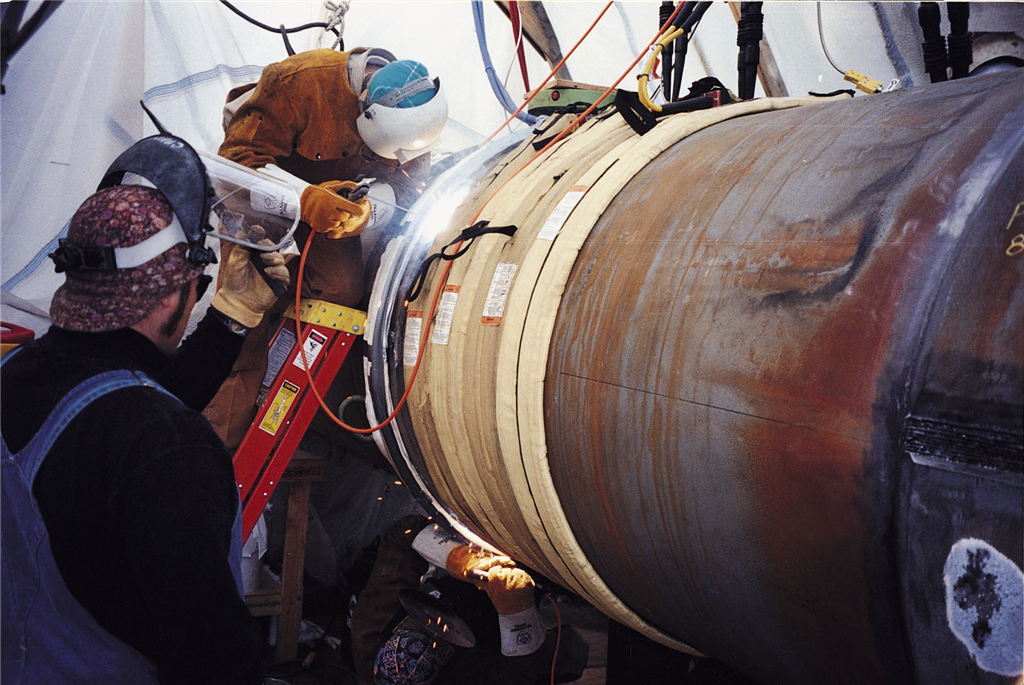
Preheating is usually required before the welding of new transmission pipelines and the repair and maintenance of existing in-service transmission lines. Preheating helps to ensure that the weld joint achieves its required strength and hardness and helps to minimize the risk of delayed hydrogen-induced cracking.
There are several preheating methods available for pipeline welding. Open flame is one common method, but it presents some challenges that can negatively impact weld quality and integrity. Another option is induction heating, a method that offers various benefits for weld quality, efficiency and safety.
Induction Heating on New-Build Transmission Pipelines
One of the main quality challenges associated with using an open flame to preheat pipes in the field is that the process increases the risk of hydrogen-induced cracking. When a fuel is burnt, as with flame heating, water vapour is produced as a by-product. The moisture in water vapour can be a source of hydrogen in the weld that be detrimental to the integrity of the pipeline. If high-quality welds are to be achieved in pipeline applications, it is important to reduce the risk of trapping hydrogen in the weld.
In addition, flame heating usually results in inconsistent heating throughout the pipe since it is a manual process. It is also harder for the welder to maintain a specific temperature or ensure that the temperature remains within what is specified in the welding procedure. Going above or falling below the required temperature window will adversely affect the quality of the weld. Flame heating also doesn’t provide good traceability since the temperatures are monitored manually using temperature crayons.
Induction heating may be a newer method to preheat pipe, compared to flame heating, but it has already been successfully implemented in transmission pipelines for many years. Induction heating cables of various configurations and sizes are wrapped around the pipe to be heated. An alternating current passes through the heating cables and creates a magnetic field around it. The magnetic field induces localized eddy currents within the pipe. The resistance of the metal against the flow of these eddy currents result in heat being generated in the pipe. The pipe becomes its own heating element, making the induction heating process highly efficient with minimal heat loss to the surrounding. Because of this higher efficiency, induction heating provides a much faster time-to-temperature. Speed is critical in the construction of new transmission pipelines because the contractors want to weld as many joints as possible per day.
Besides the productivity benefits, induction heating can also improve weld quality. Since no fuel is burnt with the induction heating process, moisture is kept out of the welding process. This significantly reduces the risk of hydrogen-induced cracking and helps to ensure the integrity of the pipeline. Induction heating also provides consistent and uniform heating throughout the part because the system uses feedback from thermocouple probes for automatic temperature control. Welders can now easily maintain the required preheat temperature and ensure that the pipe remains within the acceptable temperature window throughout the welding process.
Preheating of In-Service Transmission Pipelines
For the repair or maintenance of in-service transmission pipelines, it is usually not practical or feasible for the pipeline to be shutdown just so that welding works can take place.
With traditional flame heating, it is very difficult to preheat the pipe properly because heat is being pulled away from the steel via the fluids that are flowing in the pipe. This is known as the heat sink effect. Once the flame is removed, the steel cools down very quickly.
Induction heating, on the other hand, will allow the operator to maintain the necessary preheat temperature in order to slow down the cooling rate of the weld puddle. This helps to minimize the risk of cold cracking in the weld, a claim that is supported by the Pipeline Research Council International. The induction heating cables also work well for preheating in-service transmission pipelines because the cables can be arranged to accommodate geometry transitions that are common with split tees used for hot taps and pipe-to-valve welds.
Achieving High Quality Welds with Induction Heating
Among its numerous benefits, induction heating provides greater consistency and faster time-to-temperature, while also minimizing the risk of hydrogen-induced cracking. These are major factors that contribute to the greater success of contractors working in the transmission pipeline industry.