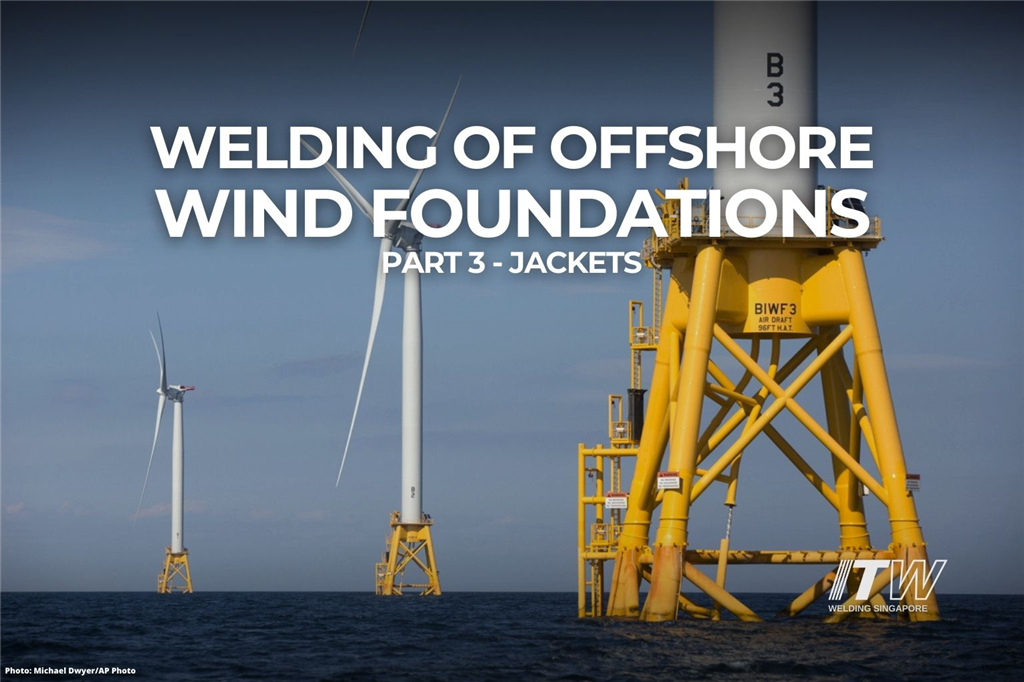
The Welding of Offshore Wind Jacket Foundations
In part two of this series, we described the welding of offshore wind monopiles and the welding challenges that fabricators face. In this article, we will elaborate on the welding of offshore wind jacket foundations.
Typical Fabrication Process of Offshore Wind Jacket Foundations
A jacket structure is composed of multiple legs and braces that are made from high-strength tubular steel (typically S355, S420 and S460 grade or equivalent). When installed offshore, the legs are anchored to the seabed with piles, which are also high-strength tubular structures. The legs and piles are prefabricated from large steel plates that are rolled into cylindrical or conical shapes, tack welded and preheated, followed by longitudinal and circumferential welding via the Submerged Arc Welding (SAW) process. This is very similar to the offshore wind monopile fabrication process that was described in part two of this series.
Assembly of the legs and braces typically take place in an open yard that is located near the load-out area. During the assembly process, there are generally two types of weld joints, circular joints, and TKY-node joints. Circular joints arise when the ends of two steel tubes meet, while TKY-node joints occur when the end of a steel tube meets the surface of another steel tube. After the jacket foundation is fabricated, it undergoes surface treatment and is transported to the offshore wind farm site for installation.
