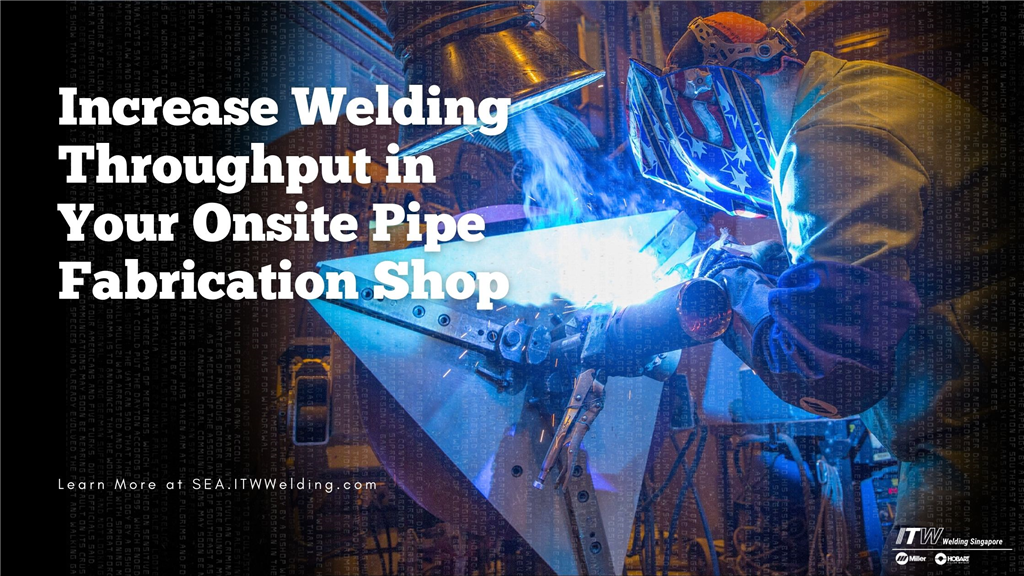
For permanent prefabrication pipe shops that want to improve productivity and take on more projects, many have switched from the manual Stick and TIG processes to fully mechanized systems that usually consists of a column and boom manipulator, positioner, and interface controller. In order to achieve the higher deposition rates that these fully mechanized systems are meant to deliver, advanced pipe welding processes such as Miller’s Regulated Metal Deposition (RMD®) and Pulse MIG are typically employed. Despite these fully mechanized systems having a high initial investment costs, many pipe shops are able to achieve ROI within a few years because of the significant increase in throughput that these systems offer. For example, an 8-inch Schedule 80 pipe takes about 3-hours, on average, to complete with the manual Stick and TIG processes. On the other hand, the same pipe can be welded in 30-minutes with a fully mechanized system, a 500% increase in throughput.
That being said, for temporary pipe shops that are set up near the construction site, the implementation of a fully mechanized system might not be practical or make any financial sense since these shops tend to exist only for a short period of time. As such, piping contractors typically still prefer to employ the manual Stick and TIG processes to get the job done. However, these welding processes are slow and labor intensive, and could result in the welding operation becoming the bottleneck of the entire production.
In order to achieve a higher throughput without having to make a large initial investment, temporary pipe shops can consider a handheld mechanized setup instead. This setup consists of a pipe positioner or pipe stand that rotates the pipe in the horizontal position, and a welder welding the RMD® and Pulse MIG processes in the down hand position (1G). Given that this setup has a much smaller footprint and weight compared to a fully mechanized system, it can be easily transported from one project site to the next. In addition, the piping contractor can also achieve a significant increase in productivity. Using the same example as mentioned above, the 8-inch Schedule 80 pipe can be welded in 45-minutes with the handheld mechanized setup, translating to a 300% increase in throughput.
.jpg)
Besides delivering a higher throughput, the handheld mechanized setup offers two additional benefits over the manual Stick and TIG processes. Firstly, welders are able to deliver higher quality welds consistently because they are welding in the 1G position throughout the shift, as compared to the manual Stick and TIG processes which require the welders to weld in a 5G position that increases welder fatigue. Secondly, piping contractors will find that it is easier to recruit and train new welders with the handheld mechanized setup, as compared to the manual Stick and TIG processes, which tend to require a lot of training in order to deliver code-quality welds.
If you want to have a further discussion on handheld mechanized pipe welding, or see a demo, kindly reach out to us at SGOffice@MillerWelds.com