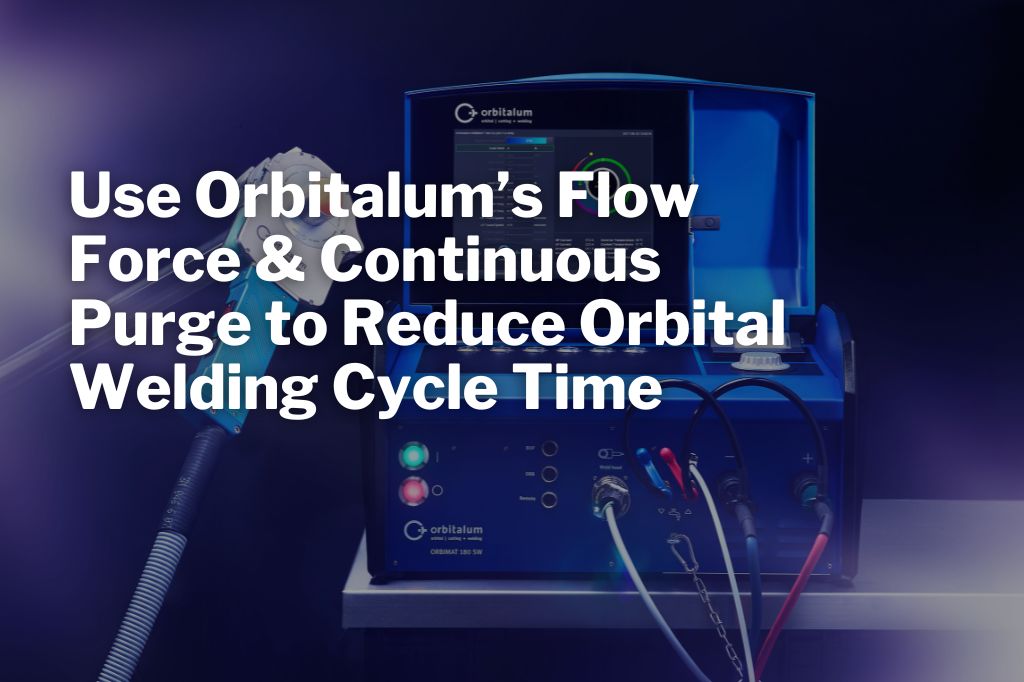
In general, the orbital welding cycle time consists of a few stages: Cleaning, tacking, pre-purge, orbital welding, post-purge, cleaning. Traditionally, it is common practice to use a 30 seconds pre-purge time and 30 seconds post-purge time. This amounts to 1 minute of purging per orbital weld joint. For 100 weld joints, this translates to 100 minutes spent on purging. What if the total purge time can be reduced to increase welding throughput? With Orbitalum’s Digital Gas Panel, this is possible.
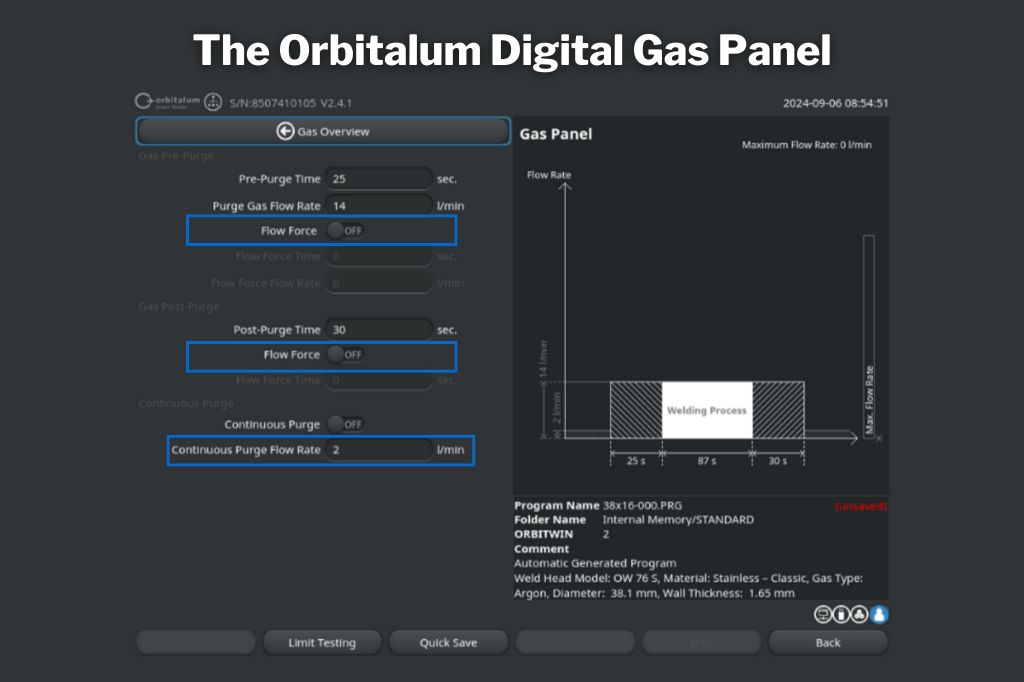
Orbital welding machines from Orbitalum, such as the flagship OM180SW, have a built-in mass flow controller. The shielding gas flow rate and time is digitally controlled by the welding machine via the Digital Gas Panel. On the Digital Gas Panel, you will also see 2 unique features known as Flow Force and Continuous Purge. These features help to reduce total purging time.
- Flow Force reduces the amount of time required for pre-purge and post-purge by flooding shielding gas into the weld head at an accelerated rate.
- With Continuous Purge, the shielding gas continuously flows into the weld head to prevent oxygen from entering the weld head even during non-productive times such as cleaning. This helps to reduce the pre-purge time.
Below, you will see a video of Flow Force and Continuous Purge in action. In this example, we managed to reduce the total welding cycle time by 32%. If you are interested to learn more, do reach out to sherwyn.tan@orbitalum.com