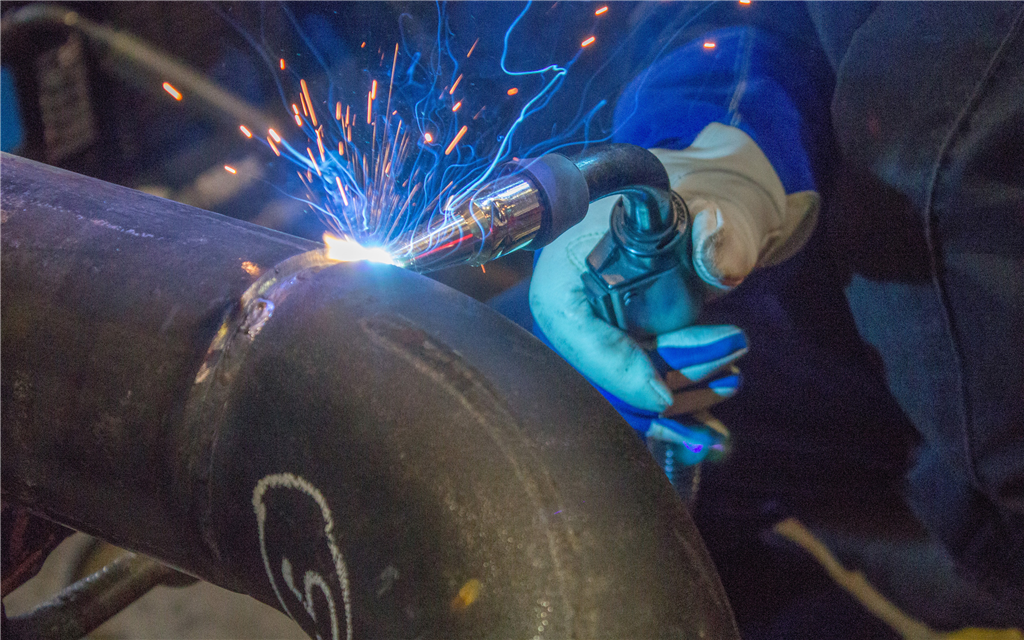
The Fundamentals of P91
P91 (9% chrome and 1% molybdenum) is designed to retain its strength and resist failure due to creep at extremely high operating temperatures and pressures. Because of these features, P91 is used in many critical applications such as high-pressure steam lines, headers and superheaters. Needless to say, the welding codes and procedures for P91 applications are very stringent because any weld defects can result in cracking and catastrophic failure.
In this article, we will discuss some of the challenges most contractors face when welding P91 materials, as well as some solutions to improve both weld quality and productivity.
Heat Input and P91
One of the biggest challenges in welding P91 is its sensitivity to heat changes during the welding process. A material’s microstructure is influenced by how quickly the material cools and the weld puddle solidifies. Too much or too little heat can result in cracking in the heat affected zone (HAZ) and the premature failure of the weld. Therefore, proper control of the heat input before, during and after welding is very important.
Preheating is primarily done to remove moisture and reduce hydrogen. In addition, preheating also helps to reduce the thermal gradient between the base material and the weld puddle to improve weldability and keep the weld puddle from cooling too quickly. P91 is usually preheated in a temperature range of 204 to 315 degrees Celsius.
It is equally important to keep the interpass temperature range within the preapproved welding procedure during welding. Too hot and the material may lose its strength and toughness. Too cool and cracking may occur.
After welding is completed, the heat from the welding process usually makes the weld deposit and the HAZ brittle. Post-weld heat treatment (PWHT) must be conducted to return the material’s microstructure to a favourable state and restore its toughness.
Since precise and stable temperature control is crucial when welding P91 pipe, induction heating is becoming a very popular solution for this application. Compared to traditional heating methods such as ceramic heating pads and flame heating, induction heating induces heat from within the P91 material. This means that induction heating will give a higher uniformity throughout the heat zone and minimizes the chances of hot and cold spots in the material. In addition, advanced induction heating systems can allow for automatic documentation of temperature levels for quality assurance.
Filler Metal Chemistry and P91
Choosing and qualifying the most appropriate filler metal for welding P91 materials is another important element that contractors must consider. The performance of P91 welds are dependent on the chemical composition of the weld metal.
The welding supplier should provide the X-factor for all chromium-molybdenum filler metals. The X-factor measures the weld’s resistance to temper embrittlement. Filler metals for P91 welding applications should typically have an X-factor of less than 15. Furthermore, it is highly recommended that filler metals be purchased with actual test reports showing the chemical analysis for the specific lot numbers.
Lastly, always look for filler metals that have been designed with low hydrogen levels so as to avoid hydrogen-induced cracking in the P91 material.
Advanced Wire Welding Processes and P91
Many contractors are using traditional welding process such as TIG and stick to weld P91 pipes. This may have worked in the past, but it is becoming increasing clear that many contractors are feeling the pressure from the changing industrial landscape. These include shortages in skilled labour, shorter project timelines and a greater emphasis on costs control. For contractors looking to improve profitability and become more competitive, advanced wire welding processes may be considered to increase productivity without sacrificing weld quality.
P91 pipes used in supercritical power plants may have a pipe dimension of 24” diameter, 110mm thickness. Typically, the root pass is TIG welded with an argon back purge. The subsequent passes are usually stick welded, and it will be hours before the P91 pipe is completed and ready for inspection. Switching these processes to a modified short-circuit MIG for the root pass followed by pulsed MIG or flux-cored welding for the fill and cap passes can reduce the total welding time by at least 50% and accelerate project completion. The amount of argon gas that is consumed for the back-purge process is also significantly reduced, resulting in additional costs savings.
The modified short-circuit MIG process (Miller® RMD®) is easy for welders of all skill levels to learn because the machine controls the metal transfer with great precision. The machine anticipates and controls each short circuit and then reduces the available welding current to create a consistent metal transfer with minimal agitation to the weld puddle. Because welders have precise control of the weld puddle, they can create consistently high-quality welds after a short training duration.
Addressing the Challenges Related to Welding P91
In the demanding, high-pressure applications that utilize P91 materials, quality is the most crucial factor. Hence, controlling heat input and selecting the correct filler metals are important elements to consider when welding P91 pipes.
However, in this day and age, contractors are not only expected to achieve high quality standards. Contractors must also successfully tackle challenges related to shortages in skilled labour, shorter project timelines and a greater emphasis on costs control. It is thus important to consider a change in welding processes to save time and money and to gain a competitive edge.