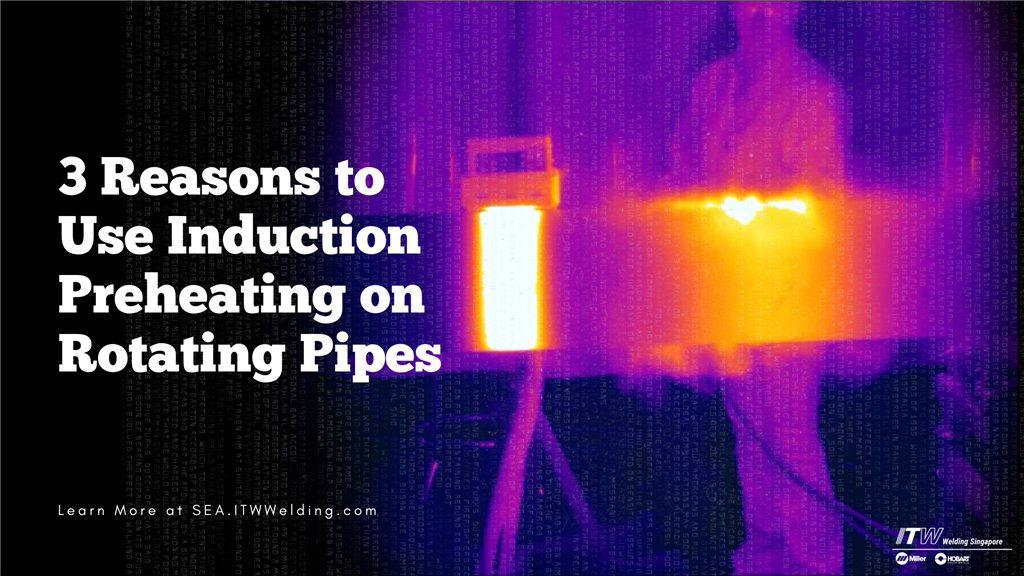
When it comes to preheating pipes and tubular structures that can be found in industries such as Oil & Gas, Offshore and Wind, the right method can save time and money, and reduce safety risks. In this article, we will compare 2 common methods that are used to preheat rotating pipes and tubular structures – Induction and Open Flame.
Induction Heating Delivers Higher Quality
Induction heating utilizes electromagnetic fields to generate eddy currents within the pipe, heating it internally from within. In rotating pipe applications, infrared sensors are used to allow for continuous monitoring and maintenance of the pipe’s temperature. As a result, induction heating can deliver thorough, uniform heat that is evenly controlled throughout the pipe. A digital recorder can also be employed to ensure accurate recording and reporting of the preheat temperature to clients and surveyors.
On the other hand, flame heating only heats the surface of the pipe, which then cools down when the flame is moved, resulting in multiple hot and cold spots. Temperature monitoring is also a manual process that is prone to errors or not done at all. In addition, the use of flame heating causes condensation in and around the weld, adding hydrogen to the pipe being heated. This hydrogen can build up and cause cold cracking in the finished weld.
Induction Heating Lowers Operating Costs
Induction heating is typically more than 85% power efficient because it heats the pipe from within and very little heat is lost to the surrounding air. As a result, the induction heating process can heat a pipe to temperature within minutes, and it is often much faster than other heating methods. Set up is also fast, simple and repeatable with the Miller® ProHeat™ 35 Rolling Induction System. These factors translate to more time spent welding instead of waiting on the production floor.
With flame heating, much of the heat is lost into the surrounding as it heats the pipe, resulting in a longer time-to-temperature. The time required for reheating with flame after breaks or shift changes adds to the overall time-to-temperature of the process since the pipe or tubular structure begin to cool immediately when the flame is removed. Lastly, because flame heating is such an inefficient process, it can consume a huge amount of fuel per station per shift, resulting in very high operating costs.
.png)
Induction Heating Improves Safety
The use of flame heating significantly increases the risk of burn injuries, fires and explosions. Welders may also inhale the toxic gas by-products that are produced during flame heating.
In contrast, induction heating is a much safer process because the heating tools do not get hot, and there are no toxic by-products or excessive noise from the process. This minimizes the safety risks for the welder and creates a much friendlier work environment.
Switch to Induction Heating Today
Preheat rotating pipes and tubular structures faster, cheaper and safer with the Miller® ProHeat™ 35 Rolling Induction System. Reach out to us at SGOffice@MillerWelds.com for a free consultation or demo.