Diesel engine welding machines are a common sight in remote mine sites and construction sites where there is limited access to power from the electrical grid. The equipment is also ideal for mobile jobsites because it is more versatile and is highly portable compared to a generator set. In this article, we will be sharing 6 best practices when it comes to operating your diesel engine welding machines.
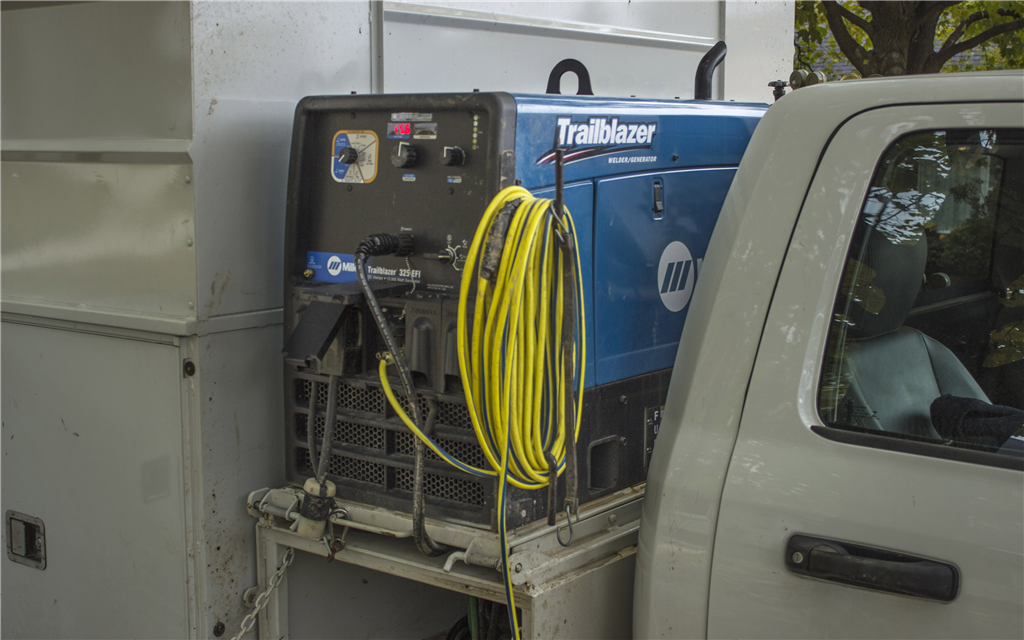
1. Proper Cable Management
In line with housekeeping best practices, welding cables are typically coiled up and kept above ground via cable hangers. This is to avoid any potential tripping hazards. However, many welders tend to leave the cables coiled up during welding, especially when the welding job takes place near the machine. When this happens, a large electromagnetic field is created around the cable hanger, and this can affect the internal components of the welding machine and the arc quality after prolonged use.
Always remember to lay out the welding cables on the ground before welding, even if the welding job is very near to the machine. Alternatively, you can consider installing quick-disconnects throughout the length of the cables, so that you only hook up shorter portions of the cable when needed.
2. Clean and Inspect the Weld Terminals
The next time, before you call up a welding supplier to complain about a faulty welding machine, perform some simple checks first to see if there are any anomalies in the external weld circuitry. Many times, we have found that the welding cables were not tightened properly to the weld terminals, resulting in poor arc performances.
If possible, make it a habit to check the external circuitry every day before beginning your shift, and start the inspection from the weld terminals. If you notice dust or debris buildup at the weld terminals, use a wire brush and clean the terminals. If the welding cables are loosely connected to the terminals, make sure to fasten them before starting your welding operations.
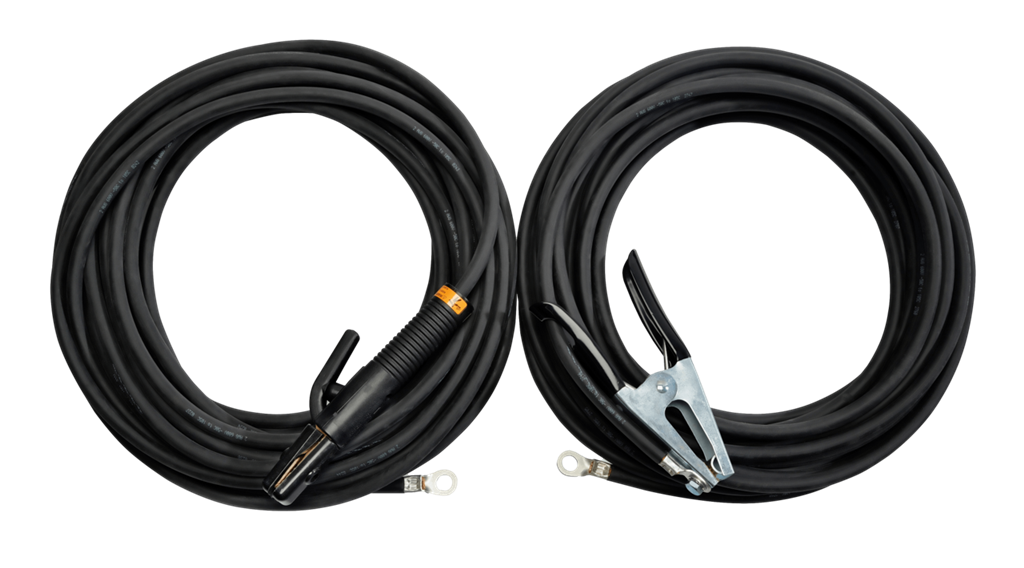
3. Use the Correct Cable Size
When it comes to the external circuitry of the welding machine, the 2 things that are commonly overlooked are the quality and size of the welding cables.
