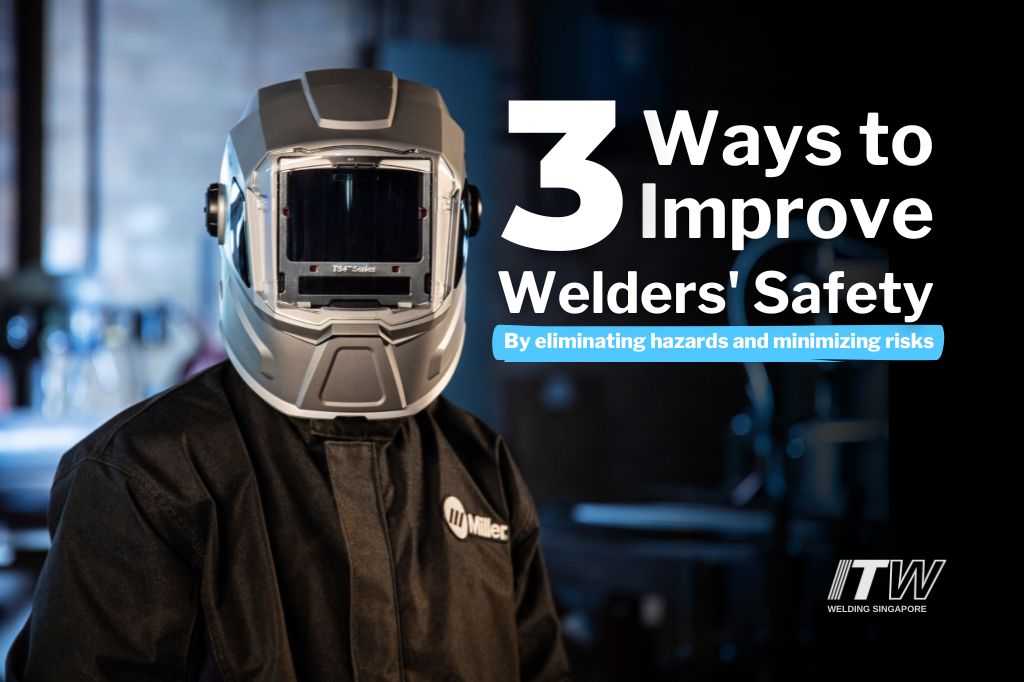
Based on the Hierarchy of Controls, the most effective method to protect welders from hazards and reduce risk of injury or death is to eliminate the hazards. The wearing of Personal Protective Equipment (PPE), such as welding helmets and respirators are the least effective because they only help to reduce exposure to hazards.
In this article, we will elaborate on three common hazards that welders face, and how the latest welding technology from Miller Electric can help eliminate hazards and minimize risks. If you are responsible for the safety of welders, or accountable for the successful and safe completion of projects, you may find this article relevant.
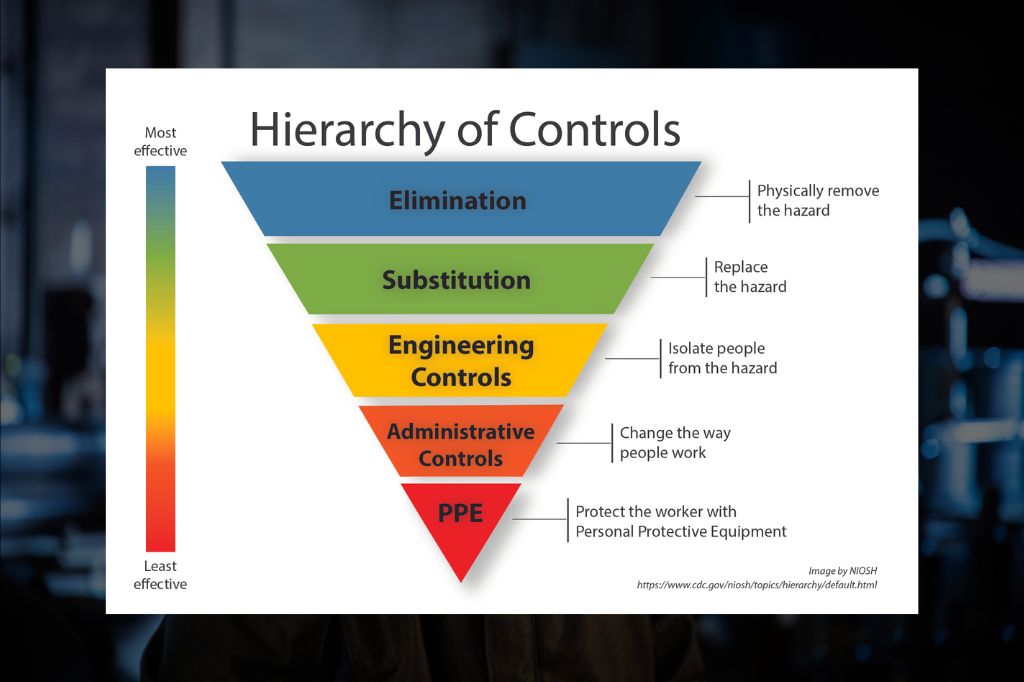
1. Minimize the Risk of Burn Injuries
Before welding, welders may be required to perform preheating, as specified in the Welding Procedure Specification (WPS). Usually, preheating is done via flame heating with a propane torch. The typical preheat temperature ranges between 80oC to 150oC. Depending on the size and thickness of the part to be heated, it may