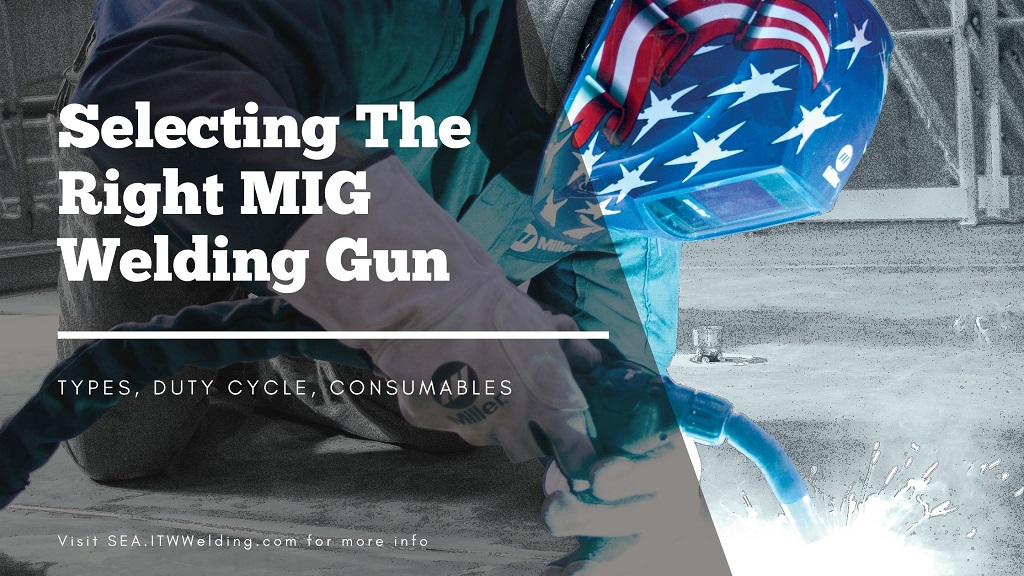
MIG welding guns are critical extensions of welding machines but are often overlooked by welding contractors. A poorly selected MIG welding gun can affect the weld quality as well as cause unnecessary downtime in production. In this article, we will discuss the different types of welding guns and the various aspects you should consider in order to choose the best welding gun for your welding application.
The Five Main Types of Welding Guns
There are five basic types of welding guns. The first type is an air-cooled welding gun which relies on ambient air and shielding gas to dissipate excess heat that builds up along the welding circuit. Air-cooled welding guns typically have amperage ratings of between 150 to 600amps. The second type is a water-cooled welding gun (typically rated between 300 to 600amps) that uses an external water-cooling system to dissipate heat from the gun. As a result, water-cooled systems are relatively more expensive and require more maintenance. However, water-cooled welding guns are generally lighter and more flexible because there is relatively less copper in the power cable.
The third type of welding gun is a push-pull gun which is predominantly used to weld soft alloys such as aluminium. A compatible wire feeder and gun system is usually required to ensure smooth wire feeding with minimal resistance. In such a system, the push motor is located at the wire feeder and the pull motor is integrated within the gun. Push-pull guns can come in air-cooled or water-cooled designs and gooseneck or pistol-grip styles. Spool guns are another type of welding gun that can be used to improve feeding of soft alloy wires. In a spool gun design, a small spool of wire (~0.45kg) is located on the welding gun. Unlike push-pull guns, spool guns are typically used for light welding applications and MRO jobs.
The last type of welding gun is one with fume extraction capabilities. Fume extraction guns help improve jobsite safety by capturing toxic welding fumes at the point of welding. These guns are usually rated between 300 to 600amps and are typically larger than regular welding guns.
Welding Application
If you are welding in the field, air-cooled welding guns are more portable and practical. Water-cooled welding guns are usually suited for welding cells in a manufacturing floor. In addition, if you are welding with 1.6mm diameter wires (and above), you can consider using a water-cooled gun. Contractors that weld with 1.2mm diameter wires (and below) typically choose to work with air-cooled guns instead. Lastly, when welding softer wires such as aluminium, always consider either a push-pull gun or a spool gun to ensure smooth and consistent wire feeding.
Welding Amperage and Duty Cycle
Choosing the optimal welding amperage for your welding gun can be tricky. A 600amps gun can be used for virtually all applications but will be very heavy and expensive. On the other hand, a 200amps gun may be cheaper and lighter, but will be less versatile, especially in demanding jobsites. Besides welding amperage, you also need to consider the duty cycle of the welding gun. Exceeding the duty cycle of the gun will decrease the service life of the gun and its consumables, which can lead to additional costs and production downtime. Taking these factors into consideration, you should have a good understanding of the average amperage and arc-on-time in your welding operation in order to determine the best welding gun for your application.
Welding Gun Components and Consumables
As a general rule of thumb, always choose the shortest welding gun cable possible for your welding operations. Shorter cables are not only lighter but can also help to minimize jobsite clutter and prevent excessive coiling that can lead to poor wire feeding.
In addition, when choosing a welding gun, always consider how easy (or difficult) it is to replace the gun liner. Traditional gun liners require the welder to measure and trim the liner to the correct length. An improperly cut gun liner can result in poor wire feeding and erratic welding arc, leading to welder frustration and poor-quality welds. There are new solutions in the market, such as the Bernard AccuLock S Consumable System, that can help eliminate these liner installation issues.
Besides the traditional fixed neck welding guns, there are also rotatable neck and flexible neck options that you can consider. Rotatable and flexible necks allow you to weld more comfortably in confined areas and in situations that require out-of-position welding. These small changes can help reduce welder fatigue and improve weld quality.
Lastly, when it comes to the welding gun consumables, such as nozzles and contact tips, there are usually two main distinctions, i.e., standard or heavy-duty. As expected, heavy-duty consumables will have a higher upfront costs as compared to the standard consumables. However, the use of heavy-duty consumables will improve your overall operating costs in the long run because fewer replacements will be required during production.
Make an Informed Decision
On top of qualifying filler metals and evaluating welding machines that will be used for a project, welding contractors should also spend some time to select the best welding gun to suit the welding application. Always reach out to your trusted welding supplier to have a further discussion and request for a demo if required.