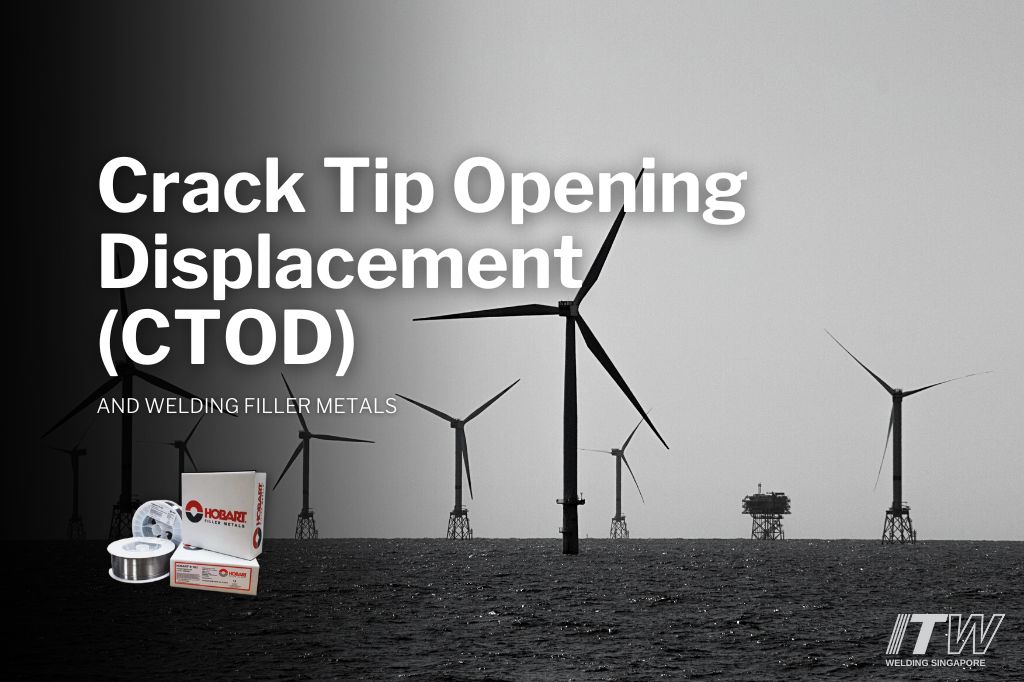
What is CTOD?
There are two common methods to measure fracture toughness, i.e., Charpy-V test and Crack Tip Opening Displacement test, or CTOD. The Charpy-V test is a simple, qualitative test that only gives an indication of the toughness of a metal. A small, standard notched specimen is fractured via a swinging pendulum. The amount of energy (represented in Joules) that is required to fracture the specimen gives an indication of the notch toughness of the test material. If a small amount of energy is absorbed by the specimen, this would indicate that the material is brittle.
In order to measure fracture toughness accurately, CTOD is conducted. Unlike the small, inexpensive Charpy specimen, the CTOD specimen is usually the full thickness of the material. The most common specimen geometry used is the Single Edged Notch Bend (SENB) specimen. This specimen, which contains an artificially induced fatigue crack in the centre, is placed in a 3-point bend fixture and submerged in a cooling bath. A load is then applied at a rate that is representative of the service conditions. The crack tip opening (represented in millimetres) is measured throughout the test via a strain gauge until a fracture event takes place. Similar to the Charpy-V test, three tests are conducted to ensure consistency of results.
CTOD and Welding Filler Metals
In the offshore industry, CTOD tests may be specified for steels used in subsea pipelines, offshore wind farms or for heavy steel plates used in ship hulls and decks. The test temperature is equal to or lower than the service temperature. For most offshore projects, the typical CTOD requirements for welding filler metals are 0.15mm to 0.38mm, at 0oC or -10oC. As per DNV testing code, the qualified thickness range is 0.5 x t to 1.1 × t, where t is the thickness of test piece.
Recently, there has been an increasing number of offshore projects with more stringent CTOD requirements at lower temperatures. To meet the ever-increasing needs of the offshore industry, welding manufacturers are constantly formulating new and improved filler metals. For example, Hobart® 811K2 is a 100% CO2 flux-cored wire that is designed to achieve excellent CTOD values at -20oC. Other Hobart® filler metal products that are designed to meet the CTOD needs of the offshore industry include:
When evaluating welding filler metals, offshore fabricators should ask their welding suppliers to submit both the CTOD values as well as the actual test report. When reviewing the test report, pay attention to the thickness of the CTOD specimen in the test report. All else being equal, CTOD values tend to be higher when the specimen is thinner. If the specimen is thinner than the actual thickness requirement of the offshore project, fabricators should ask the welding supplier to perform a retest and resubmit the new CTOD results. The retest should be done on the actual plate thickness or on a thickness that is reasonably close to actual plate thickness of the project. By doing so, offshore fabricators can perform a more objective evaluation and select the most suitable welding filler metal for the project.
If you have any questions on CTOD and welding filler metals, feel free to reach out to us at SGOffice@MillerWelds.com