take hours to reach the required preheat temperature. During this period, welders are exposed to an open flame in the jobsite, which subjects them to two key risks. Firstly, the risk associated with burn injuries, fires and explosions is high. Secondly, flame heating generates high noise levels and large quantities of toxic by-products. Long term exposure can result in noise-induced deafness and respiratory illnesses if welders are not equipped with the proper PPE.
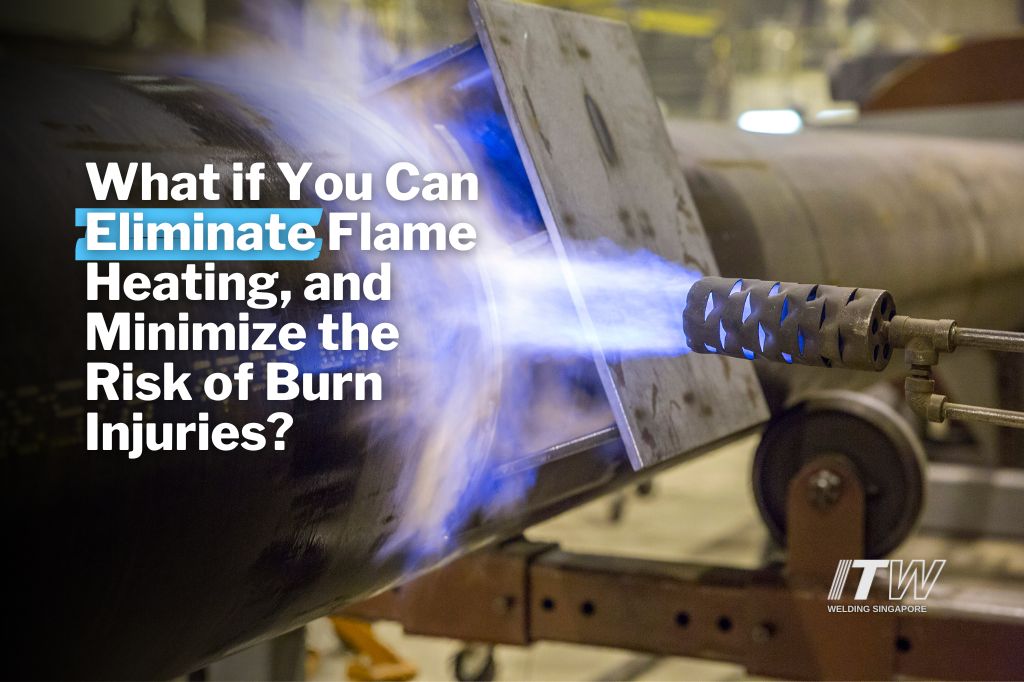
The induction heating system from Miller Electric is a safer and faster alternative for preheating. For example, the Miller® ProHeat™ 35 has been used to preheat pipes, tubular structures, vessels, I-beams, and excavator buckets, just to name a few. Since induction heating is based on the concept of electromagnetism, it is a much safer process compared to flame heating since no open flame is used. There are also no toxic by-products or excessive noise produced, unlike flame heating. If induction heating is implemented, welders will be able to work in a much safer and comfortable environment.
