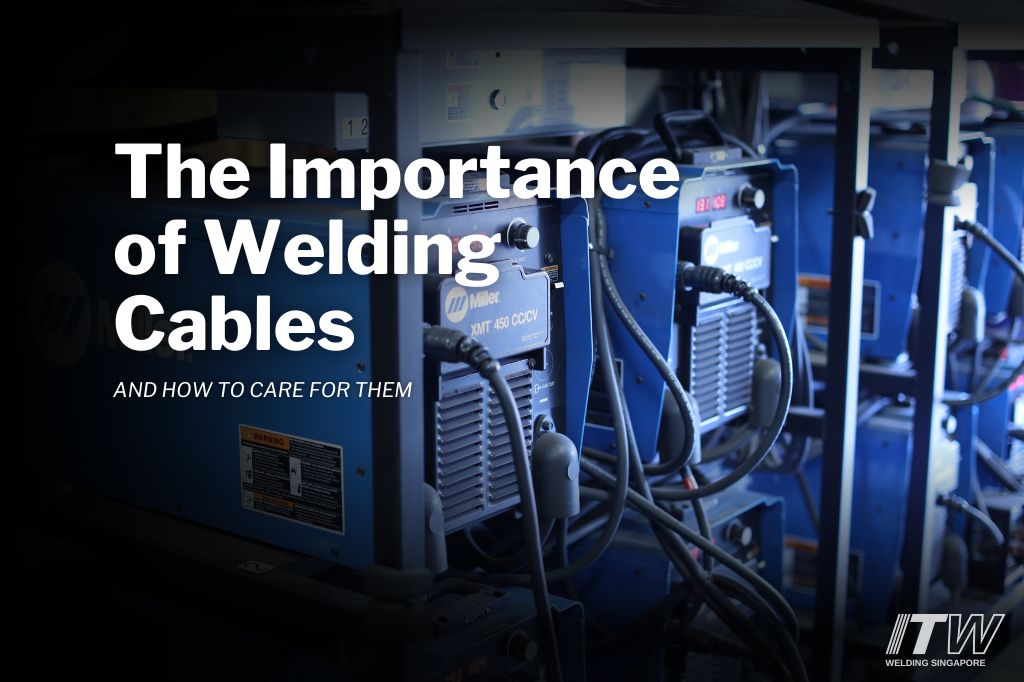
Did you know that welding cables are vital to the proper functioning of your welding machine? Neglecting them could lead to issues for your machine. Just like how preventative health care is important for yourself, it's essential to do some preventative maintenance on your welding equipment.
Why Is It Important to Care for Your Welding Cables?
Welding cables are a frequently overlooked and mistreated component of the welding process. Cables that are run over, excessively taped up, spliced, or undersized can cause the following issues:
- Overworking or over-duty-cycling of the welding machine, which can lead to unnecessary downtime and repairs.
- Increased electricity or fuel costs due to the overworked machine, which can eat into your bottom line.
- Poor weld characteristics that may cause additional rework, repairs, and downtime on the job.
How to Care for Your Welding Cables?
To ensure that your welding machine stays healthy, here are four simple tips to care for your welding cables:
- Keep the weld cables short. For example, it's crucial to avoid using a 30-meter length of cable for a 15-meter welding job. Instead, use quick connects if possible and save the extra cable for future needs.
- Do not coil the weld cables during welding. Coiling creates a large electromagnetic field around the cable hanger that can impact the welding machine's internal components and the arc quality over prolonged use.
- Inspect the weld cables, output studs, and connections every morning. Replace or repair any faulty cables or connections, tighten any loose connections, and clean dirty connections with a wire brush. It only takes a few minutes to inspect at the start of a shift and is preferable to losing a day's work to replace a burnt connection or purchase new cables that weren't checked.
- Use the appropriate weld cable size based on the distance of the weld circuit and the welding amperage. Undersized cables restrict the flow of current from the welding machine to the weld and create a resistor that generates heat in the cables or connection. For example, if the incorrect size is used, the machine will be over duty-cycled because a welder may try to run 32 volts at the output studs to compensate for those hot cables that are only giving 20 volts at the weld. Eventually, the welding machine may break down and cause unnecessary downtime.
To ensure that your welding machine lasts longer and works better, always use well-maintained and appropriately-sized weld cables. For further discussion, reach out to us at SGOffice@MillerWelds.com