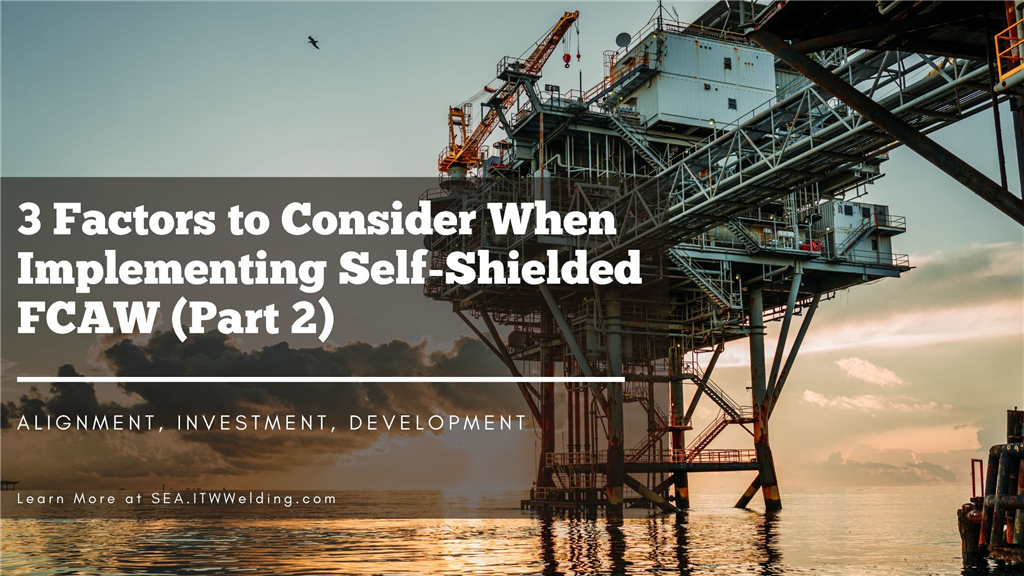
In Part 1 of this article, we discussed the limitations of Stick and Gas Shielded Flux Cored Arc Welding (FCAW-G) welding processes for the fabrication of jacket structures. Some fabricators have explored the use of Self-Shielded Flux Cored Arc Welding (FCAW-S) to replace these processes, and they have met with varying degrees of success. In this article, we will focus on three key factors that can affect the successful implementation of FCAW-S in offshore fabrication yards.
1. Alignment
As with most organizations, successful change-management takes place only when there is alignment amongst all the stakeholders. In this case, there must be alignment amongst the welding department, management, and client for the FCAW-S process to be successfully implemented. The management team can start by performing a thorough audit of the yard to understand if welding is truly a bottleneck, and if a change in the welding process can improve overall productivity levels so that projects can be completed on time and within budget. If a switch to the FCAW-S process is indeed the best option that the fabricator should adopt, the management team will need to garner the support of both the welding department and the client.
For the welding engineering team, the task of converting all existing welding procedures to FCAW-S procedures will be a challenge, even for the most experienced welding engineer. As such, the management team will need to incentivise and empower the engineering team to execute the changes. As for the welders, one of their main concerns with using a faster welding process is that they will not be able to claim overtime pay. Therefore, the management team must look to differentiate the salary of Stick welders and FCAW-S welders in order to drive change.
Lastly, some clients may be apprehensive about adopting a new welding process, even if the changes can help to improve the fabricator’s productivity levels to ensure that projects are completed within schedule. Clients are usually concern about weld quality issues that may arise with these changes. To address this concern, the management team will need to show the client the results of the internal tests that have been conducted, as well as a robust rollout plan to ensure smooth implementation of the new welding process.
2. Investment
Unlike the Stick welding process, FCAW-S requires a Constant Voltage (CV) welding machine with an accompanying wire feeder. For fabricators that only have CC welding machines in the yard, they will need to invest in new welding machines. When evaluating which welding machine to purchase, it is important that fabricators take note of these three factors.
1. For all-positional welding, the FCAW-S process typically operates on a lower voltage range, about 17 to 18 volts. The ability of the welding machine to maintain a stable voltage (at this low voltage range) is crucial to ensure good weld quality.
2. The welders are usually situated far away from the welding power source, so long welding cables are used, and it is not uncommon for large voltage drops to occur. As such, fabricators should consider a welding machine that is able to automatically compensate for such voltage drops and delivers the correct welding voltage that the welder sets at the weld joint.
3. Many fabricators tend to use generators in the yard to power the welding machines. This means that the welding machines may be subject to dirty input power, which may affect the stability of the welding arc. Therefore, fabricators should opt for welding machines that are designed to absorb such dirty input power and are still able to deliver a stable welding arc for high-quality welds.
As for the FCAW-S welding wire, fabricators should work with a welding manufacturer that has a long history of producing high-quality wires. Fabricators should also ask their welding supplier for references, approvals and relevant third-party test reports when evaluating the right wire for the job. Do take note that most FCAW-S wires in the market have a diffusible hydrogen content of less than 8 ml per 100g, however, some filler metal manufacturers are able to offer H5 tested controlled lots.
3. Development
With the right incentive structure in place and having evaluated and invested in the most suitable FCAW-S welding wire and welding equipment, the fabricator now needs to ensure the proper and sustainable development of its welding workforce. Since most welders may not have experience with FCAW-S, they will need to undergo training and requalification. The fabricator can start by identifying a few welders who have shown a strong interest in learning the FCAW-S process and who possess a strong aptitude to become a trainer. The fabricator should expect the welding supplier to propose a robust training program and commit experienced welding specialists to train these future trainers in the FCAW-S process. Once this train-the-trainer program is complete, the rest of the welders can proceed to be trained and requalified so that they can start using the FCAW-S process in production.
Make the Switch Today
For many offshore fabrication yards, having to requalify welding procedures and retrain a crew of welders is challenging and costly. Therefore, it is understandable that the Stick and FCAW-G welding processes are still dominant in the open assembly yard. However, the cost of maintaining the status quo and avoiding more productive welding solutions may impact the long-term profitability and sustainability of the fabricator. If you would like to have a more in-depth discussion, reach out to us at SGOffice@MillerWelds.com