2. Minimize the Risk of Asphyxiation
When welding corrosion resistant alloys, such as stainless-steel pipes, welders must purge the inside of the pipe before TIG welding. A commonly used purging gas (also called backing gas) is Argon, an inert gas. Argon displaces the atmospheric air and oxygen inside the pipe, thereby protecting the weld metal and parent material from oxidation during the welding process. This in turn maintains the corrosion resistance of the welded stainless-steel pipe.
Since welders are potentially exposed to an oxygen-deficient atmosphere, adequate risk control measures must be in place to reduce the risks. Examples include equipping welders with portable gas detectors, providing proper training on purging techniques and safety procedures, and ensuring adequate ventilation. Despite these safety measures, there have been reports in Singapore and United States of America of welders who have died of asphyxiation. Because purging gas is odorless, tasteless, and colorless, suffocation by inert gas can occur rapidly without any warning signs.
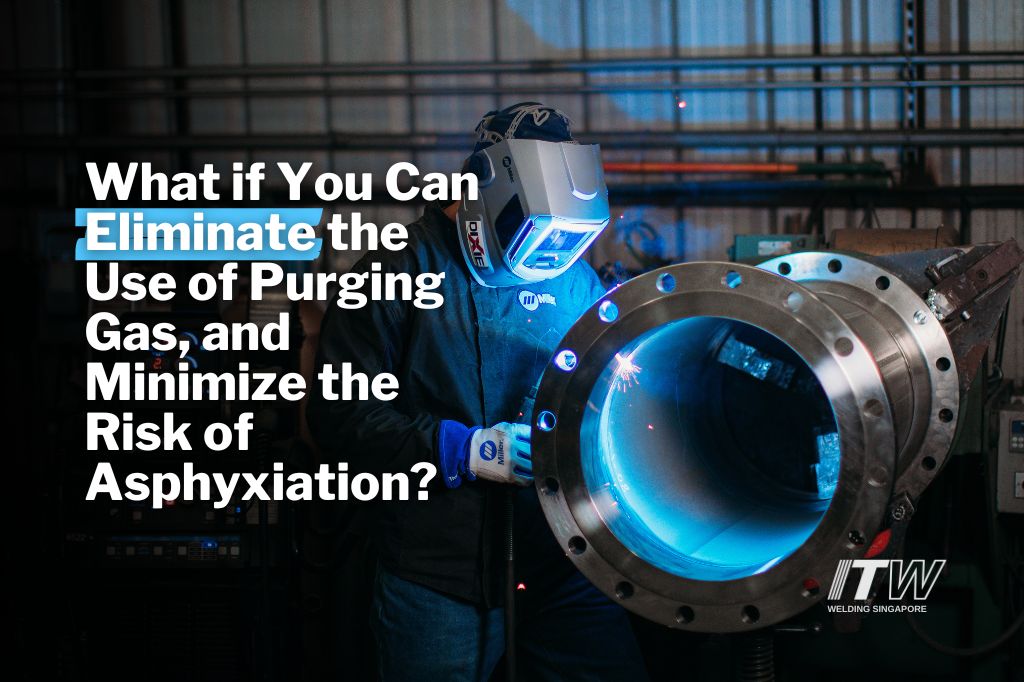
By changing the TIG welding process to the Miller® Regulated Metal Deposition (RMD®) process, it is possible to eliminate the need for purging gas when welding stainless-steel pipes, such as Grade 304 and 316. RMD® is a modified short-circuit GMAW process that is primarily designed for the root pass welding of pipes. Because RMD® provides a precisely controlled metal transfer, the shielding gas exists the GMAW gun relatively undisturbed. The shielding gas pushes through the open root of the pipe and displaces the atmospheric air and oxygen in the pipe. This prevents oxidation on the back side of the weld. Testing has shown that stainless-steel pipes that have been welded with RMD® without purging gas can still retain the corrosion resistance requirements expected by clients.
