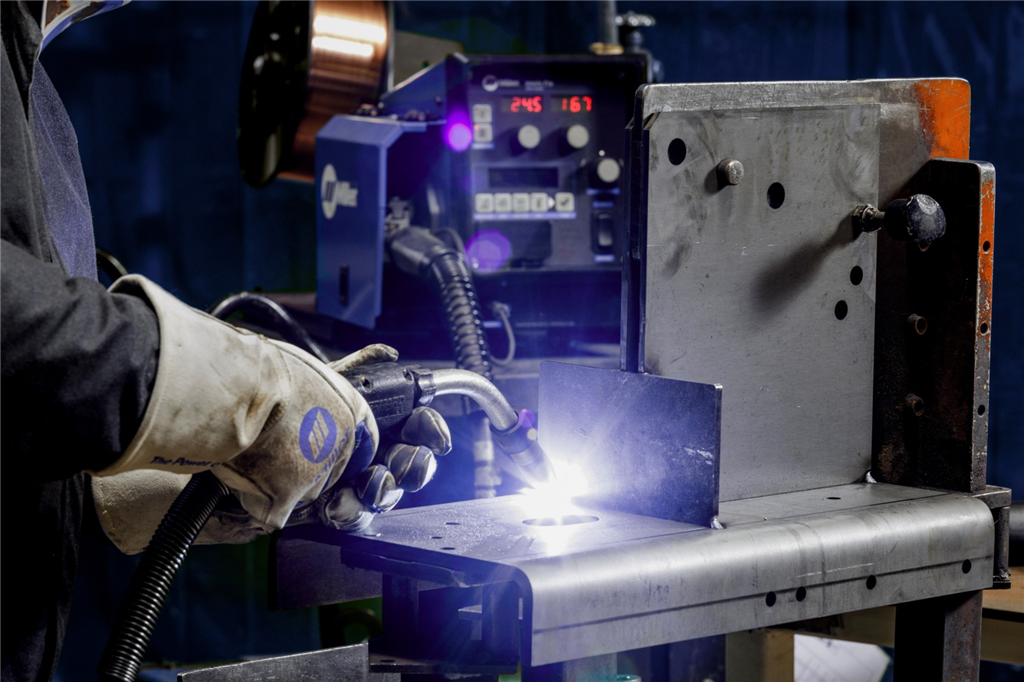
Achieving consistent quality in your welding operations depends on multiple factors such as the skill of the welder, the reliability of the welding equipment, the formulation of the filler metal etc.
There is another factor that directly impacts the performance of your welding operations but is often overlooked, and that is the shielding gas used. Shielding gases affect the mechanical properties of the weld, the amount of fume and spatter generated, and how smoothly the filler metal welds.
In this article, we will discuss the most commonly used shielding gases and how they impact weld performance.
The Basics
Helium, Argon and Carbon Dioxide are the most commonly used shielding gases. The main role of shielding gases in arc welding is to protect the weld puddle from elements such as nitrogen and hydrogen that are present in the environment. This helps to minimize potential weld defects such as porosity and cracking that will result in rework and unnecessary downtime. In addition, the shielding gas not only affects how the filler metal is transferred from the welding arc to the joint, but it also determines the weld penetration profile.
Carbon Dioxide and Argon
Carbon Dioxide (CO2) is a reactive gas and is the only shielding gas that can be used without the addition of an inert gas. It is also the most commonly used shielding gas because it is the least expensive. 100% CO2 is ideal for welding thick materials since the penetration profile tends to be broad and deep. However, 100% CO2 tends to create a slightly less stable arc and more spatter is generated, resulting in additional post-weld cleaning.
Argon (Ar) is an inert gas that is commonly used when welding aluminium, titanium and magnesium. 100% Ar provides a stable arc, consistent weld quality and appearance and good weld puddle control. It is ideal for welding fillet and butt welds since it produces a narrow penetration profile. Furthermore, minimal post-weld cleaning is required since 100% Ar generates less spatter.
In order to combine the benefits of using either 100% CO2 or 100% Ar, shielding gas mixtures consisting of 75-95% Ar and 25-5% CO2 are another option for welders. This Ar/CO2 gas mixture will allow welders to achieve higher productivity rates and create visually appealing welds when welding on materials such as carbon steel.
It is important to note that different compositions of Ar/CO2 gas mixtures will alter the mechanical properties of the weld metal. Shielding gas mixtures with higher Ar content will produce welds with higher tensile and yield strengths but with lower ductility and crack resistance. On the other hand, if a shielding gas mixture has a higher CO2 content, then the weld metal will have lower tensile and yield strengths but improved ductility and crack resistance.
Heat input is another factor that can affect the mechanical properties of the weld. High heat input has a similar effect on the mechanical properties of the weld as with a shielding gas made up of a higher CO2 content. Low heat inputs result in higher strength and lower ductility, similar to when the Ar content is high in a shielding gas mixture. Therefore, heat input and composition of shielding gas can be used to compound or offset the effect they have on the mechanical properties of the weld. For example, if an application demands for welding with high heat inputs that tend to result in lower weld strengths, then a higher Ar content in the shielding gas may be required to increase the strength of the weld.
Helium
Helium is another inert gas that is used as a shielding gas in arc welding. Helium is usually mixed with Ar in ratios of between 25-75% Helium and 75-25% Ar, and it is generally used for the welding of non-ferrous metals. Because Helium creates a hot arc and a wide and deep penetration profile, it can be used to help increase welding travel speeds and productivity rates. However, Helium is seldom used because it is more expensive compared to other gases. In addition, Helium is very light, so the gas flow rate tends to be higher than that of Argon. This higher gas consumption leads to greater operating costs. Helium can also be used in a tri-mix formula of Ar and CO2 for the welding of stainless steel.
As we’ve discussed, the choice of shielding gas will impact the performance of the weld, and it is crucial to choose the correct shielding gas to meet the needs of your welding operations. When in doubt, consult your trusted filler metal manufacturer on the type and amount of shielding gas that should be used for your specific application.