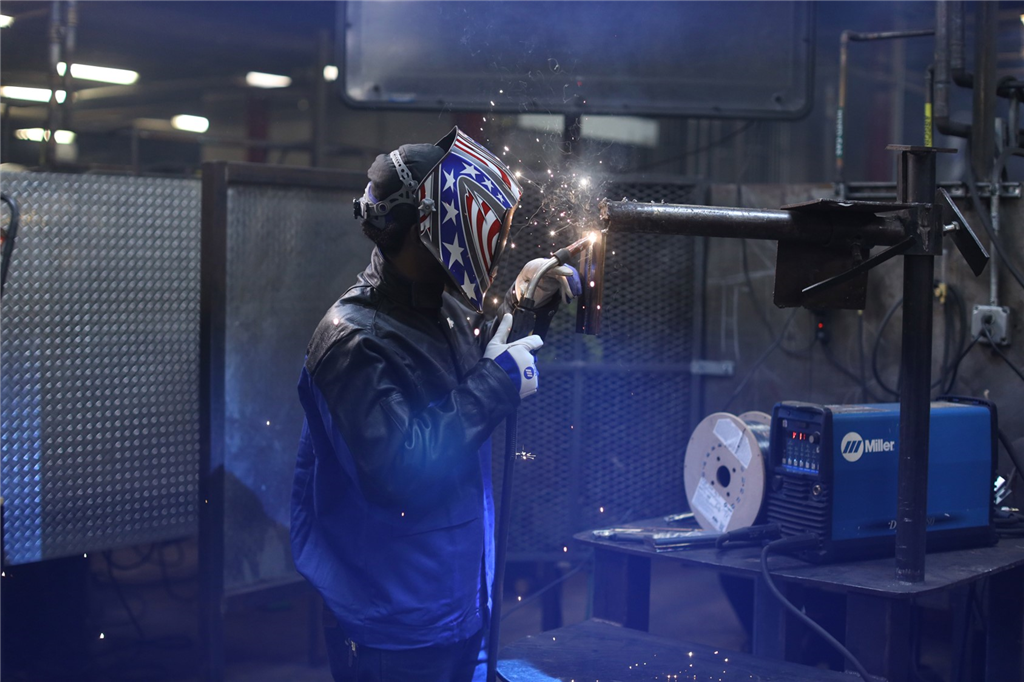
Performing preventive maintenance in your welding operations is crucial to keeping production flowing smoothly and avoiding any unplanned downtime. In this article, we will share some maintenance best practices so you can get the most of your MIG gun and help prevent issues such as poor wire feeding that can result in unnecessary downtime.
Perform Proper Inspection
Before welding, always start with an inspection of the gun and work your way back to the wire feeder. Ensure that the consumables at the front-end of the neck are tightened and the back-end of the neck is secured to the gun handle. If these connections are loose, there will be poor electrical conductivity which could lead to weld defects and overheating of the gun. Visually inspect the gun handle and trigger to check that there are no damages or missing screws. The welding cable should be free of cuts and kinks, and there shouldn’t be any exposed internal copper wiring. Exposed wirings are not only a safety hazard for the welder but can also lead to a build up of electrical resistance and eventual overheating of the cables. Lastly, verify that the power pin of the gun is fully inserted and tightly fastened to the wire feeder. If the connection is loose, issues such as birdnesting and overheating of the gun can occur.
Gun Liner
Because the gun liner is one of the most difficult components of the gun to inspect and maintain, it is one of the most common sources of poor wire feeding and unscheduled downtime. Always follow the manufacturer’s instructions for proper trimming and installation of the liner. A liner that is cut too short will cause wire feeding problems. During installation, always keep the liner off the ground to avoid picking up dirt and debris that can result in weld porosities. After welding for a period of time, it is normal that fragments of welding wire will chip off and build up in the liner. You can clean out the dirt and debris by periodically blowing clean compressed air through the liner. This periodic maintenance will help prevent issues such as poor wire feeding, burnback and birdnesting.
Gun Consumables
Front-end gun consumables such as gas diffusers, nozzles and contact tips are constantly exposed to heat and spatter. Therefore, it is important to perform preventive maintenance to help extend the life of these consumables and to improve the gun performance. Ensure the gas diffuser is fastened tightly to the neck and check the diffuser’s O-rings for cracks, cuts or damage. Use pliers to clean the spatter that builds up on the nozzle over time to allow for unobstructed gas flow. As for contact tips, look at the diameter of the tip and observe for signs of keyholing. If the contact tip looks worn, it should be replaced before problems such as erratic welding arc and poor wire feeding start to occur.
Take Care of Your Equipment
When MIG guns are not in use, store them in a coiled position in a safe place. Do not leave them lying on the floor where there is a chance the gun could be run over and damaged. The better you take care of your welding equipment, the better results you will achieve in your welding operations.