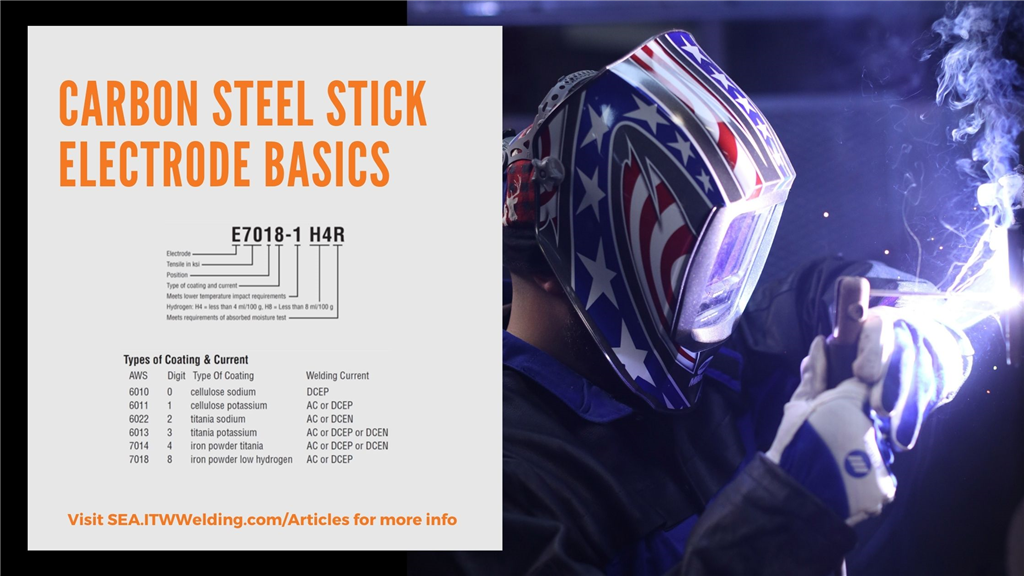
In this article, we will explore the most common stick electrodes under the American Welding Society (AWS) A5.1 Specification.
What is the Purpose of the Flux Coating?
All stick electrodes consist of a metal rod that is surrounded by a flux coating. When the arc is initiated, the flux burns and produces a shielding gas that protects the molten weld puddle from atmospheric impurities. When the weld puddle cools down, the flux forms a slag that protects the weld metal from oxidation. Manufacturers may also add deoxidizers, iron powder or other alloying elements into the flux to give the stick electrodes different properties and characteristics.
How are Stick Electrodes Classified?
AWS uses a standardized classification system that is made up of numbers and letters to classify different types of carbon steel stick electrodes. A typical classification can look like this: E7018-1 H4R.
- “E” indicates that the product is a stick electrode.
- “70” implies that the stick electrode will produce a weld with a minimum tensile strength of 70ksi.
- “1” indicates that the stick electrode can be used in all welding positions. If it was a “2” instead, this would mean that the electrode can only be used on the flat and horizontal welding positions.
- The next digit represents the coating type and welding current that can be used with the stick electrode. In this example, “8” refers to a low hydrogen coating and that the electrode has to be welded with either an AC or DCEP current.
- “-1” denotes that the stick electrode will offer additional impact values at lower temperatures.
- “H4” implies that there will be 4ml or less of diffusible hydrogen per 100g of weld metal.
- “R” indicates that the stick electrode has undergone specific tests and is deemed to be moisture resistant.
The Most Common E60XX Carbon Steel Stick Electrodes
E6010 electrodes are typically used by pipe welders to perform root pass welding on pipes. This electrode requires a DCEP welding current and offers a deep penetration with the ability to dig through oil, dirt, paint and rust. Similar to E6010 electrodes, E6011 electrodes tend to produce a deep and penetrating arc. However, E6011 can be used with both DCEP and AC welding current. E6012 electrodes, on the other hand, are general-purpose electrodes that produce a shallower penetration profile and a denser slag. Unlike E6012, E6013 electrodes produce a softer arc with minimum spatter and a slag that is easier to remove. As a result, E6013 is commonly used to weld clean, new sheet metal.
The Most Common E70XX Carbon Steel Stick Electrodes
E7014 stick electrodes produce a similar penetration profile as compared to E6012 electrodes. However, E7014 electrodes contain higher amounts of iron powder and can be welded at higher amperages. Another popular electrode is E7018, which is considered one of the easiest stick electrodes to use. It contains a high amount of iron powder and produces a smooth arc with minimal spatter. E7018 is commonly used to weld thick structural steel plates and can also deposit high strength welds with impressive impact toughness properties. Lastly, E7024 electrodes contain a high amount of iron powder and are used for high-speed welding in the horizontal or flat positions on steel plates that are at least ¼ inch thick.
Final Thoughts
If you need further assistance with stick electrode selection, please contact your trusted welding supplier to have an in-depth discussion.