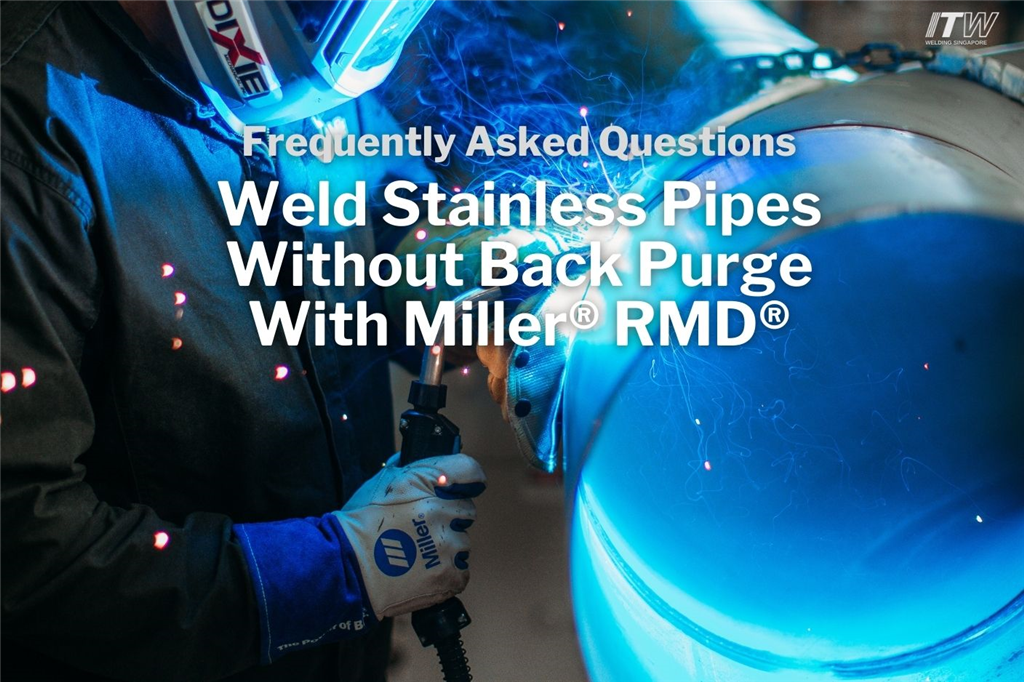
When TIG welding stainless pipes, welders use argon as a purging gas to displace oxygen inside the pipe. This protects the weld and the pipe from oxidation during welding and preserves their corrosion resistance.
The traditional practice of back purging presents three main challenges to welding contractors:
- Purging involves time-consuming setup and lowers productivity.
- Argon gas is expensive and reduces the company’s profitability.
- Welders are at risk of asphyxiation despite the existing safety measures.
To overcome these challenges, Miller Electric introduced the RMD® (Regulated Metal Deposition) weld process that can eliminate the need for purge gas when welding certain stainless pipes. In this article, we will address the frequently asked questions about this innovative technology.
What is the RMD® weld process?
RMD®, or Regulated Metal Deposition, is a modified short circuit MIG welding process that is developed by Miller Electric for the root pass welding of pipes. The welding machine anticipates and precisely controls each short circuit to create a consistent metal transfer with minimal weld puddle agitation. Because of this calm, stable arc, welders are able to produce consistent, high-quality welds within a short training duration. Additionally, RMD® helps to boost productivity as it offers travel speeds that are two to three times faster than the traditional TIG process.
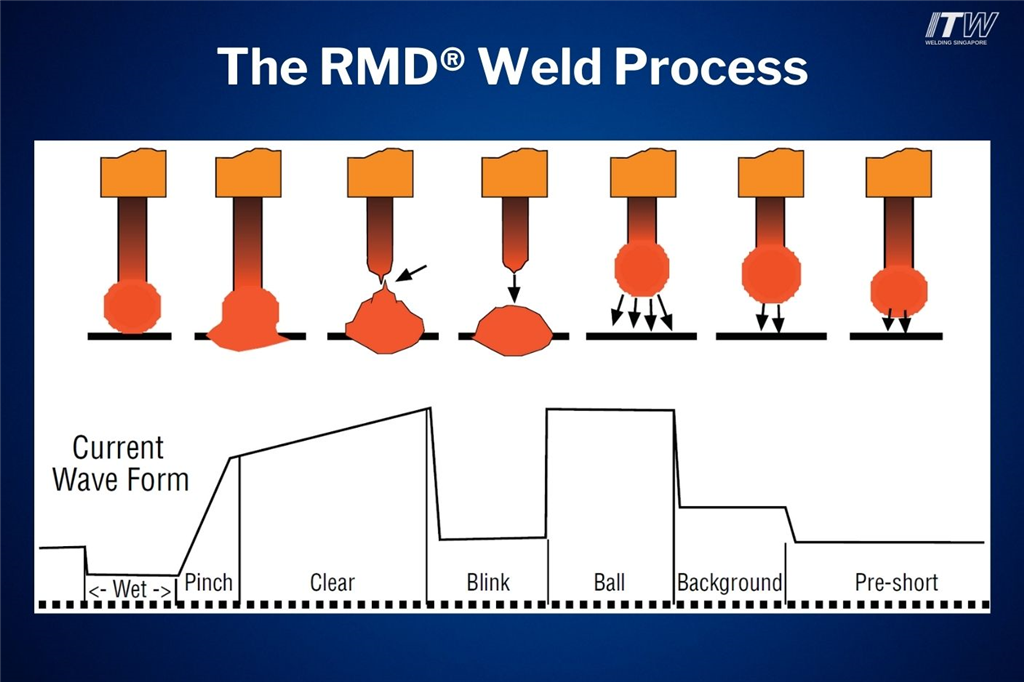
Why is it possible to eliminate back purge with RMD®?