3. Minimize the Risk of Slips, Trips and Falls
Based on the Singapore Workplace Safety and Health Report 2022, the leading cause of workplace injuries is Slips, Trips and Falls (STF). STF can result in sprains, strains, fractures, head injuries and even deaths. As such, many companies employ risk control measures, such as the installation of handrails, practicing good housekeeping etc. to reduce the occurrences of STF.
For a welder working in an expansive jobsite, the risk of STF is very real. Due to the nature of their job, it is not uncommon to see welders climbing up ladders or crawling through small spaces to get to the weld joint. This means that the welding machine is usually placed far away from the point of welding. If process or parameter changes need to be made, the welder will have to walk back to the welding machine to make the adjustments. An extensive study conducted by Miller Electric found that a welder makes an average of four trips to the welding machine during one shift. All this unnecessary walking can significantly increase the chances of STF-related injuries.
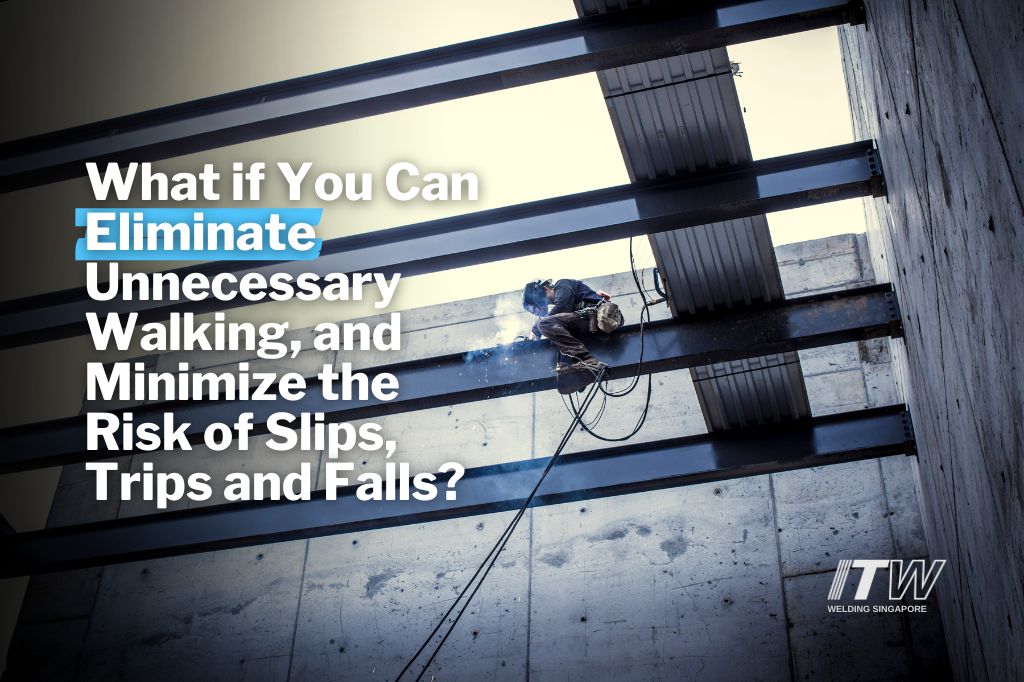
To address this challenge, Miller Electric developed the ArcReach® Technology that will allow welders to make all process and parameter changes at the point of welding, without the use of control cables. This technology eliminates all unnecessary walking in the jobsite, thereby improving jobsite safety. An additional benefit of employing ArcReach® Technology is an improvement in productivity, since welders spend more time welding, instead of walking.
Eliminate the Hazards and Minimize Welders’ Risks Today
Welders face a multitude of risks daily. Besides the obvious welding-related risks, such as exposure to the welding arc and welding fumes, welders also encounter many hazards on the jobsite. If you want to keep your welders safe and complete projects on schedule, reach out to us at SGOffice@MillerWelds.com for a discussion.