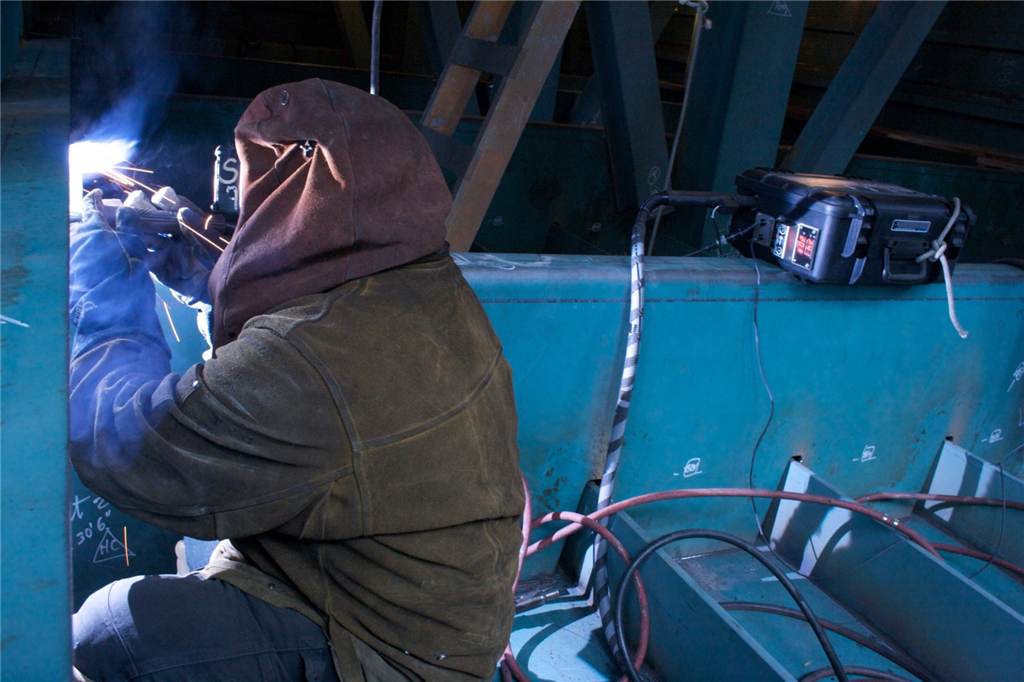
Poor wire feeding is a common challenge in many welding operations that can cause a lot of frustration and unnecessary downtime. It is very easy to assume that the filler metal is the main source of the problem, but in reality, wire feeding issues are usually a result of a combination of factors.
The Filler Metal
Established filler metal manufacturers design and produce welding wires with a lube coating to improve wire feeding and weldability. For filler metals that are commonly used in automated or mechanized welding applications, the manufacturer may also use different lubes to aid in better feeding through the longer gun liners. If the filler metal is kept within the manufacturer’s recommended storage conditions, there is usually no reason to use external products such as cleaning pads and lube pads that “clean” the wire and add more lube on the original product so as to “improve” the wire feeding.
The Use of Cleaning Pads and Lube Pads
Cleaning pads and lube pads are usually marketed to allow for the smooth feeding of wire that has a poor cast, an excessive helix, a rusty surface or when a long gun liner is used. However, you should be aware of some potential issues that can arise when using these products.
Adding extra lube to the wire can result in clogged liners, contact tips and gas diffusers. Excessive lube can also increase the risk of hydrogen-induced cracking since more hydrogen is introduced into the weld. Should the lube pad become too worn out, pieces of the pad could even make its way into the liner, further contributing to the wire feeding problem.
Because of these potential issues, many filler metal manufacturers do not recommend using these external products. The use of cleaning pads and lube pads adds an external variable outside of the manufacturer’s control that can negatively impact how the wire is designed to perform. If you are facing wire feeding issues, instead of implementing a cleaning pad and lube pad solution, it will be best to evaluate your welding set up and check all the potential factors that may be causing the poor wire feeding.
Troubleshooting Wire Feeding Issues
Wire Feeder or Equipment: If the drive rolls in the wire feeder do not move when the gun trigger is pulled, this could indicate a malfunction in the feeder relay, a broken control lead, or a loose connection in the external circuitry. Check and rectify these components to restart your welding operations.
Drive Rolls: Using the incorrect style or size of drive roll is another common source of poor wire feeding. Firstly, always match the drive roll size to the diameter of the wire. Next, choose the correct drive roll style depending on the type of wire used. V-shaped drive rolls are used for solid wire, and a V-knurled drive roll works better for cored wires. It is also important to set the proper drive roll tension. Too little tension will result in poor wire feeding while too much tension will crush the wire and result in a clogged gun liner. Also, check that the guide tubes are installed properly to ensure smooth wire feeding from the drive rolls into the gun.
Liner: Always ensure that the liner is of the correct length, size and style for the wire being used. Liners that are cut too short or too long can lead to a host of wire feeding issues. Use clean compressed air to blowout the debris that may have accumulated in the liner after a period of time.
Contact Tip: The contact tip will wear out over time due to the high temperatures and spatter from the welding operations. If the contact tip looks worn, it should be replaced before problems such as erratic welding arc and poor wire feeding start to occur.
Welding Gun: Sometimes, when the gun cable is too long, it can result in kinking and poor wire feeding. You should either choose the proper gun length for the welding application or keep the gun cable as straight as possible while welding.
Perform Root Cause Analysis
When you encounter poor wire feeding, don’t assume that cleaning pads and lube pads will solve the problem. There are multiple factors that can result in poor wire feeding and many of them have simple solutions, for example, blowing out a clogged gun liner or replacing a worn contact tip. When in doubt, you may consider contacting your trusted welding supplier to identify the root cause of the wire feeding problem.