With RMD®, the precise metal transfer and a fast-freezing weld puddle allows the shielding gas to exit the MIG gun with minimal disruption. This shielding gas effectively flows through the open root of the pipe and displaces the atmospheric air within it. As a result, oxidation on the back side of the weld is prevented.
Which grades of stainless steel can be welded with RMD® and no purge gas?
Stainless steel grades 304 and 316 are the most common base materials that can be welded with RMD® without backing gas. For duplex and super duplex materials, RMD® can be used, but we recommend that a purge gas be employed during welding. On a side note, chrome moly pipes, such as grade P91, can also be welded without a back purge if RMD® is used.
Which welding machines offer the RMD® process?
RMD® is a patented weld process developed by Miller Electric and can only be found on certain Miller® welding machines. For pipe fabrication shops, the PipeWorx Welding System is a popular choice. When pipe welders have to work in the field, but have access to electricity, they can choose the XMT® 400 and ArcReach® Smart Feeder combination for improved portability. If there is no access to electricity, then a diesel engine welding machine, such as the Big Blue® 500X Pro, can be paired with the ArcReach® Smart Feeder to deliver RMD® in the field.
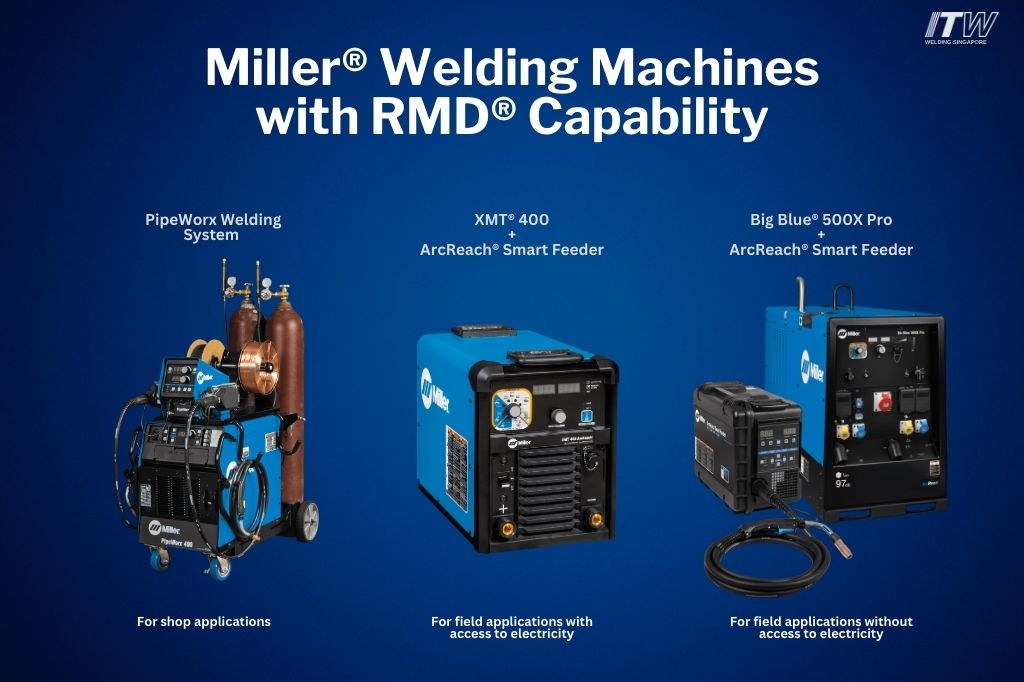
Which filler metals are used with the RMD® process?
When Miller Electric developed the RMD® stainless weld programs, the design and evaluation were based on the Hobart® 308L HiSil and Hobart® 316L HiSil MIG wires. As such, to achieve the best results with the RMD® process, with or without back purge, we recommend that you pair Miller® welding machines with Hobart® filler metals. Do note that it is best to use a filler metal with higher silicon content as it helps to improve weldability.
Which shielding gas should be used with Miller® RMD®?
We generally recommend two types of shielding gas when welding stainless pipes with the RMD® process. The first is a trimix gas, consisting of 90% helium, 7.5% argon and 2.5% carbon dioxide. The other option is 98% argon and 2% carbon dioxide. In Southeast Asia, the latter is more common because it is the cheaper option.
