.jpg)
In heavy fabrication industries such as earth-moving equipment and structural steel fabrication, manufacturers consistently strive to enhance productivity and quality. Many seek to achieve these improvements through minimal adjustments to existing processes, aiming for better implementation and cost reduction.
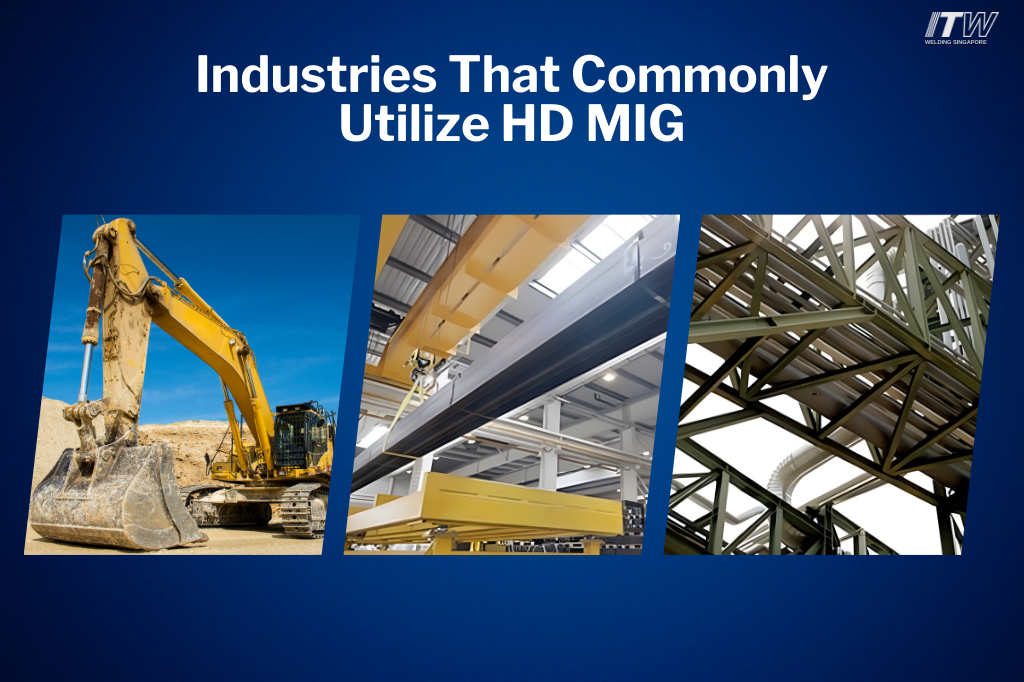
To increase weld deposition rates without complicating operations, a new MIG welding process is now available. Known as High Deposition MIG (HD MIG), introduced by Miller®, this process features a streamlined single-wire setup similar to conventional CV MIG, yet offers higher deposition rates compared to traditional CV MIG processes while minimizing heat input. This advancement facilitates improved bead appearance, enhanced control, greater operator appeal, and reduced distortion, particularly beneficial for large-scale structures.
Miller's HD MIG process program enables the use of longer electrode stick-out while maintaining excellent arc starts and performance. It employs an extended nozzle, increasing the contact tip-to-work distance (CTWD) without altering the operator's perspective.
The welding system includes the Miller® Deltaweld® power source & Intellx™ Elite wire Feeder paired with a Bernard® welding gun featuring long stick-out consumables. Setting welding parameters is made easier with the EZ-Set Synergic mode of HD MIG, allowing users to adjust parameters simply by changing the wire feed speed (WFS). The system is available with both air-cooled & water-cooled setups.
While other more complex options like twin-wire MIG systems can be more prone to feeding issues and arc interferences, welders may find it challenging to adapt to welding with multi-wire systems. HD MIG’s single wire standard MIG set-up retains ease of wire feeding and a conventional look from the operative’s perspective.
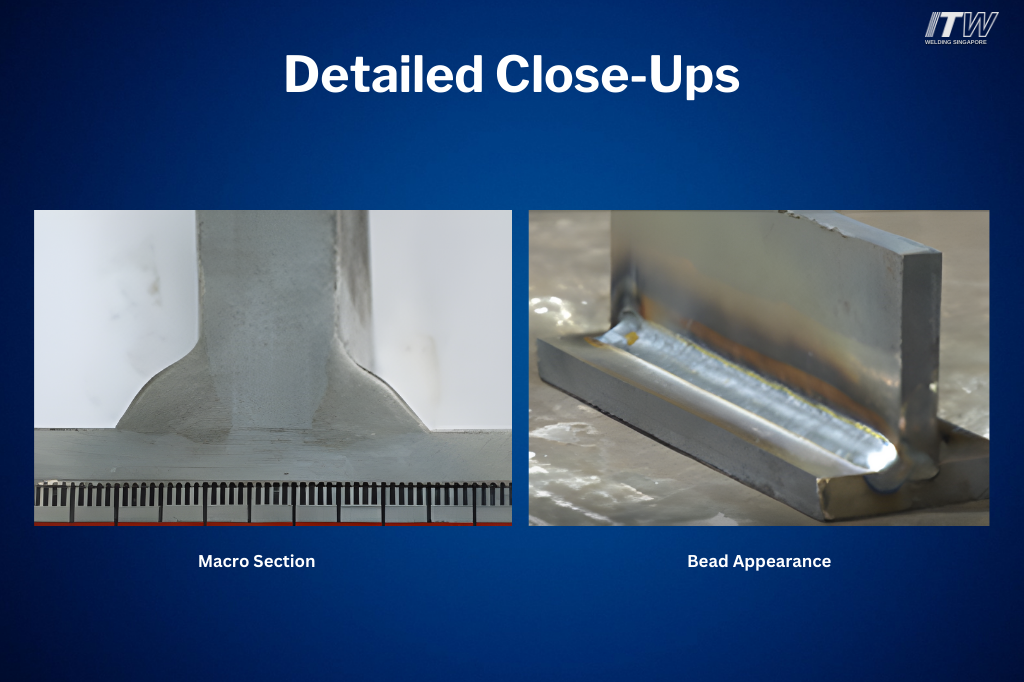
The HD MIG process achieves high deposition rates up to 9.52 kg/h and can weld 8mm fillet leg lengths at speeds up to 550 mm/min, making it a compelling choice for fabricators, including those considering a transition to single wire Submerged Arc Welding (SAW) processes. Typically, single-wire SAW offers deposition rates around 8 kg/h, but its setup is notably more complex compared to an HD MIG system.
HD MIG is suitable for handheld, mechanized or robotic applications and can also be integrated with through-arc seam tracking, further enhancing its versatility in welding applications.
If you would like to know more, reach out to us SGOffice@MillerWelds.com