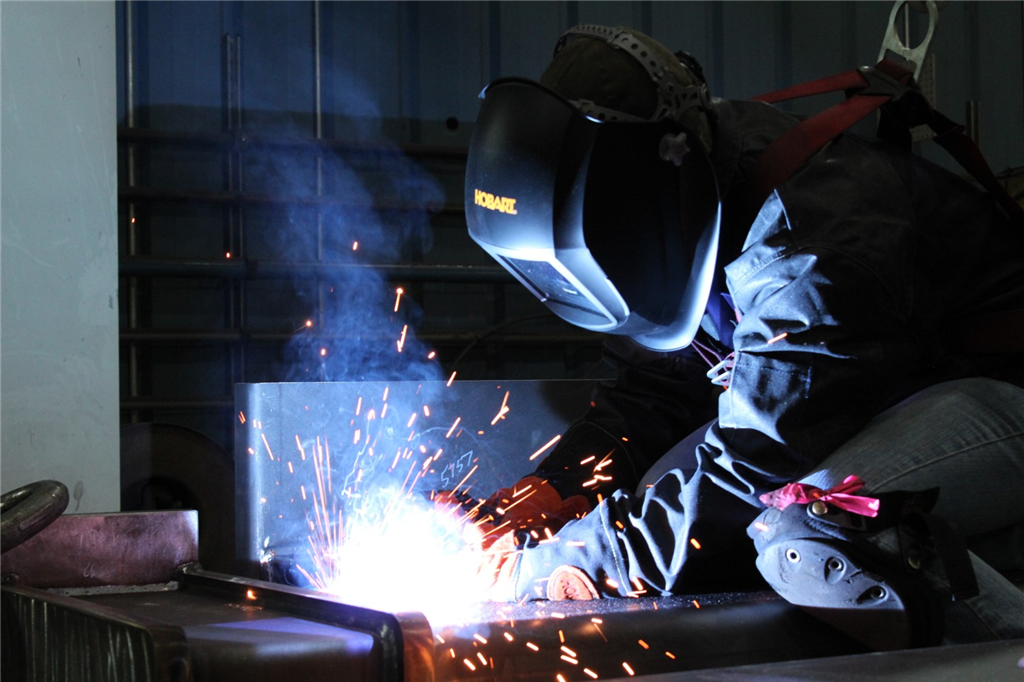
Metal-cored wires are more expensive as compared to solid wires. However, the benefits such as improved productivity and quality will help offset the higher per unit price if the metal-cored wires are implemented in the correct applications.
For companies considering the use of metal-cored wires, it is important to conduct a thorough assessment of the current welding operation, including the pre-weld and post-weld operations, to understand if the conversion is justifiable. The key will be to identify bottlenecks in productivity and the cost associated with these bottlenecks. This initiative will also help establish a good baseline for improvement so that companies can gauge the potential for productivity and cost improvements with metal-cored wires.
Review the Pre-Weld Activities
Are activities such as sandblasting, grinding or applying anti-spatter absolutely necessary, or are these activities compensating for the less-than-optimal welding wire being used? Are these activities resulting in a slowdown in the upstream portion of the welding operation? How much time and labour are spent on these pre-weld activities? You should also take into consideration the consumable costs associated with using grinders and sandblasting equipment, as well as issues related to operator fatigue or injuries when operating these tools.
Analyse the Post-Weld Activities
Quantify the costs and time associated with post-weld activities such as grinding and chipping of spatter. If there are weld defects that require rework, quantify the costs and time associated with the rework. If parts are rejected and need to be scrapped, calculate the material and labour costs associated with these rejected parts.
Scrutinize the Weld Cell
Observe the welding activity in the weld cell and take note of information such as number of parts welded per shift, arc-on time, welding parameters etc. These are important data that can be useful when calculating the potential impact of replacing the solid wire with a metal-cored wire.
Establish a Baseline for Improvement
Once all information from the pre-weld, weld and post-weld operations have been gathered and quantified, a baseline for improvement can be easily established. If the costs and time associated with the pre-weld and post-weld operations are higher than desired, or if there is a high volume of rework or if productivity is lower than expected, then metal-cored wire may be a viable alternative.
Determine the Payback
In order to justify the higher price point of metal-cored wires, you will need to show your management how this investment will offer payback through improvements in productivity and quality.
For example, in the pre-weld and post-weld operations, if the amount of time and money spent on non-value-added activities are high, you can show how metal-cored wires can eliminate the need for grinding, cleaning and part rework. In addition, labour can be more effectively utilized if they are reallocated to work on value-added activities such as welding, so as to produce a higher volume of parts. In the weld cell, metal-cored wires may offer the possibility of completing the welding process faster, thereby improving the overall productivity of the welding operation.
When determining if the metal-cored wire is the best choice for your welding operations, never rush the assessment or decision. When you are performing trials with metal-cored wires, always do so in a limited capacity so as not to disrupt your existing production schedule. Reach out to your trusted welding supplier to help you with the evaluation process and guide you through the conversion to increase your chances of success.