Can the RMD® process be used in all positions?
The RMD® process is designed to weld in all positions. Typical pipe welding procedure qualifications are done in 1G rotating, 5G or 6G positions. Pipe welders predominantly weld in the 5G or 6G position when in the field. In the pipe shop, some contractors have decided to implement RMD® in the 1G rotating position to achieve higher throughput. This is usually performed via a handheld mechanized setup, or a fully mechanized system, depending on the contractor’s budget, project timeline and many other factors.
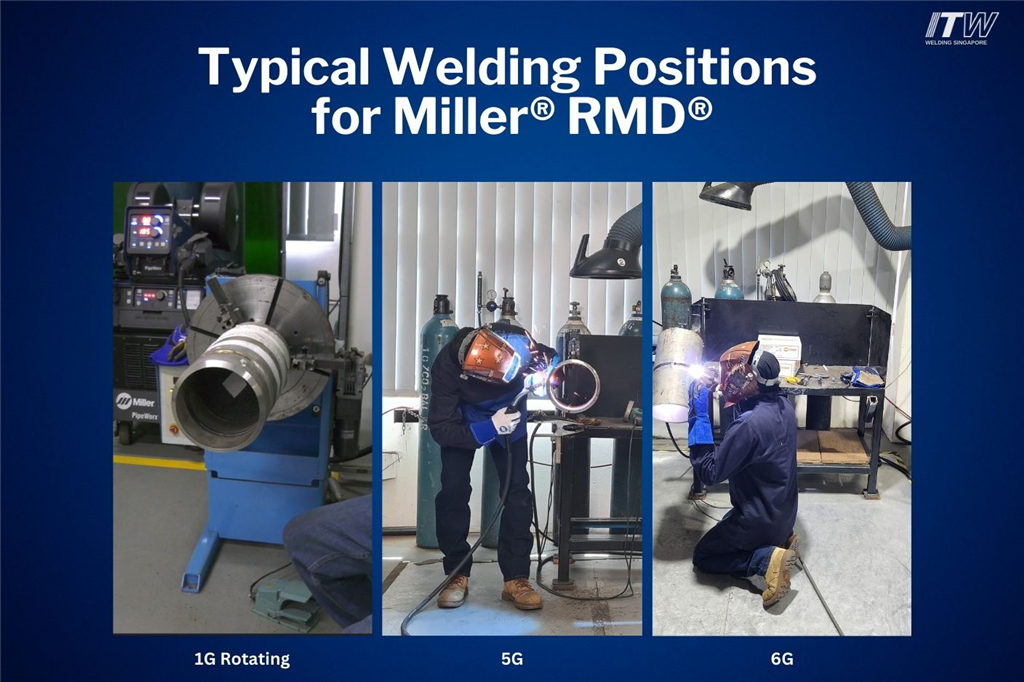
What diameter of filler metal should be used with the RMD® process?
For 1G rotating applications, 0.9mm, 1.0mm or 1.2mm diameter wires are recommended. For 5G or 6G positions, we recommend 0.9mm or 1.0mm diameter wires instead, especially if the welder is new to the RMD® process. The smaller wire diameter will provide easier weld puddle control and welders can complete the training and qualifications quickly.
Can the RMD® process weld a pipe from root to cap?
The RMD® process is designed for root pass welding of a pipe and can replace the traditional TIG process. Because RMD® delivers a higher deposition rate, the root pass is thicker, and the hot pass can be eliminated. The fill and cap passes can be completed with a Pulsed MIG process that is available on any Miller® welding machine that offers the RMD® process. As such, a welder can use one filler wire, one shielding gas and one welding machine to weld a pipe from root to cap. This reduces changeover time and improves the user experience.
Has the RMD® no back purge process been implemented in projects?
This process has been used by welding contractors in North America, Europe, Middle East, and Asia, and is accepted by the clients of the projects. After visual inspection, clients will require the welded test coupons to be sent for a variety of non-destructive and destructive tests as per relevant codes. This may include radiographic test, corrosion test, bend test, tensile test, and impact test. If you would like to view any of the test reports, kindly send us a request for more information.
Do you provide training for welders on the RMD® process?
We offer a comprehensive train-the-trainer program to our customers in Southeast Asia. The program will include a detailed timeline and the resources needed to make the training and procedure qualification a success. As your partner, we are also able to advise on how to successfully implement RMD® in production so that you can reap the full benefits of this weld process.
What is the minimum pipe diameter for RMD® welding in the 5G or 6G position?
For welding contractors who are new to this process, they will usually start welder training and procedure qualification on an 8-inch pipe. As welders get more familiar with the RMD® process, they can easily weld 6-inch pipes as well. We have also heard of contractors who use RMD® on 2-inch pipes, but that typically requires a lot of experience.
If you have any more questions on the welding of stainless pipes with RMD® and no back purge, please contact us at SGOffice@MillerWelds.com