within a competitive budget. This is mainly due to external pressures such as rising costs of fuel, materials, labour and equipment, and increasing government regulations.
Since welding plays a significant role in the construction industry, many contractors have begun searching for new welding tools that can help them boost efficiency while lowering overall operating costs. A dual-operator diesel engine welding machine is one such tool that many contractors are considering over the traditional single-operator variant.
Traditional Single-Operator Machines
When contractors choose to use a single-operator machine, it usually means that one machine needs to be purchased or rented for one welder. When there are more machines in the fleet, this leads to higher transportation and logistics costs, especially in expansive jobsites. Since every machine has a diesel engine, a larger fleet also results in higher service and maintenance costs. In addition, operating multiple diesel engine welding machines in a project site contribute to higher fuel consumptions, excessive noise pollutions and larger emissions of impurities and pollutants.
New Dual-Operator Solutions
With new technology advancements, dual-operator diesel engine-driven machines from Miller can address the above-mentioned challenges by providing enough power for at least two welders. These dual-operator machines also have enough auxiliary power to operate additional inverter-based welding power sources or tools. Because the weld terminal and the auxiliary power are completely independent, the welder can weld and operate a variety of tools using the auxiliary power without negatively impacting the quality of the welding arc.
For example, the Miller Big Blue® 800X Duo AirPak is capable of producing 800 amps for one welder, or 400 amps each for two welders, with three-phase auxiliary power available at the same time. It is common for contractors to run tools such as grinders, lights and plasma cutters off the auxiliary power. If required, the equipment can even be used by as many as six welders at once, each welding a 3.2mm diameter stick electrodes at 120 amps. This configuration can boost productivity significantly without having to add more machines or renting larger generators.
Jobsite Benefits
Being able to do more with one machine is a big benefit for leading contractors such as Miron Construction. In mobile jobsites where the equipment must be set up and moved multiple times during the day or week, Miron only had to manage half the usual number of welding machines. This helped to reduce the logistical costs and planning involved. In addition, the ability to have more welders working from one dual-operator machine was also a key consideration for Miron because they could minimize the clutter and save space in the cramped jobsite, thereby promoting efficiency and improving jobsite safety. By reducing the amount of equipment on a jobsite, while maintaining or increasing productivity, makes it easy for Miron to see the return on investment of these dual-operator machines.
A dual-operator diesel engine-driven welding machine can offer a full range of jobs and options for multiple welders, while saving space on a jobsite and enhancing efficiency. Contractors will benefit from a lower cost-per-welding-arc due to the lower fuel consumption and savings in maintenance costs, without having to sacrifice on arc quality or productivity.