.jpg)
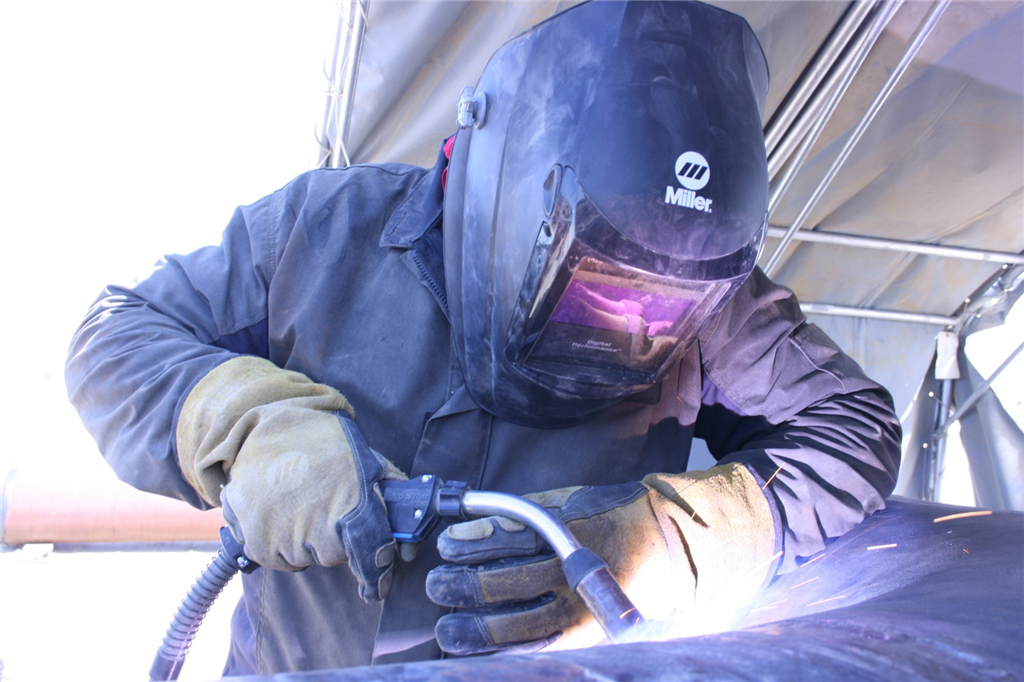
.jpg)
TC Energy
TC Energy owns and operates multiple oil and gas pipelines and natural gas storage facilities in Canada, USA and Mexico. Given the recent trends in pipe welding, i.e., the shortage of skilled labour and the introduction of new pipe welding processes, TC Energy has been working with its contractors to explore more efficient methods of welding.
Traditional welding and heating processes
For pipe welding projects in the field, the contractors had previously performed preheating of the P1 pipe material with a flame torch, followed by stick welding. E6010 electrode was typically used for the root pass, followed by E*018 electrode for the fill and cap passes. Traditionally, it would take TC Energy’s contractors 11 ½ hours to complete welding a 48-inch pipe with a 1-inch thickness. Because large-bore pipes require more weld time, TC Energy decided to focus their efforts here to explore new pipe welding processes that would allow higher efficiency gains and bigger savings.
Testing and implementing new wire welding processes
After conducting multiple studies with its contractors, TC Energy decided to evaluate Miller’s Regulated Metal Deposition (RMD) for the root pass followed by FCAW for the fill and cap passes on large-bore pipes, as a substitute for the existing stick welding process. Working as a team, TC Energy and its contractors tested the new wire welding processes in the shop first to ensure everything would meet the project requirements. After the new Welding Procedure Specification (WPS) was qualified, the welders took part in several days of training before undergoing Welder Qualification Tests. During this period of time, the welders were able to familiarize themselves with the new processes as well as clarify any doubts or uncertainty. Because RMD is an easier and more forgiving welding process, even the less experienced welders were able to grasp it quickly and produce high-quality welds in a short timeframe.
With proper training, qualification and buy-in from all parties, TC Energy and its contractors were able to conduct multiple successful trial on large-bore pipes in the field. Welders were not only able to produce consistently high-quality welds with less than 1% repair rate in the field but were also operating at a much higher efficiency. A 48-inch pipe with a 1-inch thickness currently takes only 5 ½ hours to complete, a 52% increase in productivity. Because a welder is now able to complete two large-bore pipe welds in a shift, instead of one, TC Energy is able to keep projects on schedule and within budget without affecting the safety of the piping system. Following these successes, TC Energy decided to roll out the new welding processes on all large-bore pipes (more than 16-inch diameter) in the field.
Switching from flame to induction heating
With the traditional flame heating process that is used for preheating, TC Energy and their contractors had experienced inconsistent heating throughout the entire pipe, especially for large-bore pipes in the field. In order to rectify this issue, TC Energy tested and introduced Miller’s induction heating system.
Upon testing the new induction heating system on large-bore pipes in the field, the welders commented that the weldability had improved because the weld puddle reacted more consistently given the uniform heat distribution. In addition, induction heating further improved the efficiency in the field since preheating now takes 5-10 minutes, instead of 20-25 minutes with a flame torch. The elimination of open-flame onsite also improved the safety of the pipe welding operations significantly.
Significant productivity gains
Traditional welding and heating processes will always have a place in pipeline projects. However, it is important to consider other options that can yield high-quality and significant productivity improvements without affecting the safety of the pipeline system. Also, spearheading a new process requires involvement from all stakeholders. Despite the learning curve associated with introducing new welding processes, TC Energy and its contractors found success because they were able to align their goals and expectations from the very beginning.