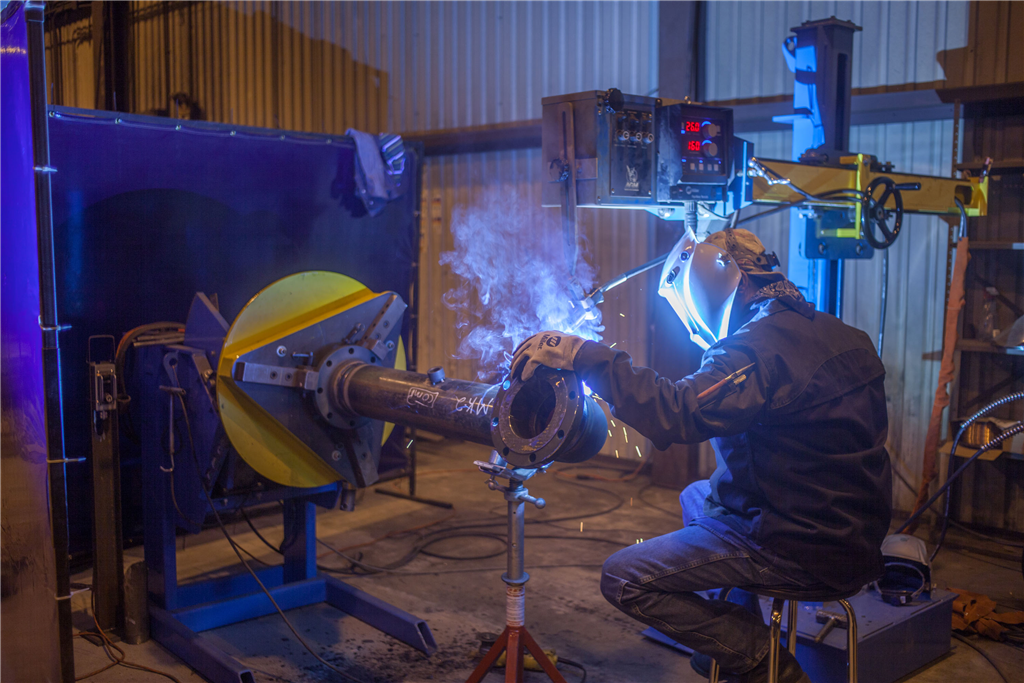
USA Energy Fabrication
USA Energy Fabrication focuses on process piping that are used in petrochemical plants, pharmaceutical plants and refineries. The typical base materials to be welded consists of Schedule 40 and Schedule 80 carbon steel pipes and Schedule 10 stainless steel.
A change in process led to significant productivity gains
In the past, USA Energy Fabrication would weld all the pipes manually. The process was time-consuming and made it difficult for the business to scale and capture more projects. In order to meet increasing customer demands, USA Energy Fabrication decided to try out the Miller PipeWorx 400, coupled with a mechanised pipe welding system. This combination allowed the pipe shop to convert from a manual welding process to a semi-automatic process that was able to greatly increase productivity and deliver consistently high-quality welds.
The Miller PipeWorx 400 offers multiprocess welding capabilities such as RMD, Pulse, FCAW etc. RMD is a modified short-circuit MIG process that is specially designed for root pass welding on pipes. The RMD process precisely controls metal transfer for uniform droplet deposition, providing a stable arc and easy puddle control. On the other hand, the mechanized pipe welding system consists of a positioner and oscillator that controls the welding gun and the puddle. The welder uses a remote to start the weld, observes the weld puddle and makes any necessary parameter adjustments on the remote.
With that first combined system, a welder could complete as much work as three manual welders in one shift, resulting in huge productivity gains that made it much easier for USA Energy Fabrication to keep up with their workload at the time. For example, in a time study that was conducted by USA Energy Fabrication, they observed that a welder took 19 minutes to complete a 6-inch double extra heavy wall pipe with the mechanised pipe welding system. A manual welder would have taken two hours to complete the same pipe. Due to the tremendous productivity gains, the company eventually added two more mechanised pipe welding systems in their pipe shop.
Achieving consistently high-quality welds
Because USA Energy Fabrication produces pipes for the oil and gas industry, the pipes produced must pass x-ray tests and meet the ASME B31.3 process piping code. Failure to pass x-ray tests is very costly for the company and could potentially affect their reputation in the industry. Before implementing the mechanised pipe welding system, USA Energy Fabrication typically had an x-ray passing rate of 80% to 95%. Now it’s over 99%. This improvement is largely attributed to the fact that welder fatigue has been reduced significantly with the mechanised welding system. The welds produced look exactly alike at 8AM in the morning and 5PM in the evening.
In addition, the Miller PipeWorx 400 has a simple operating interface and in-built welding processes that are optimized for pipe welding. The RMD process is also more forgiving to changes in wire stick-out and improper part fit-up. These factors allow for easier and faster training of inexperienced welders.
Primed for expansion
Without the three mechanized pipe welding system, USA Energy Fabrication does not believe they would have been able to expand, to reach out to more customer and to take on larger jobs. With the Miller PipeWorx 400, the pipe shop can complete more welds in a day while keeping customers happy with the consistent quality. USA Energy Fabrication is looking to expand their business even more, and they expect Miller equipment will continue to be an important part of that growth.