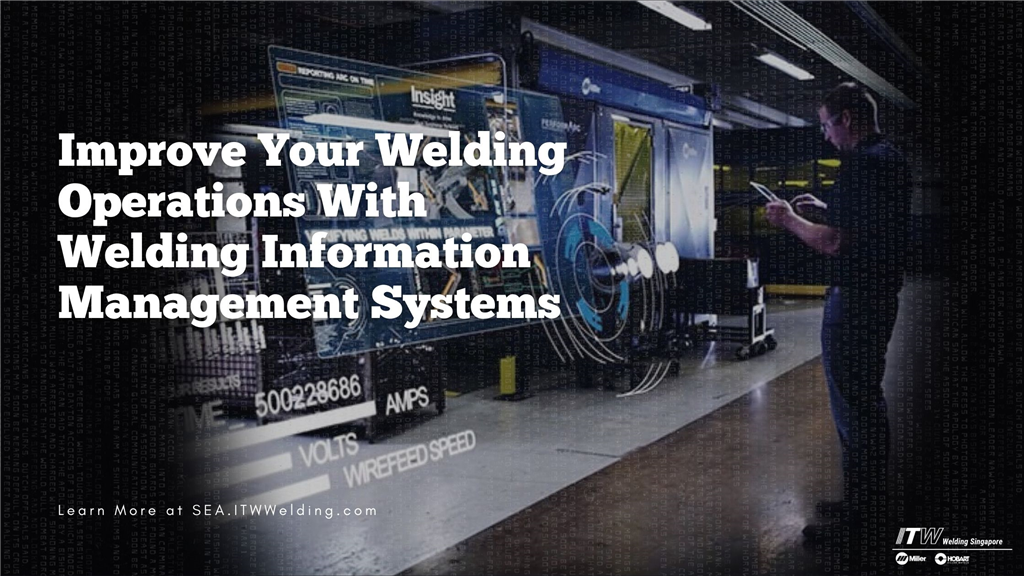
Manufacturers are constantly looking for ways to improve their welding operations. However, they tend to have more questions than solutions. Some of these questions include:
- Which welders are most productive?
- Which welders need more training?
- Are the newly hired welders meeting expectations?
- Are bad welds or missed welds escaping detection?
- What are the actual welding costs of the operation?
- What are the best ways to cut these welding costs?
- Once these ways have been identified, are the changes being made actually producing lasting results?
Miller® offers two welding information management systems to help manufacturers answer these questions, namely Insight Core™ and Insight Centerpoint™.
Insight Core™
Traditionally, the collection and analysis of the welding data is a manual process. As such, it is a challenge for manufacturers to accurately measure performance in their welding operations and to make the right improvements. Insight Core™ is a passive, real-time monitoring tool that provides visibility into the welding operations so that manufacturers can improve productivity.
With Insight Core™, manufacturers can measure each welder’s arc-on time and establish a productivity baseline. They can then make plans for improvements and evaluate the progress towards goals. All the welding data that is collected from the shopfloor is displayed in an easy-to-understand dashboard that allows manufacturers to generate reports, identify important trends, compare welders, cells and plants, and track long-term goals. Insight Core™ can also help manufacturers to identify the costs in their welding operations by tracking shielding gas and wire consumption, as well as labour. Manufacturers can leverage this information to make improvements and reduce costs. Lastly, the installation of Insight Core™ is simple and only requires an internet connection on the shopfloor to gather the welding data that can subsequently be viewed on any web-connected device by approved personnel.
.jpg)
Insight Centerpoint™
Undetected weld quality issues usually result in significant non-value-added costs to manufacturers. This cost escalates the further the weld defect gets away from the weld cell. For manufacturers who are constantly facing rework and missed welds in their operations, Insight Centerpoint™ may be the right solution as it can provide guidance, control and containment within the weld cell, thereby ensuring consistent weld quality.
With Insight Centerpoint™, welders can view and interact with a stationary screen display, which provides visualization of the part to guide the welders through the weld sequence in real-time. Manufacturers can gain addition control by embedding images, videos and audio files to provide clear, complete guidance throughout the entire welding operation. Insight Centerpoint™ is also able to alert welders if they miss a weld or if a weld is outside the prequalified parameters. As a result, this welding information management system allows manufacturers to monitor every single weld and provides early containment of defects, thus driving quality improvements and costs reduction throughout the welding operation.
.jpg)
Appoint a Champion
Besides spending time to evaluate and invest in a welding information management system, manufacturers also need to identify and appoint a champion in their organization if they want to achieve a positive return on investment. The champion should be responsible for creating a cross-function team that will implement the system, assess the collected weld data, recommend changes to be made in the welding operations, and execute those changes.
Gain New Insights
When the right welding information management system is implemented successfully, manufacturers can increase productivity while producing higher-quality welds and controlling costs. Reach out to us at SGOffice@MillerWelds.com for a free consultation and demo today!