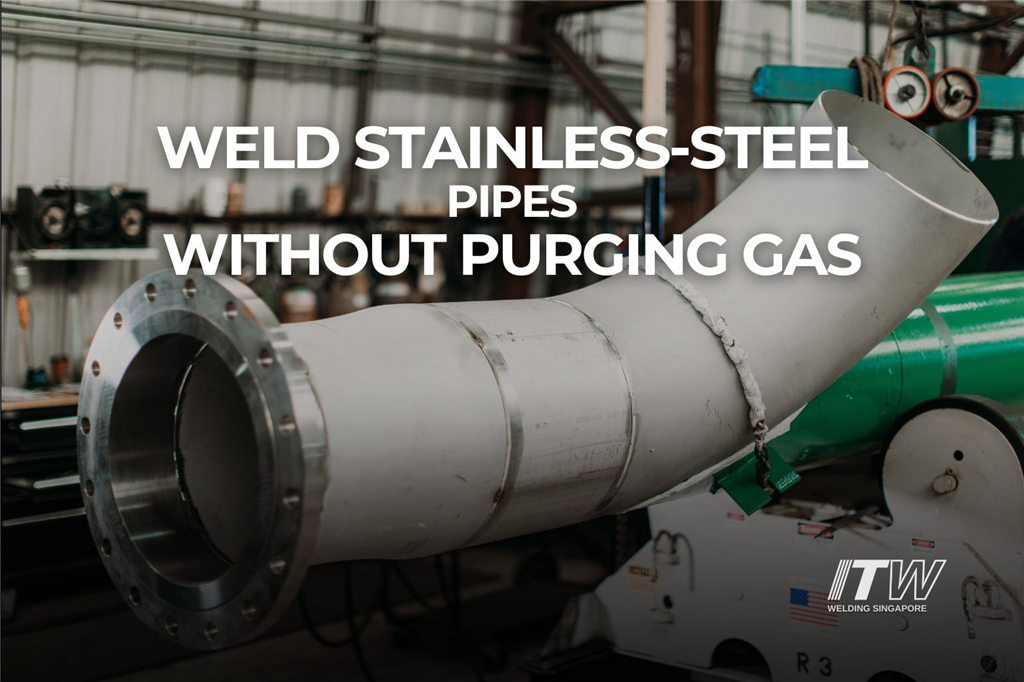
Why Must Stainless-Steel Pipes Be Purged Before Welding?
When engaging in TIG welding of corrosion resistant alloys, such as Grade 304 and 316 stainless-steel pipes, welders are required to purge the interior of the pipe before welding. This process involves utilizing an inert purging gas, commonly known as backing gas, such as Argon. During purging, the atmospheric air and oxygen within the pipe are displaced by Argon, effectively safeguarding both the weld metal and the parent material against oxidation throughout the welding process. Consequently, this preserves the corrosion resistance of the welded stainless-steel pipe.
What Are the Challenges Associated with Purging Before Welding?
There are three main challenges associated with the use of purging gas.
- Firstly, purging is a very time-consuming process and is made up of two parts, set-up time and purging time. Set-up time consists of obtaining a permit-to-work, arranging for Argon gas cylinders onsite, taping up the weld joint, and installing the purge dams and hoses. After set-up is complete, the welder can start the purging process, which can take anywhere from a few minutes to hours, depending on the dimension of the pipe. The welder cannot start TIG welding until a predetermined O2 PPM level is reached.
- Secondly, purging consumes a large amount of Argon gas. Argon gas is expensive and eats into the company’s bottom line. In Southeast Asia, it is very common for fabricators to select filler metals that use 100% CO2 shielding gas, since CO2 is significantly cheaper than Argon gas. If fabricators can eliminate the need for purging gas before welding, and the costly Argon gas associated with purging, fabricators can achieve significant cost savings.
- Lastly, the risk of asphyxiation is high. Since welders are potentially exposed to an oxygen-deficient atmosphere, adequate risk control measures must be in place to reduce the risks. This includes ensuring adequate ventilation in the workplace, providing training for welders, and equipping welders with portable gas meters. Sadly, despite these safety measures, there have been several instances where welders have succumbed to asphyxiation.
Are There Alternatives to Purging Before Welding?
Traditionally, the alternative to purging before TIG welding is to use a Flux-Cored TIG rod for the root pass. For example, Tien Tai, an ITW Welding Company, manufactures a Flux-Cored TIG rod for stainless-steel under the trade name TGFA. With the TGFA filler rod, a slag is produced during welding. This slag protects the back side of the weld bead from the atmosphere and prevents oxidation. As such, the use of purging gas can be eliminated. However, because a slag is produced, the slag needs to be removed after welding. If the welder is unable to access the inside of the pipe to perform deslagging, then the pipe will need to be flushed with fluids to remove the slag. Because of this shortcoming, the acceptance and adoption of Flux-Cored TIG rod is low.
