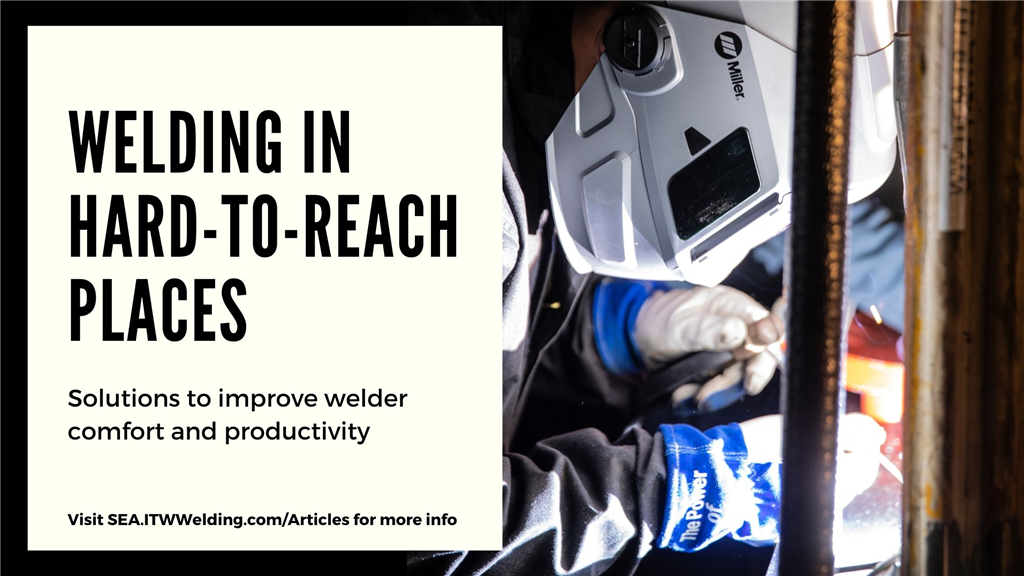
In demanding jobsites such as power plants, refineries and shipyards, welders may find themselves working in tight spots or hard-to-reach spaces. In such instances, it is difficult for welders to get into a comfortable welding position or to use proper weld techniques. Safety is also a concern as welders will be in close contact with weld fumes. In addition, welders may be required to climb up ladders or crawl through small spaces to get to the weld joint. This means that the welding machine is usually placed faraway, and the welder has to either make do with the pre-set parameters or travel back to the welding machine to make necessary changes, negatively affecting weld quality and productivity. Nonetheless, these challenges can be addressed if the right welding solutions are implemented.
Solutions to Improve Welder Comfort and Safety
Hard-to-reach areas also tend to be low-light environments. This means that welders have a difficult time seeing the weld puddle and the workpiece with traditional welding helmets, resulting in unnecessary eye strain and discomfort. To address this issue, Miller Electric developed ClearLight Lens Technology that will allow more wavelengths along the colour spectrum to come through the helmet lens. This technology improves visibility by giving welders a clearer view of the weld pool and the surrounding workpiece while welding, thereby reducing welder fatigue. Newer helmets also allow for lightweight LED torchlights to be securely attached.
When welding in confined spaces, the position of the welder’s head or a physical obstruction can block the auto-darkening helmet’s sensor and prevent the lens from darkening. In order to overcome these challenges, Miller Electric developed X-Mode Lens Technology. X-Mode uses an electromagnetic sensor to pick up the magnetic frequency of the welding arc, and the lens will darken when welding takes place. This technology ensures that the welder’s eyes are always protected from the harmful radiation of the welding arc.
Admittedly, there can also be some demanding jobs that may be too small for a welder to enter with a welding helmet due to space constraint issues. In such instances, the Miller Electric Weld-Mask may be a suitable alternative. This lightweight and portable solution can allow for much better access in confined areas while ensuring eye and head protection for the welder.
In addition, welders can invest in TIG torches or MIG guns with rotatable or flexible necks when welding in different angles and hard-to-reach areas. These welding accessories can be easily adjusted without the use of tools and can significantly improve welder’s comfort and control when welding in difficult positions.
Lastly, in order to protect welders from the harmful weld fumes, respiratory protection should be implemented when welding in tight spaces. A disposable mask is the most basic solution. For extra protection, welders can consider a portable Powered Air Purifying Respirator (PAPR) solution. The Miller Electric PAPR uses a blower to force ambient air through an air-purifying element and a hose to the welder's helmet, thereby providing all-day comfort and protection.
Solutions to Improve Weld Quality and Productivity
When working in hard-to-reach places, jobsite productivity can be negatively affected when the welder needs to constantly walk back to the welding machine to make process and parameter changes. This also increase the risks of slips, trips and falls at the jobsite. Sometimes, in order to avoid walking back to the welding machine, welders may choose to make do with the pre-set welding parameters, which may result in poor quality welds.
To address these challenges, Miller Electric developed the ArcReach Technology that will allow welders to make all parameter and process changes at the point of welding. This technology eliminates all unnecessary walking in the jobsite, thereby improving jobsite safety, productivity, and weld quality. For example, welders working in power plants and refineries usually need to switch between TIG and Stick welding processes. With the XMT 350 FieldPro Polarity Reversing (equipped with ArcReach Technology), welders can easily switch parameters and processes at the point of welding with the push of a button. This means that the welder only needs to enter the confined area once, complete the welding assignment, and leave the area promptly and safely.
Make an Informed Decision
Welding manufacturers and suppliers are constantly developing innovative solutions to improve welders’ comfort and efficiency. If your welders are regularly working in difficult environments, contact your trusted welding supplier to learn about the latest welding technologies and accessories that can improve jobsite safety, productivity and weld quality.