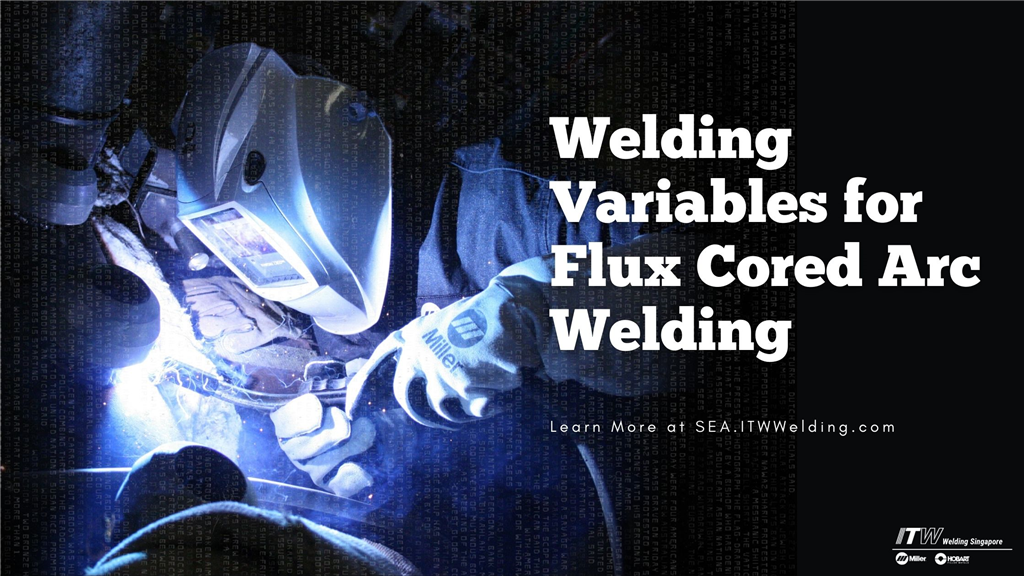
In this article, we will discuss five welding variables for Flux Cored Arc Welding (FCAW) and how these factors affect the welding arc and the formation of the final weld.
Welding Current
Welding current, or welding amperage, plays a huge impact on the deposition rate, weld bead profile and penetration. When other variables are held constant, a reduction in welding current will result in a lower deposition rate, smaller weld bead size and shallower penetration. If the welding current is set too low, large globular transfer and excessive spatter can be expected, in addition to poor penetration and piling up of the weld metal. On the other hand, if the welding current is set too high, the weld bead will become large and convex, and there will be a high chance of burn-through. For most welding machines, the welding current can be adjusted via the wire feed speed control knob on the wire feeder. As the wire feed speed increase, the welding current increases.
Welding Voltage
Welding voltage controls the arc length, which is the distance between the tip of the electrode and the base material. There is an optimum voltage that will provide the smoothest welding arc for a given welding current. When the welding voltage is increased, the weld bead will become wider and flatter. However, excessive welding voltage can cause irregularly shaped weld beads and undercuts. If the arc length is too low, the weld bead will become narrow and convex. The welding voltage can be adjusted via the voltage control knob that is located either on the welding machine or the wire feeder.
Travel Speed
Welding travel speed influences the weld penetration and shape of the weld bead, and there is an optimum travel speed for a given welding current and voltage. When the travel speed is too slow, there is a reduction in penetration because the molten weld puddle gets slightly ahead of the welding arc. In addition, there will be a piling up of weld metal and an excessively high heat input that results in a large heat affected zone. When the travel speed is too fast, the heat input will be too low to melt the base material, resulting in a reduction in penetration. The weld bead will have an irregular, ropy shape and may have undercuts.
Electrode Extension
Electrode extension is defined as the length of welding wire that extends beyond the contact tip. For a typical 1.2 mm diameter gas-shielded flux cored wire, the recommended electrode extension is usually 15-22 mm. In contrast, a 2.0 mm diameter self-shielded flux cored wire will generally require an electrode extension of about 25-32 mm. When the electrode extension varies too much during welding, the welding amperage will fluctuate and may affect the soundness of the final weld. If the electrode extension is too long, the welding current will be too low, resulting in an unstable welding arc, excessive spatter, and reduced penetration. However, if the electrode extension is too short, the welding amperage may be too high, which may lead to burn-through and premature damage of the contact tip.
Electrode Angle
Electrode angle is the angle at which the welding electrode is held with respect to the weld joint. Electrode angle consists of two components, travel angle and work angle. Travel angle is the angle between the weld joint and electrode in the longitudinal plane, while work angle is the angle between the electrode and the plane perpendicular to travel. The travel angle and work angle determine the direction that the arc force acts on the weld puddle, which affects the final weld bead shape and depth of penetration. For example, when welding with a gas-shielded flux cored wire in the flat position, the work angle is usually kept at 90o and a drag travel angle between 2o to 15o is recommended. A drag travel angle is required to prevent the molten slag from running ahead of the weld puddle when welding in the flat position. As the drag travel angle increases, penetration decreases, bead height increases, and bead width decreases.
Contact Us for a Discussion
When all the welding variables are in proper balance, a smooth welding arc and high-quality weld will be obtained. If you want to have a further discussion on welding variables, reach out to us at SGOffice@MillerWelds.com