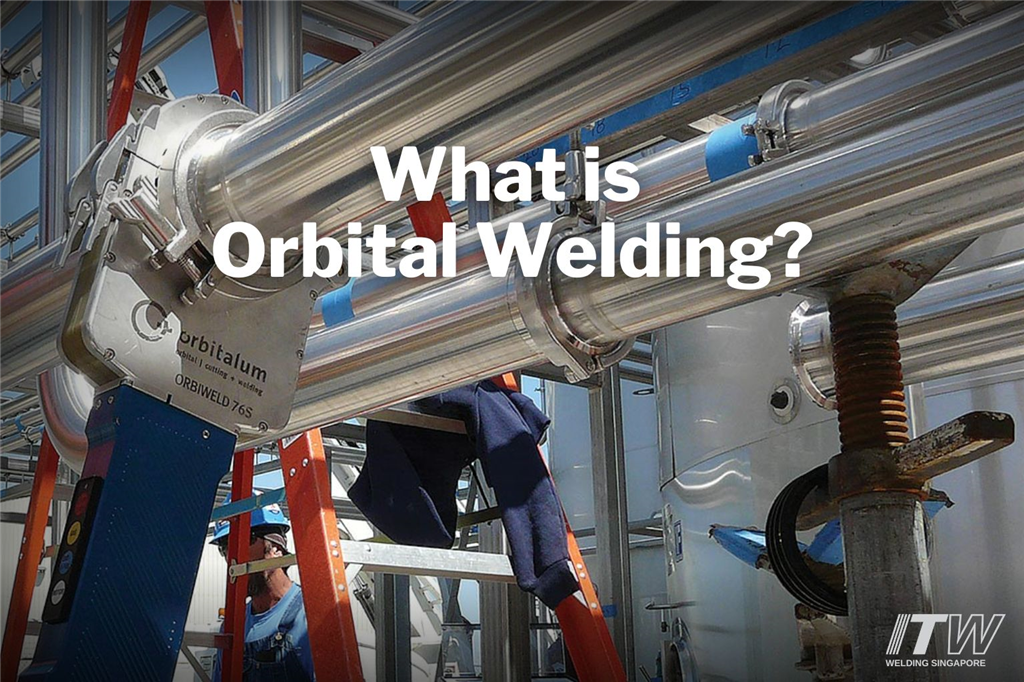
What is Orbital Welding?
Orbital welding involves the rotation of the welding tool around a stationary workpiece, such as a pipe or tube. Orbital welding delivers precision and consistency surpassing traditional manual methods. For high-purity tube welding applications, GTAW orbital welding is a popular choice. The system is made up of two key components, the power source and the enclosed orbital weld head. The welding parameters are set on the power source, while the weld head rotates a tungsten electrode and the electric arc around the weld joint for flawless outcomes.
What are the Benefits of Orbital Welding?
Orbital welding ensures top-quality, pure welds, ideal for applications prioritizing hygiene. The automated process guarantees consistent and repeatable welds, enhancing overall productivity by minimizing rework and material costs.
What are the Common Applications of Orbital Welding?
Orbital welding serves a critical role across industries. In aerospace, it ensures the structural integrity of components like fuel lines. Pharmaceutical manufacturing relies on orbital welding for hygienic, regulatory-compliant welds on stainless steel piping systems. In the food and beverage sector, it creates sanitary welds, preserving production integrity. Additionally, the semiconductor industry benefits from orbital welding's role in producing ultra-clean welds for critical components in semiconductor manufacturing.
Does ITW Welding have an Orbital Welding System?
Orbitalum Tools GmbH, an ITW Welding company, leads globally in providing integrated solutions for precise orbital tube cutting, beveling, and orbital welding. With a commitment to easy handling, top-quality products, and innovative technology, Orbitalum serves industries such as food and beverage, chemical, pharmaceutical, semiconductor, and aerospace. As a single-source solution, the company continuously innovates to meet diverse industry needs.
What is the Flagship Orbital Welding System from Orbitalum?
The ORBIMAT 180 SW is the standard for precision, safety, and productivity in orbital welding. This next generation orbital welding power source seamlessly blends proven features with cutting-edge innovations. Offering online access to projects and parameters through an integrated LAN interface, this system enhances project management and quality assurance. With a 12.4" colour touch display screen and intuitive controls, including a multifunctional dial, operation is user-friendly. The system's digital gas control, Permanent Gas, ensures high-purity welding with minimal gas usage, reducing costs. Unique features such as Flow-Force optimize welding cycles, increasing productivity and duty cycle. The elegant and practical housing, wide input voltage range, and integrated liquid cooling system contribute to the ORBIMAT 180 SW's popularity.
If you want to learn more about the ORBIMAT 180 SW or see a demo, please reach out to us at sherwyn.tan@orbitalum.com