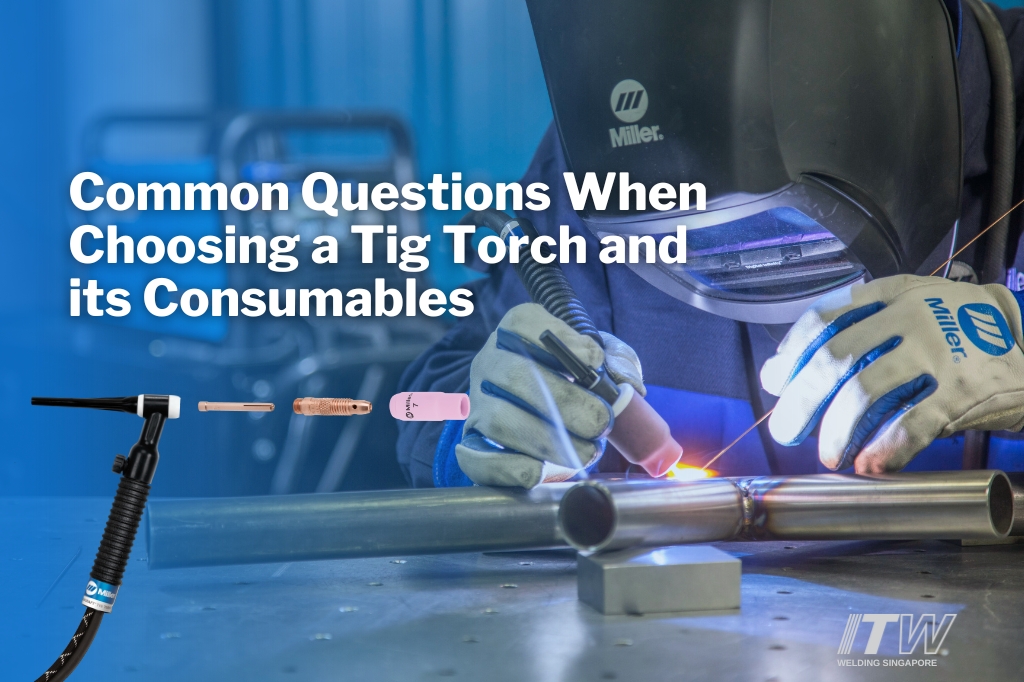
What are the most common TIG torches?
The 5 most common handheld TIG torches are WP-9, WP-17, WP-26, WP-20, and WP-18. The WP-9, WP-17 and WP-26 series are air-cooled TIG torches, while the WP-20 and WP-18 series are water-cooled. Here is a breakdown of their specifications.
- Weldcraft™ WP-9 is rated at 125A (DC) and 100A (AC) at 60% Duty Cycle.
- Weldcraft™ WP-17 is rated at 150A (DC) and 115A (AC) at 60% Duty Cycle.
- Weldcraft™ WP-26 is rated at 200A (DC) and 150A (AC) at 60% Duty Cycle.
- Weldcraft™ WP-20 is rated at 250A (DC) and 180A (AC) at 100% Duty Cycle.
- Weldcraft™ WP-18 is rated at 350A (DC) and 250A (AC) at 100% Duty Cycle.
What’s the difference between air-cooled and water-cooled TIG torches?
There are 3 main differences between air-cooled and water-cooled TIG torches.
- Air-cooled torches rely solely on shielding gas flow to cool components, while water-cooled torches utilize both shielding gas and a coolant.
- Air-cooled torches are generally suitable for amperage ranges up to 250A, making them ideal for lower amperage applications. Water-cooled torches can handle amperages up to 500A, catering to higher-demand applications.
- Air-cooled torches are typically rated at 60% duty cycle (i.e., 6 minutes welding, 4 minutes off), whereas water-cooled torches boast a 100% duty cycle.
What does WP-26FV-12-2 mean?
The naming convention for TIG torches has been established for many years now. Here is a breakdown of the nomenclature.
- “WP-26” is family of air-cooled TIG torches that is rated at 200A (DC) and 150A (AC) at 60% Duty Cycle.
- “F” stands for flexible neck. A welder can easily adjust the torch neck to any angle for better torch control in limited access joints.
- “V” refers to valve. The valve allows quick and easy adjustment of shielding gas flow.
- “12” denotes 12.5 feet power cable. If you prefer a longer power cable, there is a 25 feet option.
- “2” signifies a 2-piece cable, featuring separate power cable and gas hose. There is also a 1-piece cable option.
What’s the benefit of replacing the collet body with a gas lens?
A gas lens is composed of several screens. As compared to a collet body, a gas lens reduces shielding gas turbulence and provides a longer, undisturbed laminar flow of the gas to the weld puddle. If the weld is critical or requires high quality, a gas lens is the best option.
Which back cap to select?
Long back caps can utilize a full-length (usually 7”) tungsten electrode with minimal tungsten preparation. Small and medium back caps allow the torch to get into tighter spaces but require the tungsten to be cut. Tungsten should be cut using an abrasive cutoff wheel or ground with a grinding wheel. Avoid using wire cutters or bending, as this may create fractures at the cut ends, leading to erratic arcs.
What is the correct sequence when assembling the TIG torch?
When assembling a TIG torch, always tighten the collet body or gas lens before the back cap. Reversing this order can lead to the ingress of atmospheric gases that result in weld contamination.
What does the number on the nozzle mean?
The exit diameter for a TIG torch nozzle is specified with a number that represents the diameter in 1/16” increments. A number #8 nozzle has an inside diameter of 8/16” or 1/2”.
What size nozzle to use?
The purpose of the nozzle is to introduce the shielding gas to the weld puddle, and a long laminar flow is ideal to minimize the risk of weld contamination. There are 3 nozzle dimensions that affect the length of the laminar flow.
- Nozzle Diameter. A larger nozzle diameter will result in a longer laminar flow.
- Nozzle Length. A longer nozzle offers a longer laminar flow as the gas flow is more developed before exiting the nozzle.
- Nozzle Shape. A converging nozzle is recommended to achieve a long laminar flow.
How to properly grind a tungsten for welding?
While specialized tools exist for sharpening tungsten electrodes, a stone, belt, or disc grinder can also be effective. To prevent contamination, use a dedicated tungsten grinder and ensure that grinding scratches are parallel to the tungsten electrode centreline. Avoid angled or spiral scratches to maintain arc stability.
If you have more questions on TIG torches and its consumables, please reach out to us at SGOffice@MillerWelds.com