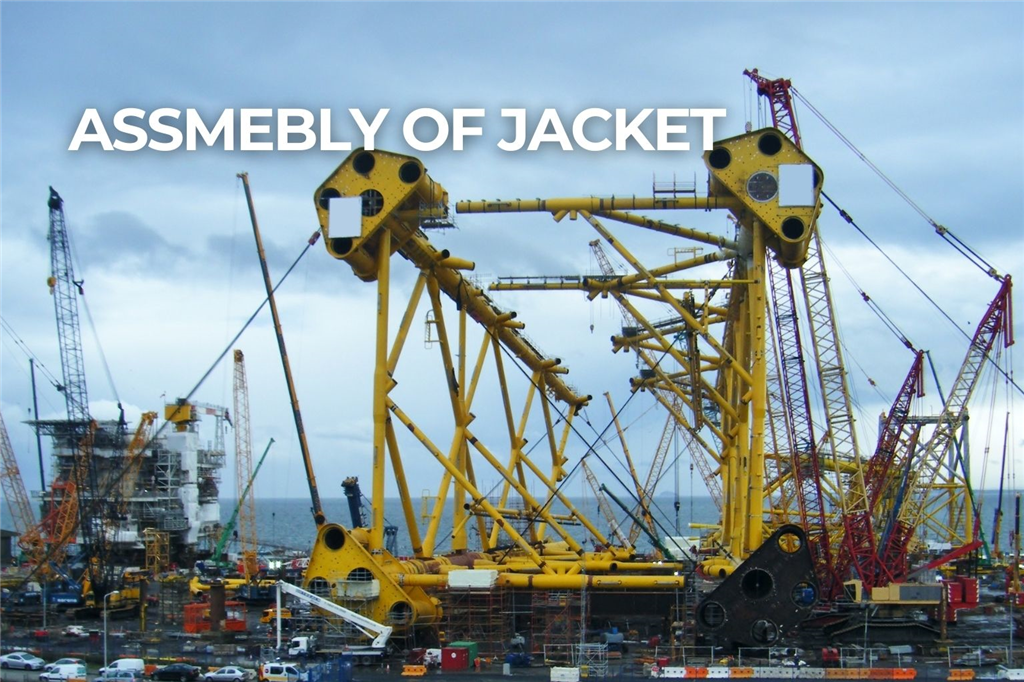
Typical Welding Challenges when Fabricating Offshore Wind Jacket Foundations
Many of the welding productivity and quality issues that fabricators will face when prefabricating the jacket legs and piles will be very similar to those that they will encounter when fabricating monopiles. This has been touched on extensively in part two of this three-part series. For the remaining portion of this article, we will focus on the welding challenges that fabricators will face when assembling the legs and braces in the open yard.
Mitigating Safety Concerns
Before welding takes place, welders usually need to perform preheating. Currently, most fabricators use resistance heating or flame heating to perform this task. Resistance heating uses hot ceramic pads that can cause burn injuries, and the pads stay hot long after the workpiece has been brought to temperature. This makes handling the ceramic pads a real safety concern for the welders. In addition, the ceramic insulation that is often used in resistance heating is a carcinogen. As for flame heating, besides the obvious safety concerns, flame heating can be a very slow process when used in the open yard because a lot of heat is lost to the surrounding. Because of these safety and productivity concerns, some fabricators have switched to the induction heating process because the heating cables and wraps do not get hot, and there are no toxic by-products from the process.
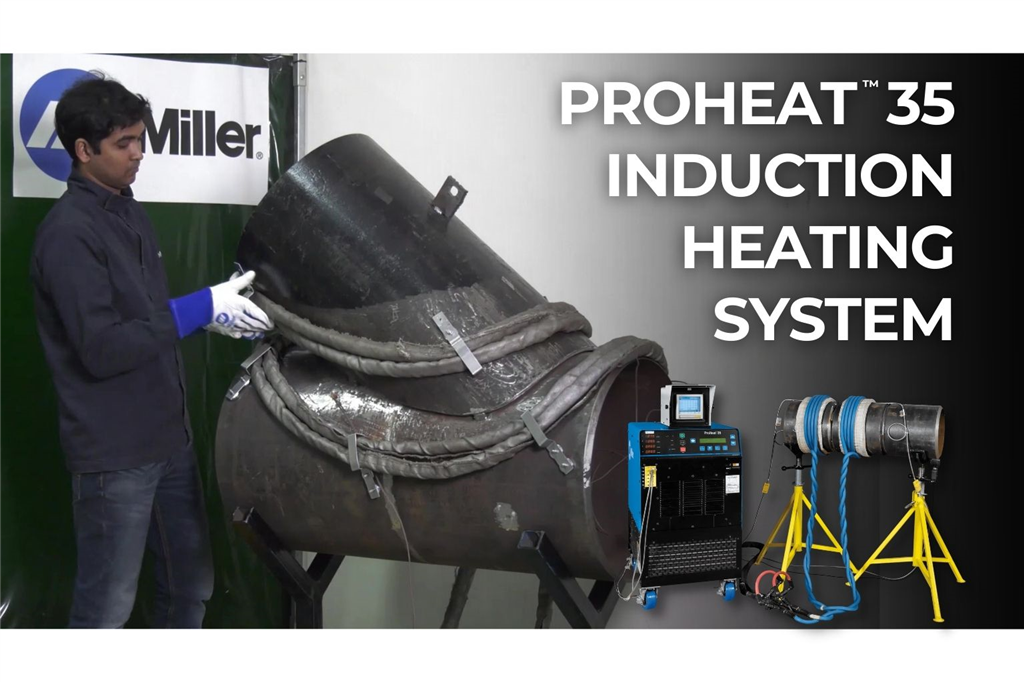
When working in the open yard, most welders will be welding at height. Depending on the existing welding procedures and the welding position, welders may have to make welding process and parameter changes. This means that welders have to walk back to the welding machine to make the necessary changes, which significantly increases the risk of slips, trips and falls on the jobsite. To improve jobsite safety, fabricators can select welding solutions that provide point-of-use remote control capabilities, such as Miller® ArcReach®.
