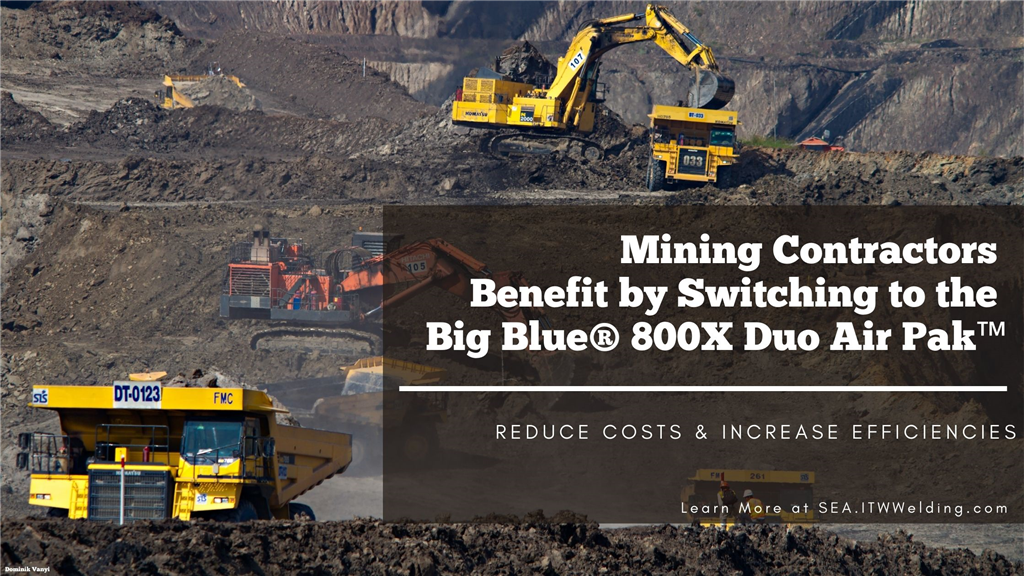
Heavy equipment maintenance and repairs are an everyday fact of life in open-pit coal mines around the world. Mining contractors use hundreds of heavy machinery and equipment such as bulldozers, excavators and dump trucks to move overburden and coal round the clock. Because the equipment have to work in harsh environmental conditions and are subject to constant wear and tear, it is not uncommon for breakdowns to occur.
Such unscheduled downtime can bring the mining operation to a screeching halt, which will affect the productivity on the mine site. For example, an excavator may be working in a team that comprises of five dump trucks. If the excavator breaks down, the output of the mining contractor will be affected since the five dump trucks will also be temporarily put out of service. Prolonged downtime not only impacts the mining contractor’s revenue, but it also costs them money. As a result, most mining contractors have mobile welding crews onsite who can respond quickly to get the heavy equipment back up and running as soon as possible.
The Traditional Repair Procedure
Currently, each welding crew usually consists of two welders and two service trucks. The service trucks haul two diesel engine-driven welding machines and one diesel engine-driven air compressor to the location of the equipment breakdown. Proper coordination between the two service trucks and a good knowledge of the expansive mine site are crucial for the welding crew to arrive at the correct location at the same time with minimal delay. Once they arrive onsite, the welding crew assesses the situation and gets to work by using the air compressor to perform carbon arc gouging on the cracks found on the heavy equipment. Subsequently, the welders will use the diesel engine-driven welding machines to carry out the welding operation simultaneously, so as to speed up the repair process. Depending on the repair job, the welders may choose between Stick and Flux-Cored Arc Welding processes, so it is important that the welding machines have multiprocess capabilities. Welders will also need to utilize the auxiliary power on the diesel engine-driven welding machines to power jobsite tools such as grinders and lighting.
As with most repair jobs, welders need to change the weld settings frequently in order to deal with varying metal thicknesses and changes in welding positions. Presently, the welders will have to walk back to the service truck to access the welding machine in order to make parameter changes. This is not only time-consuming, but also increases the risks of slips, trips and falls on the jobsite.
Introducing the Miller® Big Blue® 800X Duo Air PakTM
Understanding the challenges that welding crews face in the mine site, Miller® designed the Big Blue® 800X Duo Air PakTM to help mining contractors reduce operating costs and increase productivity. Unlike traditional diesel engine-driven welding machines, the Big Blue® 800X Duo Air PakTM offers two welding outputs instead of one. This means that the Big Blue® 800X Duo Air PakTM is able to deliver 400 amps per output when set up in dual-operator mode, or up to 800 amps in single-operator mode. The welding machine is also equipped with an Ingersoll Rand rotary screw air compressor that has a 30,000-hour life expectancy and a generator that is capable of 27,000 watts of peak power. Therefore, welders can use the same machine to weld, to gouge and to power tools on the jobsite.
.jpg)
Reduce Costs
With this all-in-one diesel engine-driven welding machine, the welding crew now only requires one machine and one service truck to perform their job, instead of three machines and two service trucks. This translates to a significant upfront costs savings for the mining contractor. In addition, operating fewer machines and service trucks means a reduction in fuel consumption as well as maintenance costs. Given the undulating terrain in the mine site, the suspension of the service trucks are usually subject to heavy abuse, so the weight savings as a result of transporting one machine will help to reduce the rate of wear and tear.
Increase Efficiencies
Since the welding crew can now drive to the specific location on the mine site in one service truck, this will eliminate any issues related to poor coordination, and more time can be spent to restore the heavy equipment back into service. The use of the Big Blue® 800X Duo Air PakTM will also help to reduce jobsite clutter and noise pollution, since fewer machines are required, thereby improving the work environment for the welding crew.
In addition, the Big Blue® 800X Duo Air PakTM is equipped with Miller’s exclusive ArcReach® technology, which will allow the welder to have complete control of the welding parameters at the point of welding. Welders will be able to fine-tune the parameters without having to walk back to the welding machine that is mounted on the service truck. This helps to enhance jobsite safety and productivity especially when welders are repairing massive pieces of heavy equipment on the expansive mine site.
Make the Switch Today
If you are looking to improve your welding operations in the mine site, reach out to us at SGOffice@MillerWelds.com for an in-depth discussion.