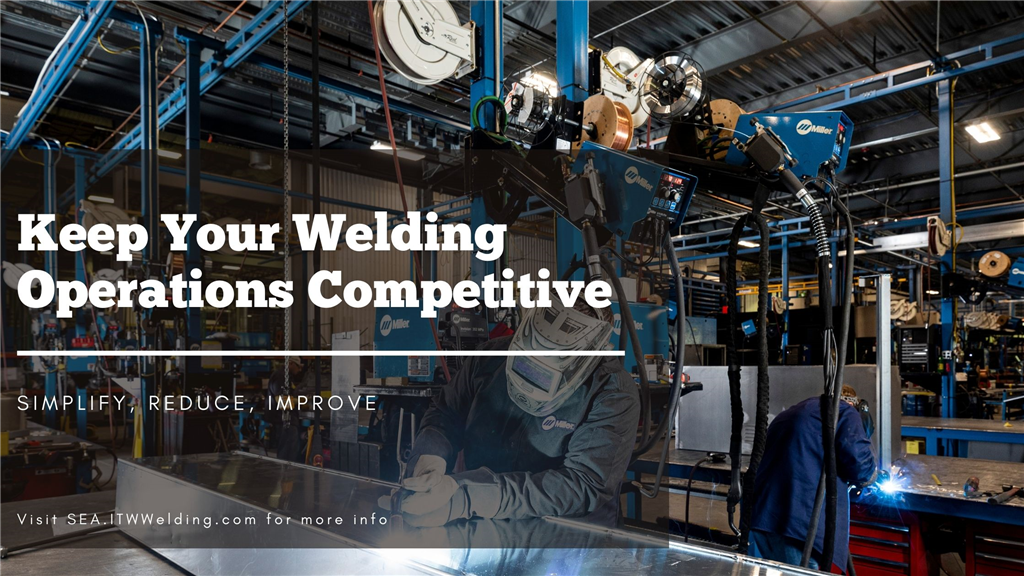
In today’s competitive landscape, clients are looking to award projects to metal fabricators who can complete projects in the shortest possible time and at the lowest bid price. In order to remain competitive, metal fabricators have to do a deep analysis of their welding operations to understand how they can simplify their welding operations, reduce total welding costs and improve productivity. It is worth noting that these factors are often interrelated. For example, eliminating non-value-added activities can help to simplify the welding operations, thereby improving overall productivity. In this article, we will discuss some of the ways that metal fabricators can improve their overall welding operations and remain competitive.
Simplify Welding Operations
To begin simplifying your welding operation, it is important to list down the sequence of your welding operation. As an example, we have put together a typical sequence below.
- Base material preparation such as blasting
- Joint preparation such as cutting and beveling
- Assembly of weld joint
- Tack welding
- Application of anti-spatter compound
- Preheating of base material
- Welding
- Grinding of spatter
- Slag removal
- Carbon arc gouging
- Replacing welding electrodes
- Welding process changeover
- Replacement of gas cylinders
- Repositioning of the welder around the weld joint
- Interpass cooling
- Polishing of weld bead
- Removal of anti-spatter compound
- Visual and/or NDT inspection of weld
- Repair of rejected weld and reinspection
- Post-weld heat treatment
Next, you need to identify the areas for improvement. One way to do that is to ask yourself this question “Is Step B a true value-added activity for Step C, or is Step B a non-value-added activity to compensate for the inefficiencies of Step A?” For example, is the time spent grinding spatter or repairing a rejected weld a value-added activity, or the result of a less than optimal welding process? If you are constantly compensating for the inefficiencies in your welding operations, not only does this add to your operating costs, it also negatively affects your productivity. By identifying and eliminating all non-value-added activities in the pre-weld, weld and post-weld operations, welders can spend their valuable time producing more high-quality welds.
Reduce Total Welding Costs
Many times, metal fabricators are fixated on comparing the upfront costs of various filler metal and welding machine brands, and many may choose to go with the cheaper alternative to save costs. However, in order to analyze and understand the true sources of welding costs, here are other factors that you may want to consider.
- Cost of shielding gas
- Cost of filler metal, taking into account the deposition efficiency
- Cost of electricity or fuel to operate the welding machine
- Base material costs related to reject rates
- Cost of grinding wheels, gouging electrodes and anti-spatter compound
- Cost of maintaining welding machine and accessories (spare parts, consumables etc.)
- Cost of unscheduled downtime due to frequent welding machine breakdown
- Cost of rework or non-valued-added activities
- Cost of over-welding
- Cost of disposal of filler metals and electronic components
- Cost of warehousing and logistics
For example, it is not uncommon for heavy-duty welding gun consumables (nozzles, contact tips) to have a higher upfront costs as compared to the standard consumables. However, the use of heavy-duty consumables in the correct applications can help to reduce your total operating costs in the long run because fewer replacements will be required during production, resulting in less downtime and welder frustration.
Another example would be the costs of over-welding. Did you know that if the leg length of a fillet weld should be 3/16 inch, but a welder over-welds and produces a 5/16 inch leg length instead, the amount of weld metal deposited would increase by 178%? If deposition efficiency is 100%, this would mean that the quantity of filler metal required for the job would increase by 178%. In addition, you will also need to factor in the amount of time the welder spent over-welding. All this adds on to your total welding costs.
Improve Productivity
With regards to improving welding productivity, many metal fabricators will think of implementing new welding solutions that increase the rate of deposition and/or travel speed. Usually, many of these solutions may be related to automation or robotic welding, which usually require a high investment costs. Here are some alternatives that you can consider.
- Invest in mechanized solutions such as tractors or carriages
- If the part to be welded can be rotated, invest in a simple positioner and allow the welder to weld in the downhand position
- Convert your manual TIG and Stick welding processes to semi-automatic wire welding processes
- Minimize the changeover time between different welding processes
- Eliminate all non-valued-added activities such as grinding, waiting and walking
- Identify sources of bottlenecks in the pre-weld, weld and post-weld operations and eliminate them
- Perform routine preventive maintenance to minimize any unplanned downtime
- Weld it once, weld it well
For example, Miller’s ArcReach Technology allows welders to make parameter and process changes at the point of welding, eliminating all unnecessary walking back to the welding machine. This is especially beneficial in expansive jobsites and when welders are working at height or in confined spaces, thereby improving jobsite productivity and safety.