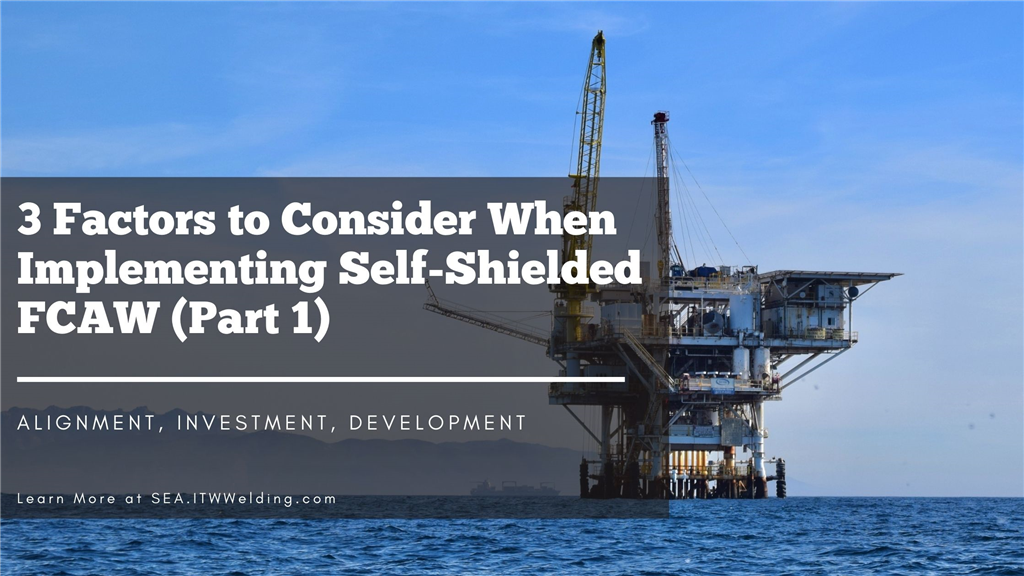
In Southeast Asia, there are many offshore fabrication yards that fabricate jacket structures. These jacket structures are submerged in water and serve as a foundation to topside structures such as offshore oil & gas platforms, living quarters, wind farm substations and wind turbines. A jacket structure is composed of multiple legs and braces that are made from high-strength tubular steel. These legs and braces are prefabricated and assembled in an open yard that is located near the load-out area. During the assembly process, there are generally two types of weld joints, circular joints and TKY-node joints. Circular joints arise when the ends of two steel tubes meet, while TKY-node joints occur when the end of a steel tube meets the surface of another steel tube.
Traditionally, most offshore fabricators in Indonesia, Malaysia and Vietnam are using either Stick welding or a combination of Stick welding and Gas Shielded Flux Cored Arc Welding (FCAW-G) processes to weld these joints in the open assembly yard.
Stick Welding
There are a few reasons why Stick welding is so predominant.
1. All welders are familiar with Stick welding as this is usually the first arc welding process that welders learn in training schools. This means that fabricators can easily recruit and qualify welders.
2. Stick welding is suited for outdoor welding and no external shielding gas is required. As a result, fabricators do not need to erect welding habitats in the yard or arrange for gas cylinders to be delivered onsite. This saves the fabricator both time and money.
3. The Stick welding process only requires a Constant Current (CC) welding machine and an electrode holder, which translates to a lower initial investment for most fabricators.
4. Most fabricators already have pre-existing Stick welding procedures that can be reused from project to project, and the welding process is also widely accepted by most clients.
Nonetheless, most fabricators would agree that Stick welding is a very slow process because of the low deposition rate and the constant need for welders to change out the welding electrode.
Stick Welding and Gas Shielded Flux Cored Arc Welding
In order to achieve higher welding deposition rates, some offshore fabricators have chosen to use a combination of Stick welding and Gas Shielded Flux Cored Arc Welding (FCAW-G) processes. However, with FCAW-G, it is very time-consuming to arrange for the gas cylinders to be delivered onsite. In addition, it is challenging to erect welding habitats in the open yard environment, especially when welding at height. Lastly, because the FCAW-G welding guns are equipped with a gas nozzle on the frontend, welders may find it difficult to access the complex TKY-node joints. This can result in welding defects such as lack of fusion, which could further reduce the overall productivity of the yard.
The Bottleneck
Because of the limitations associated with the Stick and FCAW-G welding processes, the welding operation is usually the bottleneck during the jacket assembly phase. In turn, the productivity levels of other tradesmen such as riggers, safety officers and scaffolders are also negatively affected.
In order to improve productivity and reduce the overall project costs to remain competitive, some fabricators have explored the use of Self-Shielded Flux Cored Arc Welding (FCAW-S) to replace the Stick and FCAW-G welding processes. These fabricators have met with varying degrees of success. In Part 2 of this article, we will focus on three key factors that can affect the successful implementation of FCAW-S in offshore fabrication yards.