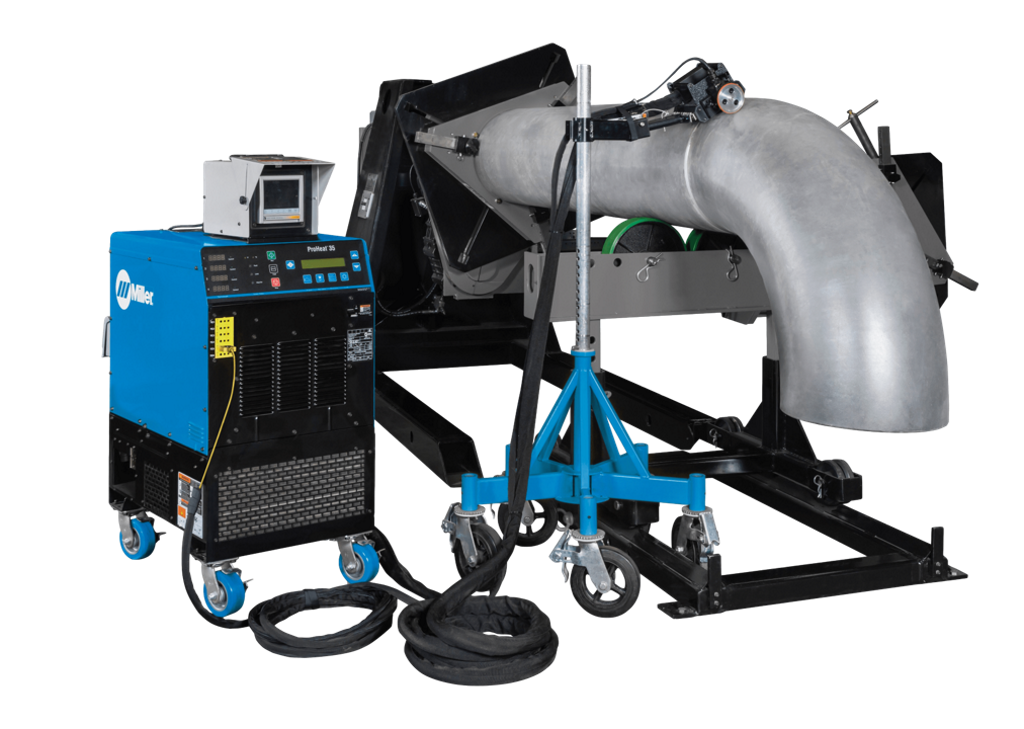
Preheating is usually done before the welding of steel or steel alloy pipes that are 1 inch thick or more. This helps to reduce the cooling rate of the weld and also drives out moisture, thereby ensuring high-quality welds and a reduced potential for cracking.
There are various methods for preheating, such as open flame, resistance heating, and traditional induction heating, each with its advantages and disadvantages. However, when it comes to rolled pipe welding applications, there are very limited options in the market that can allow for successful preheating and temperature control. In this article, we will look at a new technology, rolling induction heating, that is specifically designed for the rotating pipe/tubular welding applications. We will also address some of the concerns associated with other popular heating methods such as open flame and resistance heating.
Comparing the Various Preheating Methods
Many fabrication shops use an open flame torch because it is the simplest method for either rolled pipe or stationary pipe welding applications. The setup is quick and easy, welders are familiar with the equipment, and the initial investment costs are low. However, preheating with an open flame is very inefficient because a lot of the heat is lost into the surrounding. The consumable costs are high because of the high consumption of LPG cylinders. There are also safety hazards to consider such as the higher risks of burns, the storage of explosive gases and the consistent exposure to carbon monoxide fumes. Quality could also be another issue, since flame heating usually results in inconsistent heating with multiple hot and cold spots.
Other fabrication shops may also rely on resistance heating for preheating of pipes. With this method, ceramic heating pads and insulation are wrapped around the part to be heated, and the setup and teardown time is usually very time-consuming. These consumables are also fragile and need to be replaced occasionally since broken pads can result in hot and cold spots in the part. In addition, the number of cables and wires required for resistance heating make this method less suitable for rotating pipe application.
Similarly, traditional induction heating solutions also required a heating cable to be wrapped around the pipe, making It less ideal for rolled pipe welding applications. However, with the new rolling induction technology, an inductor sits on the pipe and does not interfere with the rotation of the pipe. The inductor is connected to a Miller ProHeat 35 machine, from which the inductor gets its power. An alternating current is passed through the inductor, creating a magnetic field around it. This magnetic field passes through the metal pipe, creating eddy currents within the material. The resistance of the metal against the flow of the eddy currents results in heat being generated in the pipe. As such, the pipe becomes its own heating element, heating from within. Therefore, this makes induction heating a very efficient process as compared to open flame and resistance heating because minimal heat is lost to the environment.
Higher Productivity and Ease of Use
Miller’s exclusive rolling induction technology is designed for an easy setup. The rolling inductor mounts on a standard pipe stand, and the welder needs to align the inductor on the rotating pipe. The welder only needs to set the maximum output and time on the Miller ProHeat 35 machine, and the equipment does the rest. Induction heating will bring the part to the desired temperature quickly and uniformly, making it an efficient heating method for rolled pipe applications.
Contributing to a Safer Work Environment
Compared to flame and resistance heating, induction heating will reduce the burn potential since there are no heating elements involved. Induction heating can also contribute to a more comfortable working environment and reduce welder fatigue because there is minimal heat loss to the surrounding, and no toxic fumes and smoke are generated.
Since induction heating is a safer method of heating, this can contribute to the fabrication shop’s goal of achieving zero lost-time incidents. Improvements in safety can also reduce the cost associated with worker downtime, insurance and compensation payments, thereby improving the fabrication shop’s bottom line.
Consistent Heating Quality
Maintaining a consistent temperature throughout the pipe is especially critical, particularly when welding today’s high strength steels. With the rolling induction technology, there will be minimal hot and cold spots on the pipe because the machine provides a steady heat output as the pipe rotates. The system offers a maximum temperature of 315 degrees Centigrade and can be used on pipe diameters 8 inch and greater.
Lower Lifetime Costs
The initial investment costs for the rolling inductor is higher compared to flame heating and resistance heating. However, the rolling inductor is a more efficient technology and is less expensive to operate on a per-hour basis. It can also increase productivity since it brings a pipe up to the desired temperature faster, and it contributes significantly to improving the safety of the fabrication shop. Therefore, the return on investment grows in favour over the lifetime of the equipment.
The Miller ProHeat 35 power source is also compatible with other accessories and tools, besides the rolling inductor. For example, when liquid-cooled cables are attached to the power source, the machine can perform multiple functions including hydrogen bake out, shrink fitting and post-weld heat treatment. This increases the versatility and value of the investment.
Make an Informed Decision
Preheating is a vital part of the pipe fabrication process to ensure high-quality welds. When deciding on which preheating method to use, it is important to consider the productivity, safety, quality and environmental issues associated with the various preheating methods.