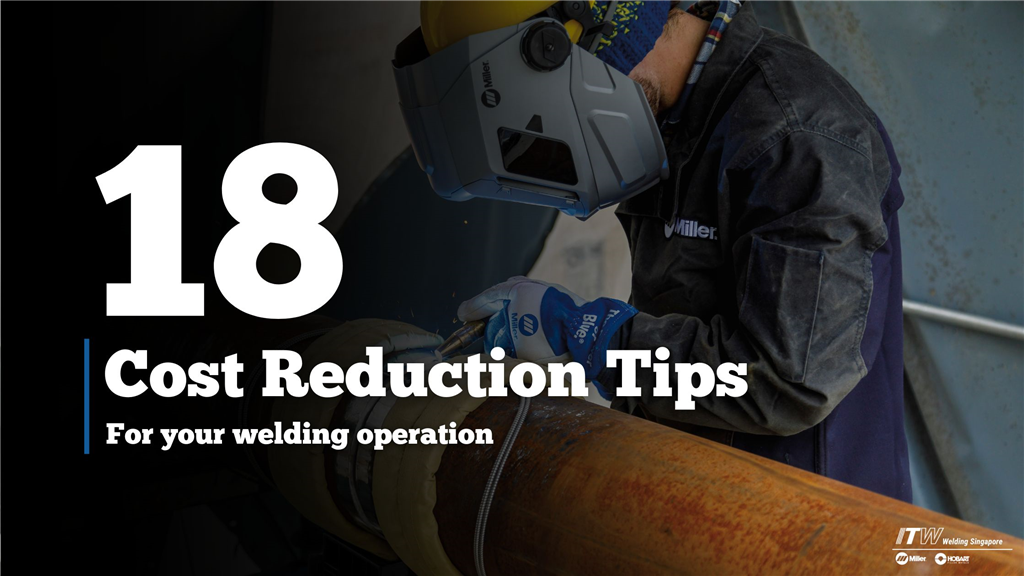
18 Cost Reduction Tips for Your Welding Operations
Metal fabricators are facing issues such as rising costs and increased competition for projects. Many metal fabricators are looking at Cost Reduction Programs to ensure the long-term profitability of the company. Here are 18 cost reduction tips which you may find useful.
1. Adopt a growth mindset
One of the biggest hidden costs in any operation is the cost of maintaining the status quo and not considering more productive solutions.
2. Dual-operator capabilities
An engine-driven welder that provides multiple arcs translates to a lower cost-per-arc and fuel savings.
3. Eliminate unnecessary walking
With Miller's ArcReach® remote control technology, welders can spend more time welding instead of walking to the welding machine to make parameter and process changes.
4. Eliminate back purge
Using Miller's RMD® process for the root pass on stainless steel pipes, operations may save time and money by eliminating the back purge process.
5. All-in-one engine-driven welder
An all-in-one welder, generator and air compressor solution can provide space savings, fuel savings and reduced maintenance cost.
6. Detect quality issues early
The costs of missed or defective welds that go undetected escalate at every stage in the welding operation and beyond. Welding information management systems can provide visualization of the part to guide new welders through the weld sequence and avoid missed or defective welds.
7. Embrace new training solutions
Augmented Reality Welding Systems can reduce the overall training time and minimize material cost.
8. Purchase on quality, not price
Cheaper machines may experience more breakdowns, which mean higher maintenance costs and lost productivity.
9. Look beyond the up-front cost savings
Cheaper filler metals tend to be associated with poor weldability and excessive spatter that hinder productivity.
10. Quick process changeover
Consider welding machines that have a simple user interface and memory function to reduce switch-over time.
11. Switch to induction heating
For shorter setup and teardown times, faster time-to-temperature, and lower consumable cost as compared to flame and resistance heating.
12. Invest in new technology
Miller's Accu-Pulse® process provides a more forgiving arc so that inexperienced welders can produce quality welds faster and more consistently.
13. Introduce simple mechanisation
For significant improvements in throughput and quality (without breaking the bank), consider using a positioner to weld pipes in the 1G position.
14. Practice preventive maintenance
Scheduled downtime helps keep the production line flowing smoothly and reduces time and costs spent on unplanned maintenance.
15. Choose the best consumables for the job
Cheap contact tips and nozzles typically don’t last as long, and they cost more in labour and downtime due to frequent changeover.
16. Select the optimal wire packaging
Packaging that is too small increases changeover rates and production downtime, while packaging that is too large can cause wastage of the welding wire.
17. Minimize non-value-added activities
Changing the welding process or filler metal can help reduce the time spent on grinding, sandblasting, and chipping.
18. Increase welder retention
Improve your company's culture and environment to attract and retain skilled welders so as to minimize time and money associated with rehiring.
If you need help to reduce the costs of your existing welding operations, reach out to us at SGOffice@MillerWelds.com