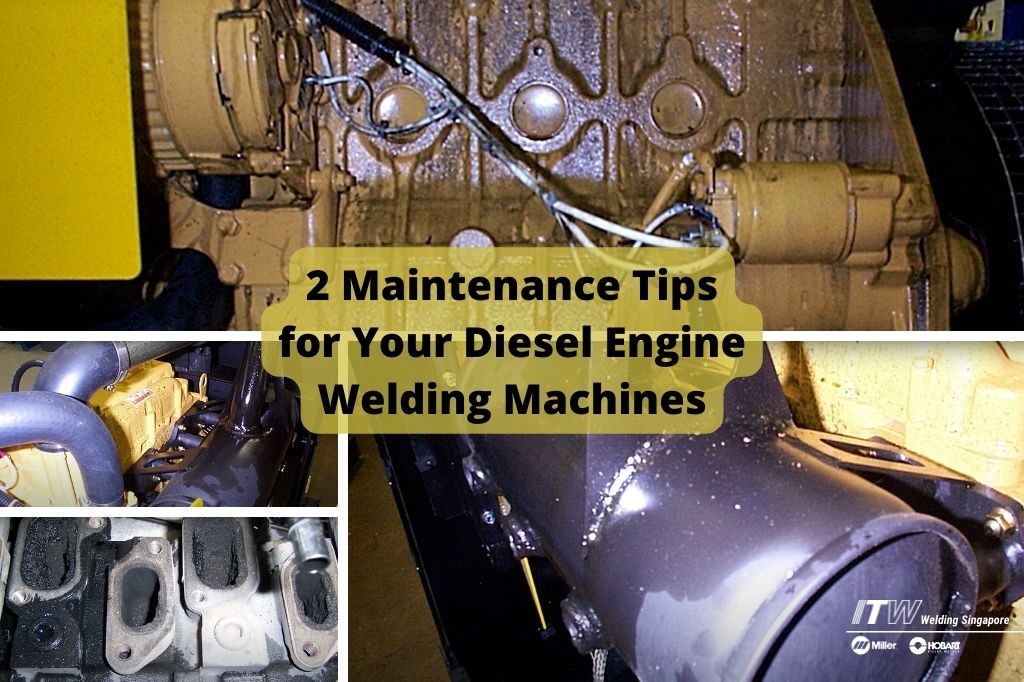
Miller® manufactures some of the best and most reliable diesel engine welding machines in the world. As such, you can always find a Miller® diesel engine welding machine in the mine sites of Indonesia, in the construction sites of Philippines, and onboard an offshore platform in Malaysia. Nonetheless, metal fabricators need to take care of these welding machines to get the most out of them. In this article, we share two maintenance tips so you can minimize unscheduled downtime in the jobsite.
Perform a Run-in Procedure
Diesel engine welding machines are designed and built to work hard, and unlike gasoline engines, diesel engines do not like to idle for extended periods of time. It is important to work a diesel engine early and often throughout its life. Diesel engines need to be run at or near rated loads to properly seat the piston rings and prevent glazing of the cylinder walls. If this is not done, there could be an accumulation of unburned fuel and engine oil in the exhaust system, which is commonly referred to as wet-stacking. If you notice a black, oily discharge from the exhaust pipe, this may be an early sign of wet-stacking. Wet-stacking does not usually cause permanent damage if addressed early but can lead to an expensive repair if ignored. We understand that a typical diesel engine welding machine spends more than half of its life just idling, due to the very nature of field welding and jobsite work. Therefore, many customers ask their welding supplier to perform a run-in procedure to help break-in the engine to prevent wet-stacking. This is typically done by connecting the machine to a load bank and running at or near the machine’s load rating for a minimum of two to four hours.
Implement a Preventive Maintenance Program
Maintenance of a diesel engine is similar to any other engine, but oil change is typically required less often than gasoline engines. It is important to change oil and filters regularly. Be sure to use the oil designed for use in the diesel engine. Don’t sacrifice your engine warranty trying to save a dollar on engine oil. Also don’t forget about the air and fuel filters. It’s important to change the fuel filters regularly and easiest to do so when changing the oil. Again, we recommend the manufacturer’s filters for maximum protection to avoid any warranty conflicts.
When performing routine maintenance, take the opportunity to look for any leaks and loose belts. Tighten or replace parts as needed. Remember to include simple items, such as belts and hoses into your preventive maintenance program. It is easier to replace them periodically than to have the unit go down in the middle of the job and have several workers waiting around unable to work. While not engine related, the generator brushes are another item often overlooked and should be a part of every preventive maintenance program. Brushes are the lifeblood of the generator and cost very little to replace regularly.
Take Care of Your Welding Machine
To summarize what we have covered, try to reduce extended idle times, keep operating temperatures up, and perform regular maintenance and inspections. This will reduce your downtime and keep your workers productive, saving you time and money in the long run. Always refer to the engine maintenance label inside the service door for recommended oils and filter part numbers. For more information, reach out to us at SGOffice@MillerWelds.com