Cables that are priced cheaply typically contain less copper and are a lot lighter in weight. We have seen such cables heat up and melt in the field, causing downtime in production.
70mm2 cables are probably the most commonly used cable size and will be sufficient for most applications. However, if you are performing heavy-duty welding and gouging very far away from the welding machine, chances are, your cables are undersized. Undersized cables tend to heat up quickly and create extra resistance in the circuit. This will affect the arc quality and the lifespan of the machine.
Always use good quality welding cables and approach your trusted welding supplier to understand the recommended cable size for your specific application.
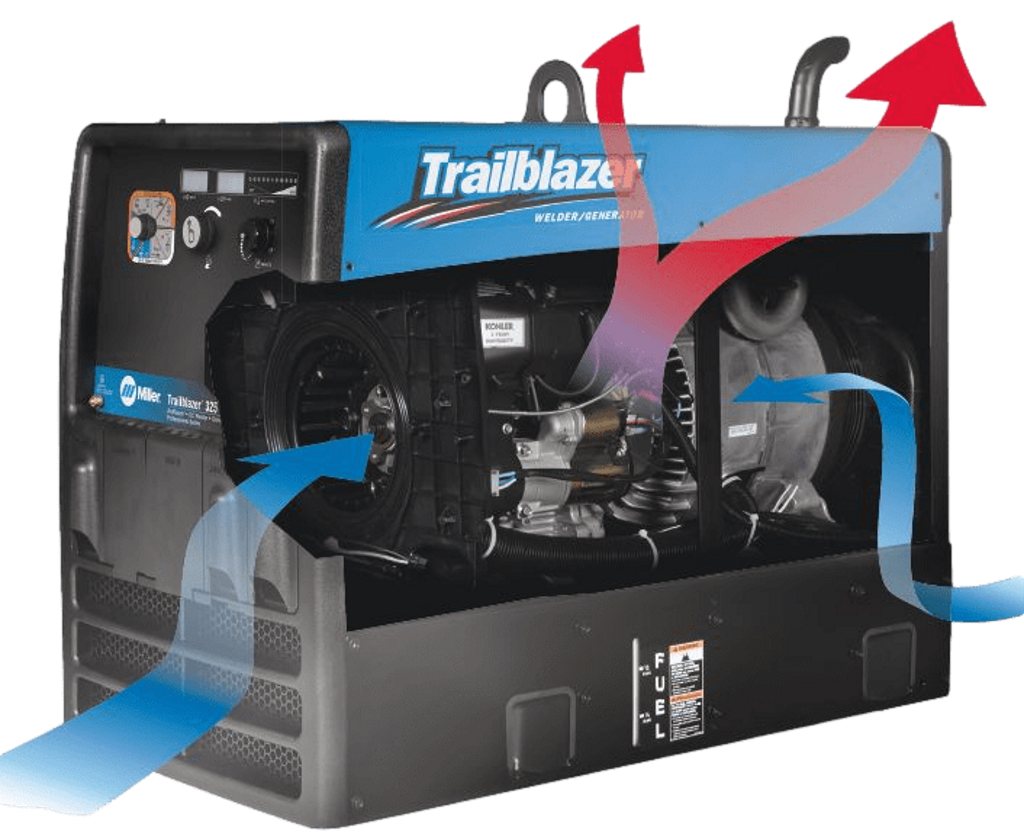
4. Keep the Panels Closed
To maximize the performance of your diesel engine welding machine, always keep the cover, doors and panels closed when the machine is in operation. This allows the cooling air that is flowing through the machine to more effectively cool the engine, generator and sensitive internal components.
If the panel is left open, some of the cooling air will escape from the machine, potentially causing the equipment to overheat. Take care of your machine, and the machine will take care of you on the jobsite.
5. Perform Routine Maintenance
If you own a car, you’ll know that it’s important to replace the engine oil, transmission oil, rotate the tires etc. after the car has covered a certain mileage. Diesel engine welding machines are no different. It is advisable to follow the recommended routine maintenance cycles to ensure you get the most of your equipment and avoid unscheduled downtime. Performing routine maintenance more frequently than expected will not improve the lifespan of the machine and will only add more costs to your operations.
Do take note that different brands and models of diesel engine welding machines are designed different, use various types of engines and have different engine capacities. Hence, always check what the different routine maintenance cycles are, never assume.
For our Miller Big Blues, you will typically find the recommended routine maintenance cycles on the right-side access door of your machine. You can also find the information in the hardcopy or softcopy owner’s manual.
6. Automatic Shutdown Function
Advance diesel engine welding machines, such as those manufactured by Miller, are usually equipped with an automatic shutdown function. This is to protect the machine in situations when there is low fuel, low oil pressure or high coolant temperature.
The next time your Miller Big Blue shuts down automatically, do not try to restart the machine immediately. Look at the gauges on the front panel of the machine and identify the reason for automatic shutdown. If the cause for shutdown is low fuel, for example, simply top up the diesel in the fuel tank and restart the machine to continue with your operations.
If you have any questions or face any challenges with your existing fleet of diesel engine welding machine, feel free to contact us at sgoffice@millerwelds.com