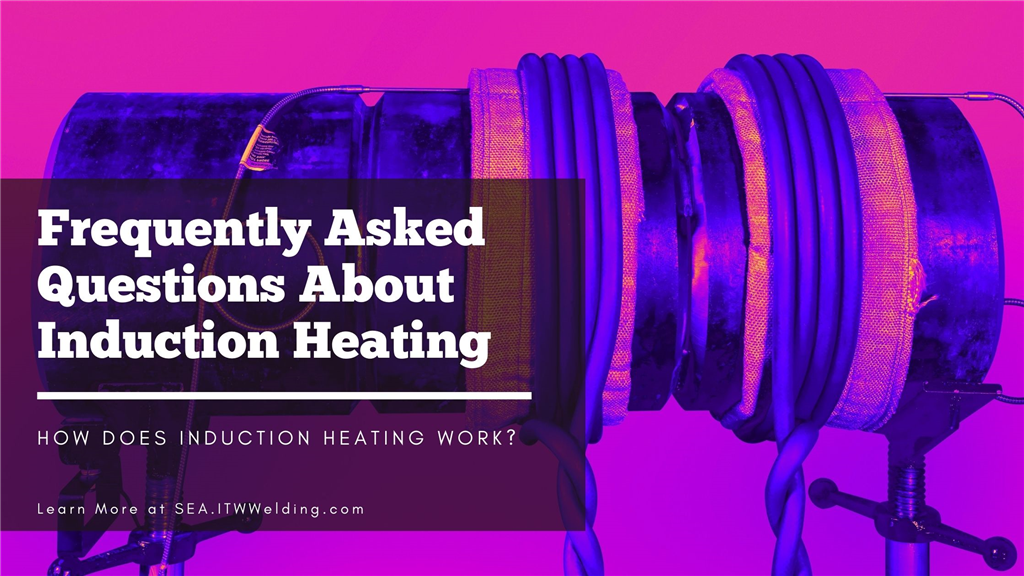
When compared to other conventional heating processes used for preheating and stress-relieving welds, induction heating is a simple, cost-effective heating process that delivers fast and consistent heat. Essentially the part becomes its own heating element, and the highest temperature is generated and controlled in the part, instead of by an external heating source such as the flame from a propane torch or the ceramic heating element from a resistance machine. In this article, we will answer four frequently asked questions about induction heating.
What Is the Science Behind Induction Heating?
Induction heating is based on the concept of electromagnetism. When electrical current flows through a copper conductor, it produces a magnetic field around the conductor. The direction of the magnetic field depends on the direction of the electrical current. By pointing your right thumb in the direction of the current and curling your fingers, you can determine the direction of the magnetic field. As more current flows through the conductor, the magnetic field around the conductor gets bigger and stronger. When the electrical current flow in the conductor is switched to the opposite direction, the direction of the magnetic field is also reversed. As the current alternates back and forth, the magnetic field grows and collapses simultaneously.
.jpg)
How Does Induction Heating Heat Metals?
When a piece of metal is placed in an alternating magnetic field, localized electrical currents (eddy currents) are generated within the metal. The bigger and stronger the magnetic field is, the more eddy currents are generated. The circulating eddy currents flow against the metal’s electrical resistance, which causes the metal to heat up. This process is called Joule heating and it’s what generates most of the heat with induction heating. Metals with low electrical resistance such as copper and aluminium require more eddy currents to heat as compared to metals with high electrical resistance such as carbon steel, which heat up more easily.
Another contributing factor to heating in ferromagnetic materials is hysteresis losses, which occurs due to the material’s resistance to a changing magnetic field. Hysteresis losses generate less heat than Joule heating, but still significantly contributes to the total heat within the material. Magnetic materials such as carbon steel generate more heat due to hysteresis losses, while non-magnetic parts such as copper and aluminium won’t generate any heat due to hysteresis losses.
.jpg)
How Do We Control the Strength of the Magnetic Field?
When we want to heat objects, we need a strong magnetic field to generate the eddy currents. The size and strength of the magnetic field can be increased by placing multiple conductors with electric currents flowing in the same direction next to each other. This is the reason why there are usually multiple coil turns on induction coils. However, do take note that when conductors are placed next to one another with currents flowing in opposite directions, the opposing magnetic fields will cancel each other out. As a result, no eddy currents will be generated in the material and heating will not take place. In general, we want to avoid this when setting up an induction coil.
Another factor that will impact the heating is how close the conductors are to the part being heated, also known as coupling distance. Since the strongest magnetic field is located near the conductor, the closer the conductors are to the part, the stronger the magnetic field will be, which in turn generates more heat. The further the conductors are from the part, the weaker the magnetic field and the lesser the heat generated.
What Are the Two Most Common Styles of Induction Coils?
Solenoid coils are made by wrapping the conductor around a cylindrical object such as a pipe or a vessel. The strength of the magnetic field depends on the number of turns we wind on the coil, how closely we place the turns next to each other, and how far the coil turns are placed from the part.
Pancake coils are made by winding the conductor flat in a spiral shape, and then placing them on one side of a surface such as a flat plate. Since the part is placed beside the coil, instead of inside of it, the magnetic fields are a bit weaker than the fields inside a solenoid coil. As such, we typically compensate for this by adding extra turns to increase the magnetic field. Once again, we can manipulate the strength of the magnetic field by how many turns we wind on the coil, how far we place the coil turns from the part, and by how closely we place the inner turns of the coil to each other. As mentioned previously, we need to remember that as the inner turns come close to one another, the magnetic fields will begin to collapse, and heating will not take place.
.jpg)
If you have more burning questions about induction heating, reach out to us at SGOffice@MillerWelds.com and we will respond to your questions!