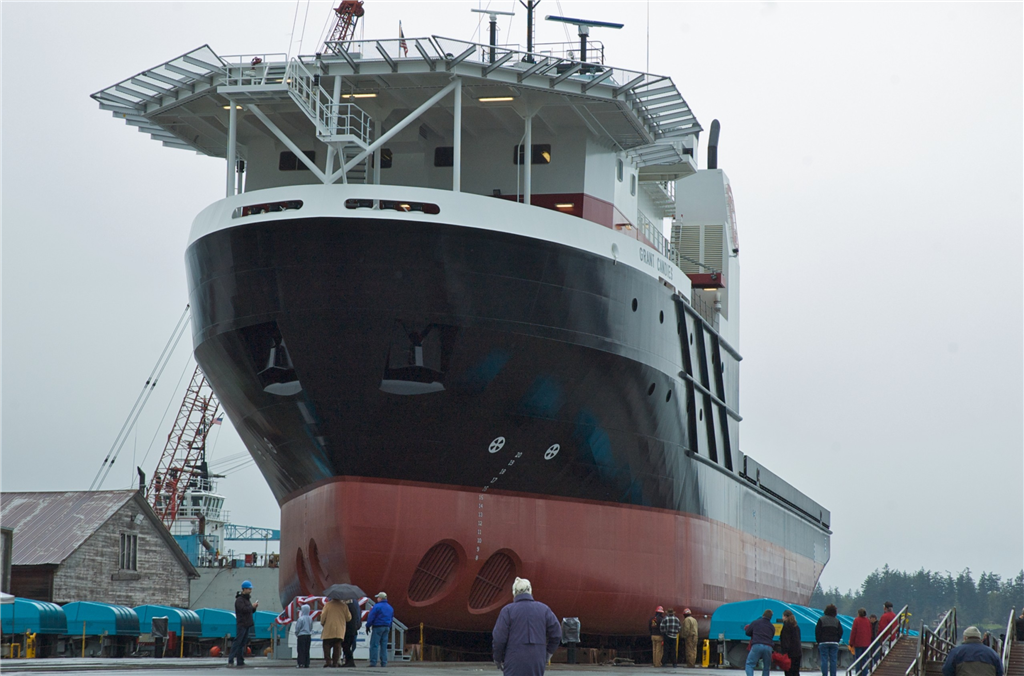
Primer-coated steels are prevalent in the shipbuilding industry because the material can withstand corrosion from saltwater. Most primer coatings are zinc-based and the use of it on steel eliminates the need for painting large portions of the steel after welding. However, this primer coating tends to cause issues such as porosity during the welding operations, which can lead to unnecessary rework and downtime.
In this article, we will discuss some of the techniques to minimize the problems associated with welding primer-coated steel, as well as address some of the safety precautious that should be in place when welding zinc-based primers.
Recommended Welding Techniques
Porosity is a common problem when welding primer-coated steel because the zinc content is unable to burn out of the weld puddle after the welding arc is established.
To overcome this challenge, one option that welders can employ is to remove the primer coating before welding. However, this is rarely done because it negatively affects the productivity of the welding operations and the steel will need to be repainted after the welding.
Another option is to perform tandem welding on both sides of the joint. This can be done manually by two welders or automatically using welding carriages or robots. Welding both sides of the joint helps to push the zinc impurities from the weld. Usually, it is recommended that the first welding arc is 3 to 4 inches ahead of the second welding arc so as to prevent zinc oxide gases from being entrapped in the weld pool and solidifying as porosities.
Because the zinc-rich primer makes the weld puddle sluggish, welders should typically use lower voltages, wire feed speeds and travel speeds as compared to welding non-coated steel. A 5% lower voltage will give a tighter arc that is capable of burning the zinc out of the weld pool more easily. Since a lower voltage is typically required, the wire feed speed and travel speed needs to be lowered as well to accommodate this change in voltage.
Lastly, a gun angle of 0 to 15 degrees should be employed when welding primer-coated steel. This will help create a tighter arc that will dig into the joint and weld through the primer.
Filler Metal Options
Some filler metals are specially formulated to weld primer-coated steel, and most of the time, these are flux-cored wires. There are scavengers in the flux that collect impurities such as zinc and these form part of the slag after each welding pass.
Traditional flux-cored wires with the AWS designators of T-1, T-9 or T-12 are commonly used for welding primer-coated steel in the shipbuilding industry. T-9 and T-12 wires are best for welding offshore structures that will encounter extremely cold temperatures. A flux-cored wire with a T-5 designator is another option that can be considered, but this wire tends to have poorer welder appeal.
Metal-cored wires can also be used to weld primer-coated steels, but they may not perform as well as flux-cored wires because metal-cored wires need to operate at higher voltages. As discussed previously, a higher voltage will not help remove the zinc from the weld puddle as well as when lower voltages are employed. In addition, metal-cored wires are typically limited to the flat and horizontal welding positions, unless paired with a welding equipment that can perform pulse welding.
Safety Considerations
The welding of primer-coated steels will expose the welders to hazardous fumes and gases such as carbon monoxide, zinc oxides etc. These gases are very harmful especially in confined areas or when air flow is poor. In order to create a safer working environment for welders, always ensure there is sufficient ventilation and consider using personal protective equipment such as a purified air powered respirator.