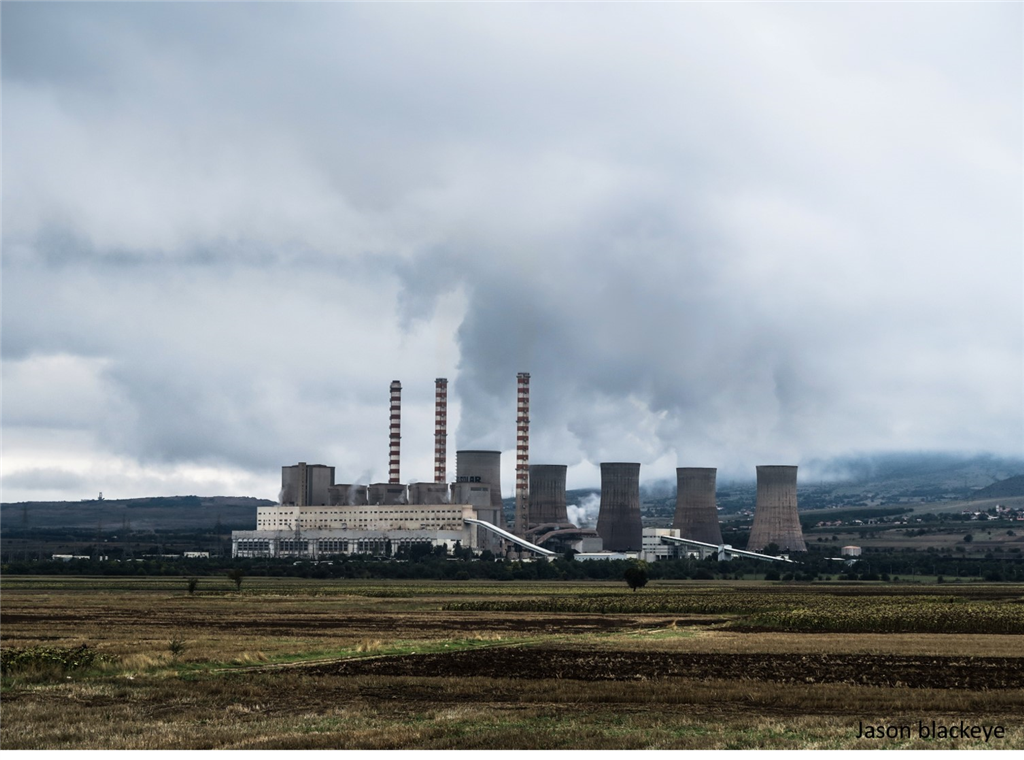
Challenges in the Power Generation Industry
The growing need for new build power plants and the maintenance and repair of aging infrastructure have placed a huge demand for skilled labour in the power generation industry. For example, some power plant projects can span two to three years, and a single project can easily require 100 full-time welders on the job.
For power generation contractors, one of the biggest challenges is finding skilled and experienced welders to complete the project on time, within budget and to the highest quality standards. If deadlines are not met, contractors usually have to pay for liquidated damages. In addition, the communities and industries that rely on the power plant may be starved of electricity.
Implementing Advanced Wire Welding Processes
In order to meet project datelines with a shrinking pool of skilled welders, some industry leaders have converted to advanced wire welding processes such as Regulated Metal Deposition (RMD®) from Miller Electric in both the shop and the field.
The RMD process can offer up to 300% increase in travel speeds as compared to traditional TIG or stick welding. This means higher productivity levels and faster completion times. On some alloys that require back purging, the RMD process will also result in significant reductions in purging gas consumption. Because the welding system gives a stable and precise metal transfer (even with variations in stickout), welders find that RMD is easy to learn and use, allowing even inexperienced welders to consistently produce high-quality welds.
Kiewit is one of the industry leaders who have adopted different welding processes and new welding technologies in their power plant projects. For example, instead of TIG-welding the root pass for P11 and P91 pipe, Kiewit currently uses the RMD process. RMD creates a thicker root pass and a subsequent hot pass is usually not required. For the remaining fill and cap passes, Kiewit uses flux-cored welding instead of stick.
In addition, Kiewit also implemented the use of remote welding technology that allows welders to make parameter adjustments easily at the point of welding, without the need for special control cables. This has reduced the unnecessary walking across the jobsite and eliminated the need to make do with less-than-optimal welding parameters.
The use of advanced welding processes and the latest remote welding technology have improved Kiewit’s productivity and ability to meet critical project schedules and quality standards. Kiewit is now more profitable and competitive than before.
Training and Qualification of Skilled Labour
After Kiewit made the switch to RMD and flux-cored welding, they realized that it was difficult to find welders who were trained in these processes since TIG and stick welding have been traditionally used on many jobsites.
As such, Kiewit decided to partner with unions in the area where they had power plant projects. Kiewit worked with the unions to train and qualify the welders in the wire welding processes that Kiewit was using on its power plant sites. The unions were supportive of this initiative because they recognized the benefits of advanced welding technology and embraced the need to change.
Recognizing the Need for Change
Contractors in the power generation industry will continue to face challenges such as a shortage of skilled welders, a need to meet critical project timelines and an increasingly competitive landscape. Because welding plays a key role in the completion of these deadline-driven construction projects, new welding technologies should be explored and adopted to ensure projects are completed on time and on budget, without sacrificing weld quality.