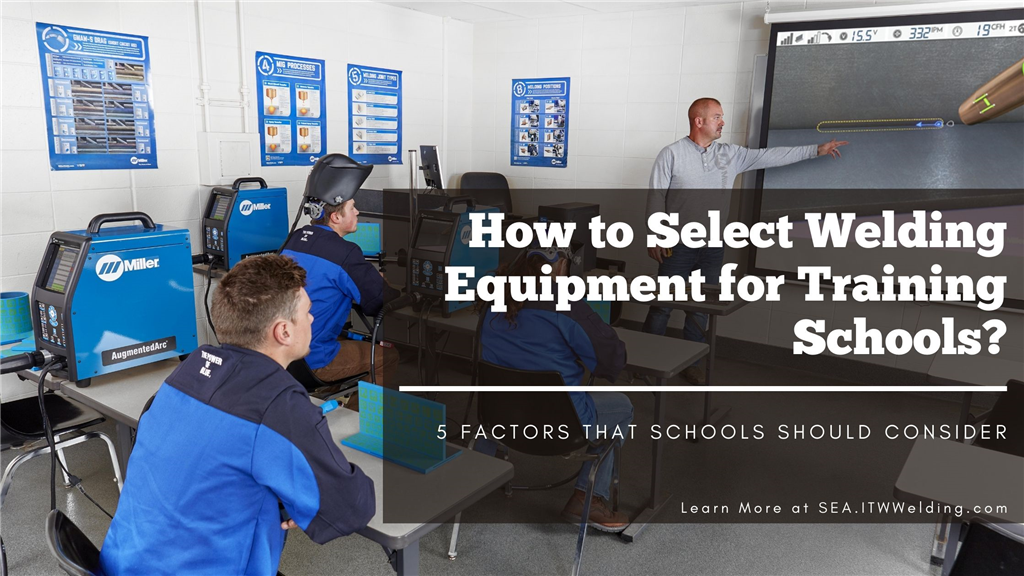
Welding training schools all around the world play an important role in nurturing the next generation of welders. Besides having outstanding trainers and an exceptional curriculum, training schools also need to equip their classrooms and welding booths with the right welding equipment. Here are five factors that training schools should consider when selecting welding equipment.
1. Ease of Use
One way to help new welders develop their skills quickly is by selecting a welding equipment that has a simple user interface and is easy to set up. This means that welders will spend less time fiddling with the settings and can spend more time welding and practicing. For example, the Miller® Multimatic® 255 is outfitted with a 7-inch colour LCD display and soft-key buttons that makes setup or process changes quick, easy and intuitive for any welder. The Multimatic® 255 is also equipped with Auto-Set™ Elite, which automatically recommends the starting parameters to the welder depending on factors such as weld process, material thickness etc. Besides a simple user interface, training schools should also select welding machines that are able to deliver a smooth and consistent welding arc so that students are able to achieve high-quality welds faster, thereby boosting their confidence.
.jpg)
2. Reliability
Similar to how selecting the right welding equipment is critical to productivity on the jobsite, training schools must also equip themselves with welding machines that can keep students productive in the welding booths. Therefore, training schools should invest in proven and reliable welding machine brands, such as Miller®, in order to minimize any unnecessary downtime that can interrupt the training session and cause welder frustration.
3. Versatility
Instead of purchasing Stick machines, TIG machines and MIG machines separately, training schools can consider purchasing versatile multiprocess welding machines that will perform every single welding process. This means that training schools can save space and costs, as compared to using separate welding machines for different processes. A modern multiprocess machine, such as the Miller® Dynasty® 280 DX Multiprocess, not only has a small footprint, but is also capable of more advanced processes such as AC TIG and Pulsed TIG. In addition, because the Dynasty® 280 DX Multiprocess is equipped with Auto-Line™ technology, it eliminates the need for manual linking and allows the welding machine to accept any input power between 208V to 575V (1-phase or 3-phase), thereby providing extra flexibility to the training schools.
.jpg)
4. Updated Equipment
In order for the welders who graduate from training schools to remain relevant, training schools need to keep up with the latest technology that the industry is currently using or going to employ in the future. Therefore, it is important for students to learn first-hand on updated welding equipment so that they are well-prepared when they enter the industry. For example, as the pipe welding industry continues to face a labour crunch and an urgent need to improve productivity, more and more contractors are adopting higher productivity welding processes such as RMD® and Pulsed MIG, instead of the traditional TIG and Stick processes.
5. Augmented Reality
Besides conducting classroom lectures and practical welding sessions, some training schools have started to introduce Augmented Reality (AR) welding solutions in their curriculum. AR solutions in the market, such as the Miller® AugmentedArc® Augmented Reality Welding System, are not meant to replace traditional welding. Instead, the AugmentedArc® is meant to help students learn the basics before live arc welding. The benefits of incorporating AR in the training program include shorter training hours as well as a reduction in material waste and expense on weld coupons.
.jpg)
Make an Informed Decision
Selecting the best welding equipment for your training school does not need to be difficult. If you need further clarifications, do reach out to your trusted welding supplier for an in-depth discussion.