Achieving Welding Productivity Goals
Miller® ArcReach® not only improves jobsite safety but can also help fabricators to meet their welding productivity targets. Because welders no longer need to walk unnecessarily around the jobsite, they can spend more time welding.
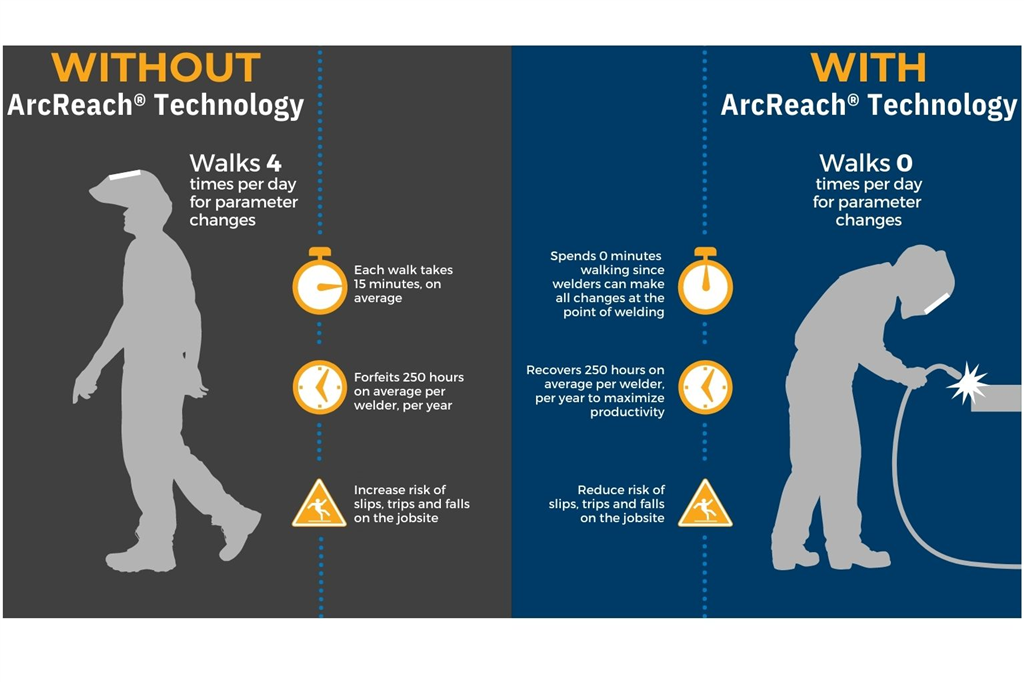
Another aspect that will significantly affect the welding throughput is the welding process that is selected for the job. Offshore fabricators in Southeast Asia tend to use different welding processes to weld the circular joints and TKY-node joints in the open assembly yard. The three most common practices are Stick welding, a combination of Sticking welding and Gas Shielded Flux Cored Arc Welding (FCAW-G) and Self Shielded Flux Cored Arc Welding (FCAW-S). Stick welding is a very slow process because of the low deposition rate and the constant need for welders to change out the welding electrode. However, Stick welding is predominant because it has a low upfront cost, and all welders are familiar with this process. Some fabricators try to improve the productivity by using a combination of Stick welding and FCAW-G, however, it is very time-consuming to arrange gas cylinders and welding habitats to be delivered and erected in the open yard environment. For welding in the open yard, FCAW-S is the most ideal process because it does not require any special setup and preparation, and it can be used to weld from root to cap. However, the high upfront cost and the need to train and qualify welders in the FCAW-S process are potential stumbling blocks for some fabricators.