In recent years, Miller Electric, an ITW Welding Company, has developed a new welding technology to weld stainless-steel pipes without the need for purging gas. This welding technology is called Regulated Metal Deposition, or RMD®.
Is It Possible to Eliminate Purging with Miller® RMD®?
By opting for the Miller® RMD® process as an alternative to traditional TIG welding, the necessity for purging gas during the welding of stainless-steel pipes can be eliminated. RMD® is a modified version of the short-circuit GMAW process, primarily tailored for root pass welding in pipe applications. Due to its precise control over metal transfer, the shielding gas experiences minimal disruption as it exits the GMAW gun. This shielding gas effectively flows through the open root of the pipe, displacing the atmospheric air and oxygen within it. As a result, oxidation on the back side of the weld is prevented. Testing has demonstrated that RMD®-welded stainless-steel pipes, even without the use of purging gas, can still meet the expected corrosion resistance standards set by clients.
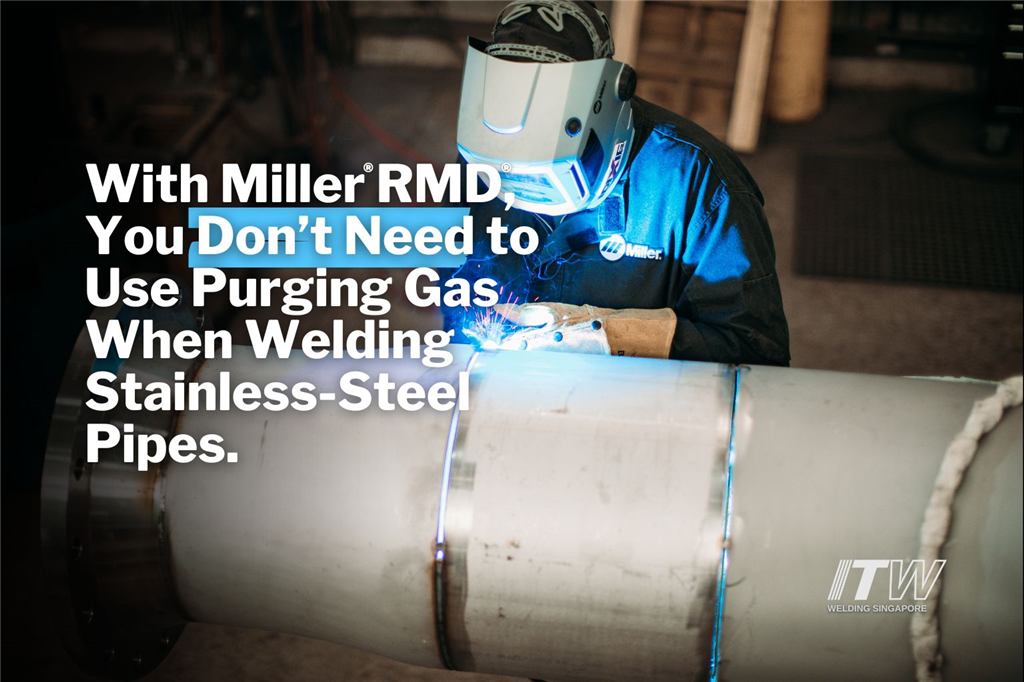
What Are the Benefits of Eliminating Purging with Miller® RMD®?
A company that decides to eliminate purging will experience three competitive advantages.
- Firstly, if purging is eliminated, there will be a significant reduction in set-up time and waiting time. Welders will have more time to focus on value-added activities, such as welding. A higher arc-on time means that the company can weld more pipes per day, improving its competitiveness and ability to take on more projects.
- Secondly, the consumption of Argon gas will be reduced substantially. This will directly reduce the company’s operating costs and improve its profitability. In addition, because considerably fewer Argon gas cylinders will be required, the in-house logistics and warehouse team can better support other aspects of the operation.
- Lastly, by eliminating the use of purging gas, a company can minimize the risk of asphyxiation and improve the working conditions for its welders. This not only helps to reduce Lost Time Accident, but also helps to boost the morale of the welders and enhance the company’s safety track record.
How to Implement the Miller® RMD® Process?
The successful implementation of new pipe welding processes, such as Miller® RMD®, usually requires a strong partnership between the pipe fabricator and its trusted welding supplier. If you are ready to make improvements to your existing pipe welding operations, you can refer to this article, or reach out to us at SGOffice@MillerWelds.com for a more in-depth discussion.