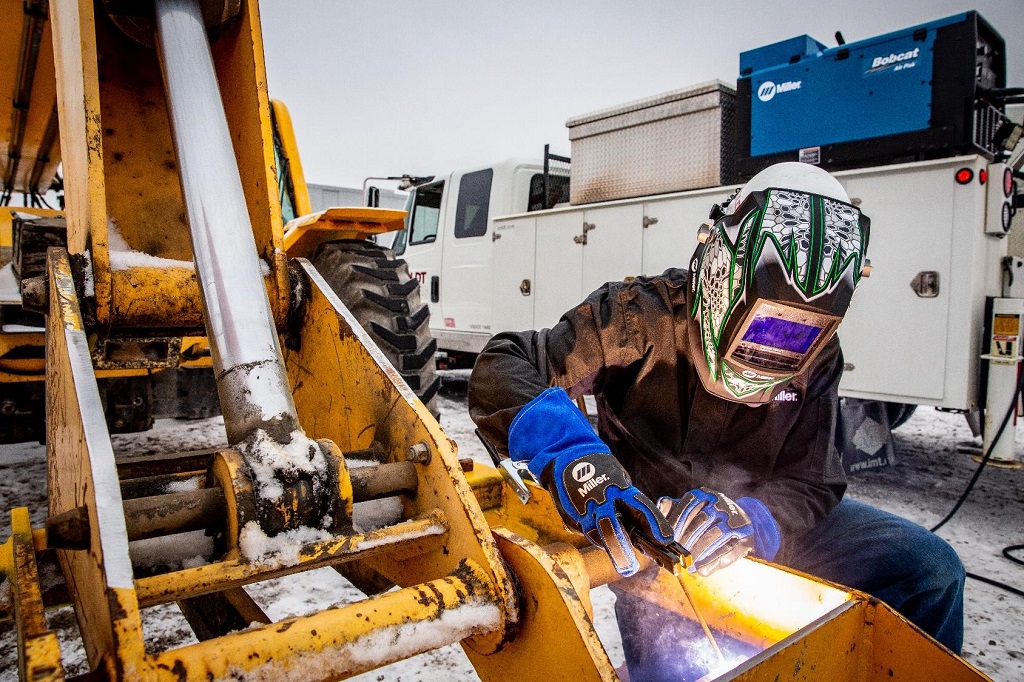
Remote jobsites with no access to power, such as mine sites, pipelines and structural steel projects, typically require the use of diesel engine welding machines. In this article, we will review the process to select the best diesel engine welding machine for the job and the conversation you should be having with your welding supplier.
Welding Process
Firstly, you will need to understand the welding processes that you will be running on the jobsite. Most jobsites in Southeast Asia are still using the Stick welding and TIG welding processes, which only require a constant current (CC) welding machine. However, there is a trend of contractors moving to higher productivity processes such as Flux Cored Arc Welding and Pulse MIG. These processes will require the use of a separate suitcase wire feeder that will be connected to the diesel engine welding machine. In addition, these wire welding processes will need to run on a constant voltage (CV) welding machine. Majority of the Miller Big Blue diesel engine welding machines are capable of running both CC and CV and are true multiprocess welding machine.
Welding Amperage
Diesel engine welding machines that are able to deliver 250-300amps per welding output will usually be sufficient for most welding applications. Certain jobsites have limited space and welders need to work in close proximities. In such cases, 500-600amps diesel engine welding machines that offer dual operator welding capabilities will be ideal. Besides welding, many projects also require the use of carbon arc gouging. A 4.8mm carbon electrode will require about 240amps, while a 9.5mm carbon electrode will need up to 600amps. You have to take these amperage requirements into account when selecting the correct diesel engine welding machine for your application.
Auxiliary Power
Most diesel engine welding machines offer between 5-20kW of power generation capabilities. Choosing the right diesel engine welding machine for the job requires you to first understand what tools you will need at the jobsite, and if you will need to weld and run the tools simultaneously. Knowing the wattage requirements of jobsite tools such as grinders, cut-off saws, lightings etc. will help you to pick the best welding machine. In addition, you should check with your welding supplier if the diesel engine welding machine offers independent welding and generator power. If this is not the case, the welder may face interference with the welding arc when another welder starts to run other jobsite tools.
Air Compressor
Some manufacturers such as Miller Electric have also built air compressors into their diesel engine welding machine. For example, with the Big Blue 800X Duo Air Pak, contractors have a powerful 3-in-1 tool for the most demanding jobsite applications. The air compressor can be used to run pneumatic tools or for carbon arc gouging. This eliminates the need for a separate air compressor on the jobsite, leading to savings in transportation and fuel costs.
Fuel
Diesel is the preferred choice of fuel in Southeast Asia. There are two things that you should take note with regards to fuel. Firstly, check with your welding supplier on the actual fuel consumption of the diesel engine welding machine. If possible, you will want to avoid welding machines that have high fuel consumption. This not only adds to your operating costs, but it also creates a lot of inconvenience in remote jobsites where fuel may not be easily accessible. Secondly, in remote jobsites, you may want to consider a diesel engine welding machine with a larger fuel tank. This can help to reduce the frequency of refuelling and help to avoid unnecessary downtime.
Make an Informed Choice
Selecting the best diesel engine welding machine for your jobsite does not need to be difficult. If you need further clarifications, do reach out to your trusted welding supplier for more details.