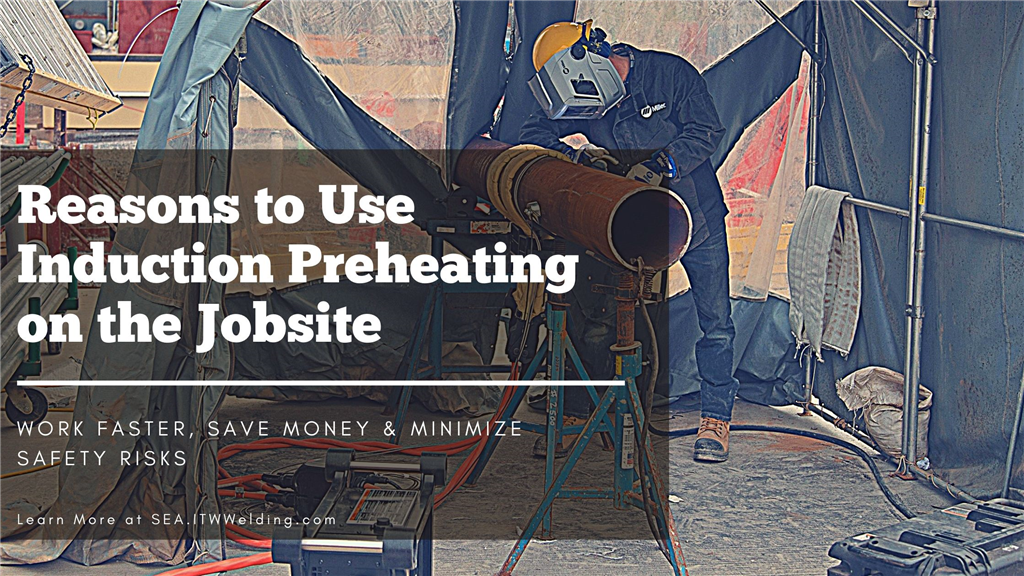
When it comes to preheating welds on the jobsite, the right method can save time and money while reducing safety risks. Let’s compare two common heating methods, induction heating and resistance heating.
Ease of Use
Induction heating is easy to use, so welders can preheat their own joints before welding. Set up is also quick, taking only minutes per weld joint. On the other hand, resistance heating can take up to three hours to set up since each small resistance pad requires power and thermocouple wiring. Teardown times are also lengthy because the resistance pads need to cool down before they can be removed and moved on to the next joint.
.png)
Operating Costs
Because induction heating is simple and easy to use, fabricators can eliminate the need to outsource the heating process to third-party contractors. Resistance heating is usually outsourced and can cost up to thousands of dollars per joint. Fabricators may also experience additional downtime and delays due to miscommunication and poor coordination with their third-party contractors. Lastly, resistance pads often burn out and require frequent and expensive maintenance and replacement. This also means that fabricators must stock extra pads and cables.
Temperature Uniformity
With induction heating, the workpiece itself is the heating element. This means that thorough, uniform heat can be delivered throughout the workpiece. Thermocouple sensors monitor the temperature of the workpiece and provide feedback to the induction heating power source for accurate kilowatt output. Conversely, resistance heating is prone to hot and cold spots because the complex nature of the setup means that the operator may not place the ceramic heating pads uniformly over the part to be heated. In addition, it is also not uncommon for the ceramic pads to burn out or break during the heating cycle, resulting in non-uniform heating.
Heating Efficiency
Induction heating is typically more than 85% power efficient. The process also heats the part from within, so very little heat is lost to the surrounding air, thereby allowing for faster time-to-temperature. Comparatively, resistance heating draws significantly more power and constantly loses heat to the surrounding air.
Safety
Induction heating minimizes the safety risks because the heating cables and wraps do not get hot, and there are no toxic by-products from the process. Since there is no need to wait for the induction heating cables to cool down, they can be safely and easily transferred from one workpiece to the next. Resistance heating uses hot ceramic pads that can cause burn injuries and the pads stay hot long after the workpiece has been brought to temperature. Also, the ceramic insulation that is often used in resistance heating is a carcinogen.
Take Control of Your Preheating
With induction heating, you can work faster, save money and minimize safety risks. Watch the video below to see how easy it is to preheat the TKY joints in offshore jacket structures with Miller’s induction heating solutions. If you would like to arrange for a free demo, reach out to us at SGOffice@MillerWelds.com