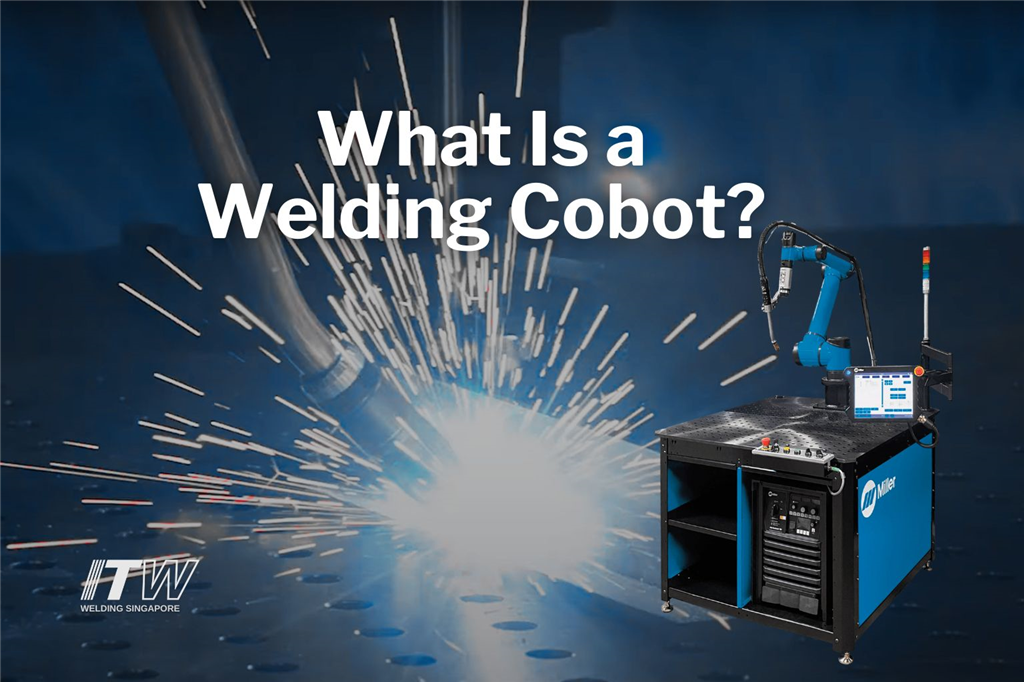
What is a Cobot?
Cobot is short for collaborative robot. Unlike traditional robots, cobots are generally smaller and lighter, have rounded edges, lower speeds, and limited force. As such, cobots are designed to work near humans without the need for fencing. Because of the reduced safety risks and portability, cobots can be easily moved within a facility to wherever it is needed. This gives companies more flexibility in their operations.
Additionally, most cobots come with an intuitive touch-screen user interface and are much easier to use compared to traditional robots. An operator with little programming experience can successfully learn to operate a cobot in less than a day of training. Since cobots can perform tasks with minimal programming, they are ideal for high-mix, low-volume work. These factors, including a lower upfront cost (compared to robots), are reasons why cobots are gaining popularity in the world today.
Many industries have adopted cobots for different applications such as pick and place, assembly, inspection, welding, and packaging. This versatility would not be possible without the availability of different end effectors, i.e., the device that is attached to the wrist of the cobot. Some examples of end effectors include grippers, sensors, screwdrivers, sanders, and welding guns.
What is a Welding Cobot?
A welding cobot is designed to carry out welding operations alongside a welder. For example, a welding cobot may be welding while a welder inspects and cleans a weld that was just completed by the cobot. This essentially turns one welder into two, boosting productivity. Moreover, the welding cobot never experiences fatigue, so it can deliver the same weld quality at the start of the shift and at the end of the shift.
Besides the cobot arm, there are three main components that make up a MIG welding cobot.
- The welding power source. The welding machine is responsible for producing the welding arc. Different welding power sources can deliver different welding outputs. For example, besides traditional CV MIG output, the Miller ® Auto-Continuum™ offers advanced MIG processes such as Accu-Pulse®, RMD® and High-Deposition MIG. When used in the right application, these advanced welding processes can help improve productivity and/or quality.
- The welding gun. The welding gun is the end effector attached to the wrist of the cobot. When selecting a cobot welding gun, such as the Tregaskiss® BA1, it is important to consider three factors. Firstly, the gun should be designed and engineered to last in high-volume welding operations. Secondly, to simplify maintenance, consider gun liners that can be replaced from the front of the gun. Lastly, choose high-quality gun consumables that have a longer lifespan to minimize downtime and maximize production uptime.
- The welding software. This is another crucial component that makes up the welding cobot, and a good welding software is designed with the welder’s needs in mind. A basic welding software is intuitive and will allow the welder to change welding processes/parameters at the teach pendant and create linear/circular welds with ease. More advanced features such as multipass welding, offset welding and weaving patterns are available in certain welding software. For example, the Miller® Copilot™ Cobot has a program called IntelliSet™. Welders only need to input the material thickness and wire diameter, and the software can provide accurate weld settings for the job.
When to Consider a Welding Cobot?
It might be wise to contact your trusted welding supplier to request a welding cobot demo if you face any of these challenges.
- Difficulty hiring or retaining skilled welders.
- Repetitive welds that are mundane.
- Inconsistent weld quality resulting in costly rework.
Reach out to us at SGOffice@MillerWelds.com to arrange a customized welding cobot demo.