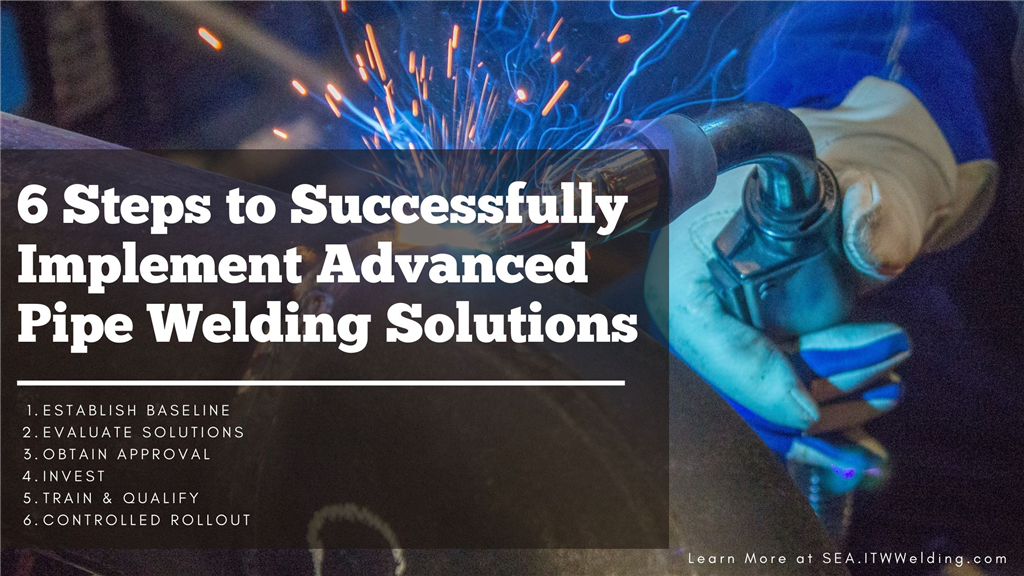
In today’s challenging environment, pipe fabricators around the world are constantly searching for solutions to improve throughput and reduce costs in order to stay ahead of their competition. Since welding makes up a large proportion of the pipe fabricator’s job scope, many fabricators have chosen to convert their traditional Stick and TIG welding processes to advanced pipe welding processes, such as Miller’s Regulated Metal Deposition (RMD®) and Pulse MIG. In doing so, these fabricators have been able to achieve higher productivity levels whilst maintaining the high quality standards demanded by their clients. In this article, we will share six key steps that pipe fabricators may adopt to successfully implement advanced pipe welding solutions in their organization.
1. Establish Baseline and Objectives
Before evaluating any new welding solutions, pipe fabricators should first establish productivity and quality baselines, such as existing dia-inch welded per day and current repair rates respectively. Subsequently, the pipe fabricator should do a deep dive into the whole operation to understand if welding is truly a bottleneck, or if welders are spending too much time waiting for parts to arrive or on non-value-added activities such as grinding, gouging and rework. If the welding operation is truly a bottleneck that is preventing the pipe fabricator from taking on bigger projects or completing existing projects on schedule, then it might be wise for the pipe fabricator to evaluate advanced pipe welding processes that can deliver higher efficiencies. Pipe fabricators can work with their trusted welding suppliers to perform an audit of their operations to understand if any improvements need to be made.
.jpg)
2. Evaluate the Advanced Pipe Welding Solution
The most direct and effective evaluation method will be to perform welding trials on a mock-up of the actual welding application to ensure that the technology actually works and to understand the possible productivity improvements that can be achieved. Fabricators should also ask the welding supplier to provide relevant references as well as welding procedures and third-party test reports to substantiate the advanced pipe welding solution. Having answered the question “Do advanced pipe welding processes work?”, the pipe fabricator is now ready to move on to the next pertinent question – “How to successfully implement advanced pipe welding solutions?”
3. Obtain Client’s Approval
As with any changes made to the existing welding processes, pipe fabricators will need to obtain their client’s approval before they can adopt the advanced pipe welding processes in the project. Besides on time project completion, most clients are concerned about two main issues: Quality and Implementation. Hence, it is important that before meeting with the client, the pipe fabricator must already qualify the welding procedure internally as per the project’s applicable codes, such as ASME B31.1. On top of that, the client will be interested to see a robust training and rollout plan that will ensure successful welder qualification and implementation. The pipe fabricator can work with a trusted welding supplier to develop a customized plan that can be presented to the client.
4. Make the Investment
After obtaining the client’s approval, the pipe fabricator will need to start investing in the advanced pipe welding solution. Depending on the project requirements, the pipe fabricator should work with a welding supplier that is able to provide different commercial options, such as purchase, lease-to-purchase, rental etc. Such options will give pipe fabricators greater flexibility and more control over their cash flow. In order to ensure that the advanced pipe welding solutions perform consistently, the pipe fabricator should also ask the welding supplier to conduct regular preventive maintenance and service training.
5. Qualify Welders
Before the pipe welders undergo the training and qualification test, the pipe fabricator should appoint an internal technical champion who will liaise between top management and the welding team, see the training program through, and quantify the productivity and quality gains during production. To ensure that the training program is a success, both the pipe fabricator and welding supplier need to commit to the previously agreed upon resources, such as trainers, time, base materials, welding consumables, expenses etc. It is important to work with a welding supplier who can provide experienced trainers to guide welders through the whole process quickly and efficiently.
6. Controlled Rollout
Lastly, once the welders are trained and qualified, it is important that the pipe fabricator starts with a controlled rollout. This entails having newly qualified welders work on specific pipes that are subject to visual and NDT inspections to ensure code-quality welds before they are allowed to proceed to weld more pipes in production. Such a controlled rollout also allows the internal technical champion to accurately document all productivity and quality improvements. Pipe fabricators may consider asking their welding supplier to station a trainer onsite to provide any assistance during this teething phase.
.jpg)
Move Forward With Confidence
The successful implementation of advanced pipe welding processes usually requires a strong partnership between the pipe fabricator and its trusted welding supplier. If you are ready to make improvements to your existing pipe welding operations, reach out to us at SGOffice@MillerWelds.com for a more in-depth discussion.