No matter which welding process fabricators decide to select for their project, Hobart® has developed a range of products for the fabrication of offshore wind jacket foundations.
– Stick: Hobart® PipeMark 816, Hoballoy® 8018C3
– FCAW-G: Hobart® 12J, Hobart® 811K2
– FCAW-S: Fabshield® 81N1, Fabshield® X80
In addition, ITW Welding Singapore has also established comprehensive training and familiarization programs to help fabricators in Southeast Asia who want to adopt new welding processes, such as changing from Stick welding to FCAW-S process.
Meeting Stringent Mechanical Requirements
Over the years, the offshore wind jacket foundation is being deployed in harsher environments and deeper waters. As such, it is understandable that the design has changed, and clients have higher mechanical requirements. A common feedback from fabricators is a need for Crack Tip Open Displacement (CTOD) requirements at -20oC. This usually means that fabricators must either retest their existing filler metals to understand if they meet the new requirements from clients, or fabricators must requalify new filler metals all together. Retesting and requalifying is always a hassle for fabricators since it involves time and money. Because it is a tedious process, fabricators should work with a welding manufacturer that has a long history of producing high-quality filler metals, such as Hobart®. Fabricators should also ask their welding supplier for references, approvals and relevant third-party test reports when evaluating the right filler metal for the job.
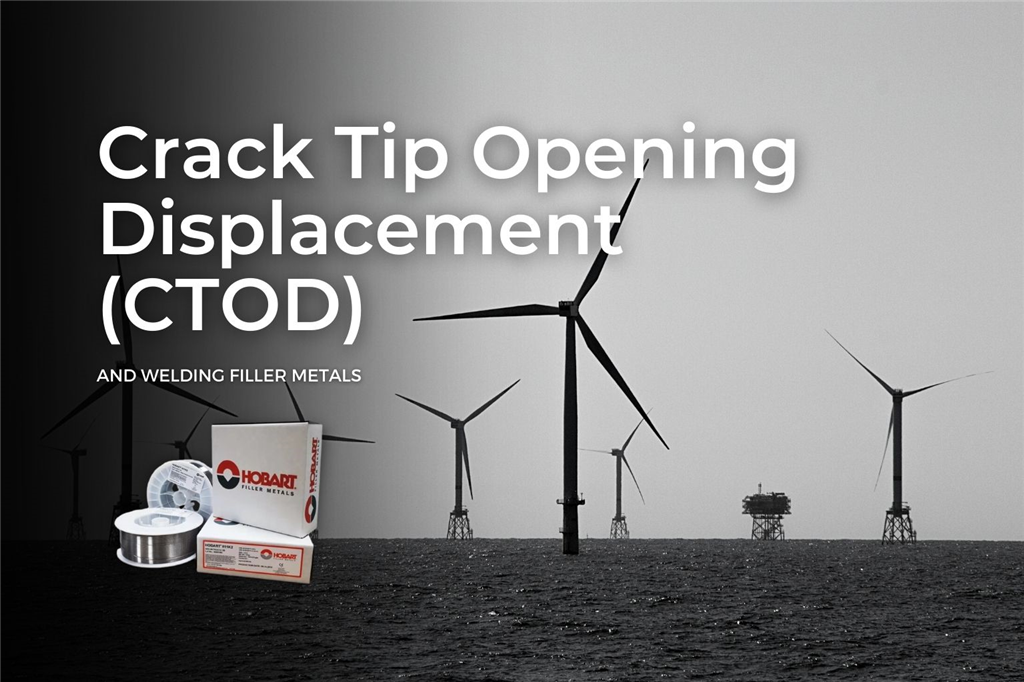
We’ve come to the end of this three-part series where we share about welding of offshore wind foundations. If you would like to have a further discussion on any of the points mentioned, or would like to see a demonstration of our welding solutions, reach out to us at SGOffice@MillerWelds.com